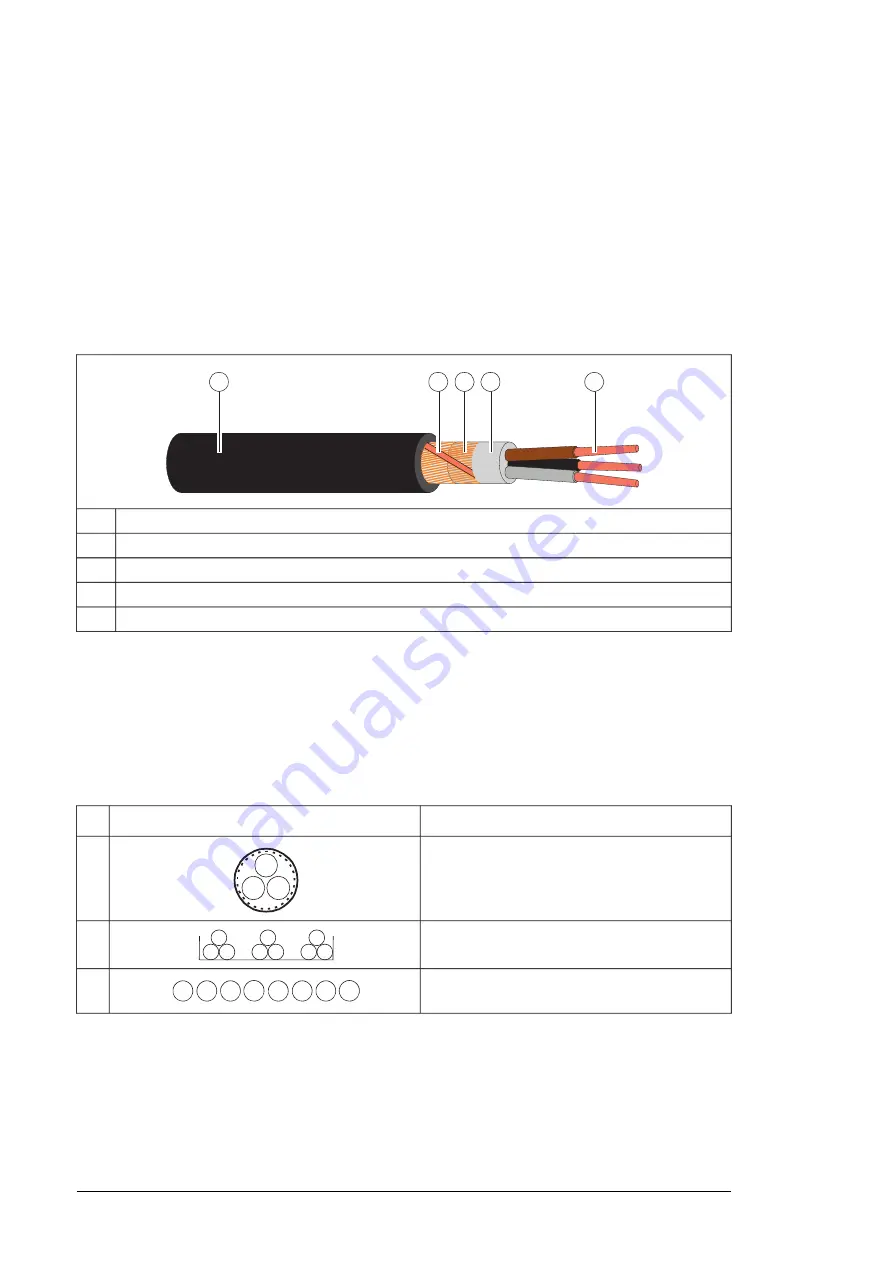
Generator cable shield
If the generator cable shield is used as the sole protective earth conductor of the generator,
make sure that the conductivity of the shield is sufficient. See subsection
above, or IEC 61800-5-1.
To effectively suppress radiated and conducted radio-frequency emissions, the cable shield
conductivity must be at least 1/10 of the phase conductor conductivity. The requirements
are easily met with a copper or aluminum shield. The minimum requirement of the generator
cable shield of the converter is shown below. It consists of a concentric layer of copper wires
with an open helix of copper tape or copper wire. The better and tighter the shield, the lower
the emission level and bearing currents.
1
3
4
5
2
Insulation jacket
1
Helix of copper tape or copper wire
2
Copper wire screen
3
Inner insulation
4
Cable core
5
■
Single core vs multicore cables in grid cabling
Use symmetrical grid cabling. Asymmetry leads to unequal current distribution between the
conductors which may cause disturbances and fault trips. To avoid asymmetry, use
symmetrical multicore (three-phase) cables where possible. Single core cabling is also
allowed if the cables are grouped symmetrically.
The table below shows three possible cabling options.
Description
Layout
No.
Multicore cabling (recommended). See subsection
for the possible con-
structions of the PE (protective earth/ground).
1
Single core cables in trefoil (preferable single core
cabling option).
L1
L3
L2
L2
L1
L3
L3
L2
L1
2
Single core cables laid flat.
PE
L1
L3
L2
PE
L1
L3
L2
3
■
Additional US and Canada requirements
Use copper, copper-clad aluminum or aluminum conductors. Use conductors rated for 90 °C
(194 °F) only.
Run the cabling in metallic conduits, or use type MC continuous corrugated aluminum armor
cable with symmetrical grounds or shielded power cable for the generator cables if metallic
conduit is not used.
54 Planning the electrical installation
Summary of Contents for ACS880-77CC
Page 1: ...ABB WIND TURBINE CONVERTERS ACS880 77CC wind turbine converters Hardware manual...
Page 2: ......
Page 4: ......
Page 10: ...10...
Page 17: ...5 1 3 4 6 8 7 2 Safety instructions 17...
Page 22: ...22...
Page 40: ...40...
Page 60: ...60...
Page 73: ...2a 3b 4c 5 Air flow direction is towards the converter module Maintenance 73...
Page 104: ...104...
Page 108: ...Description CAN bus connection XCAN XCAN 108 BCU x5 control unit...
Page 112: ...112 Dimension drawings...
Page 113: ...Dimension drawings 113...
Page 114: ...114 Dimension drawings...
Page 126: ...126...