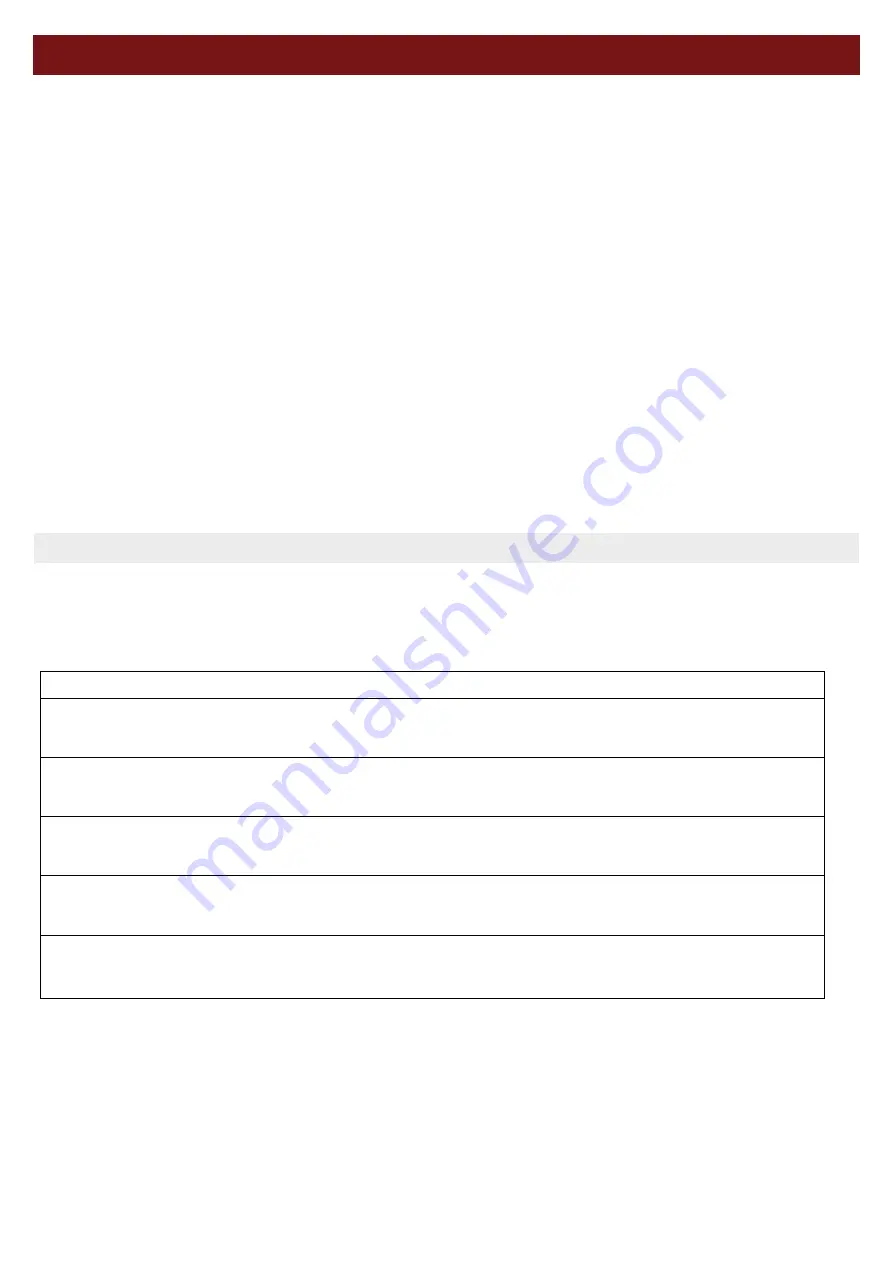
10
11
USER MANUAL - 230 VAC MULTIFUNCTION CONTROL UNIT - 051D
GUIDED CONFIGURATION
In this section it is possible to set the motor working time or the obstacle detector threshold. These procedures can be identified
by letter P: it is always possible to manually change the values at the end of the programming.
BEFORE STARTING:
- Check the gate: it must be fully closed
- Check that the motor rotation is correctly performed: both motors must open during the opening movement; both motors must
close during the closing movement.
- Be sure to have a START device: for example a transmitted stored as (symbol) or a key-switch connected to terminal block 9 with
value
E1
=
Go
(START).
- In order to program the control unit without the slowdown working time, set:
A2
or
B2
=
0.0
and then proceed with programming.
During the configuration phase, on the display you will se the parameter you are setting, for example, if the display shows
A1
it
means that the control unit is setting parameter
A1
(STANDARD TIME - MOTOR A).
STORE A TRANSMITTER AS START DEVICE
1. Select parameter
r1
using key (
←
) or (
→
).
2. After a few seconds (
=_
) will appear on the display
3. Keep the button of the transmitter you want to store pressed: the display shows (
=._
)
4. Press KEY (+): the display shows (
=
1
). Your transmitter has been successfully stored in position 1 in the control unit’s memory
(display
=
2
means position 2 in the memory, display
=
3
means position 3, etc up to 99).
4a. If the display shows (
=.
) your transmitter has not been stored.
4b. If the display does not show (
=.
), the control unit did not receiver your transmitter (E.G.: different frequency compared to
the receiver), or the radio receiver is faulty.
P1
/
P2
GUIDED CONFIGURATION: 1/2 MOTOR/S
P1
: configuration 1 motor mode
L5
=
Y
, standard working time
A1
, motor A slowdown time
A2
and auto-close time
F0
. To
proceed with configuration
P1
read lines
A1
,
A2
and
F0
. If you disabled the slowdown time of the motor, skip
A1
and/or
b1
.
P2
: motor A and motor B standard time
A1
/
b1
, slowdown time
A2
/
b2
and auto-close time
F0
configuration. If you disabled
the slowdown time of one of the motors or both, ignore
A1
and/or
b1
.
_ _
After 2 seconds two dashes will appear on the display. Perform a START command to start
A1
configuration.
A1
You are working on motor A STANDARD TIME. Motor A starts the opening movement. When the leaf controlled
by motor A has completed 90% of the opening movement, send another START command. The control unit will
automatically move to
A2
configuration step
A2
You are working on motor A SLOWDOWN TIME. Motor A slows down. It is advisable to wait 2-3 seconds when
the leaf has come to a completely open position and the motor ended the opening movement, then issue a new
START command. The control unit will automatically move to
b1
configuration step
B1
You are working on motor B STANDARD TIME. Motor A stops and motor B slows down. When the leaf controlled
by motor B has completed 90% of the opening movement, send a START command. The control unit will auto-
matically move to
b2
configuration step
B2
You are working on motor B SLOWDOWN TIME. Motor B slows down. It is advisable to wait 2-3 seconds when
the leaf has come to a completely open position and the motor ended the opening movement, then issue a new
START command. The control unit will automatically move to
F0
configuration step
F0
You are working on AUTO-CLOSE TIME
F0
. Both motors are idle. The display will show
F0
, then the seconds
counting. Count the desired time you want your automation to wait before starting the auto-closure operation,
then press the START command
> Guided configurations count the same time for opening and closing movements.
> If a leaf perform the SLOWDOWN operation only during opening movement (and not during the closing movement)
follow this procedure:
- Select
A1
using keys (
←
) or (
→
)
- Decrease
A1
value by 1 second using key (-)
- Select
A2
using keys (
←
) or (
→
)
- Increase
A2
value by 3 seconds using key (+)
- Perform a complete cycle
If the slowdown movement is performed, your configuration has come to an end. If not, repeat this procedure. Use the same pro-
cedure for motor B, if needed.