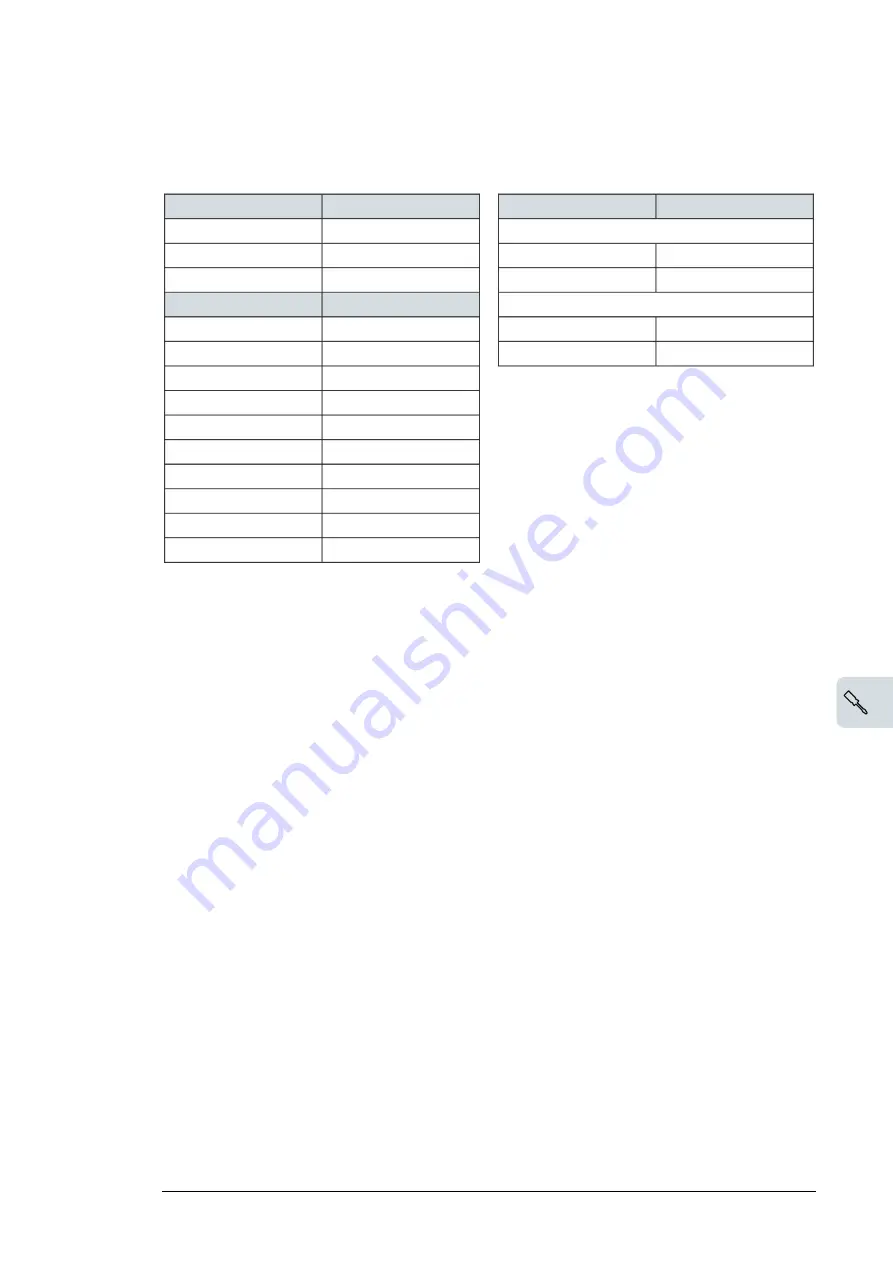
■
Connections to the control unit
Connect the fiber optic, power supply and BGDR cables to the control unit as follows:
BCU control unit
ZINT/SOIA
BCU control unit
BPOW
Drive module 1
XPOW:1 (+24VI)
X3:1
V1T
ZINT: V1; SOIA: V10
XPOW:2 (GND)
X3:2
V1R
ZINT: V2; SOIA: V20
-
X3:3 (not used)
Drive module 2
BCU control unit
BGDR
V2T
ZINT: V1; SOIA: V10
(connector XSTO OUT)
Drive module 1
V2R
ZINT: V2; SOIA: V20
5 (IN1)
X7:1
6 (SGND)
X7:2
7 (IN2)
X8:1
8 (SGND)
X8:2
(connector XSTO OUT)
drive module 2
5 (IN1)
X7:1
6 (SGND)
X7:2
7 (IN2)
X8:1
8 (SGND)
X8:2
Connecting the control cables to the terminals of the
control unit
■
Control cable connection procedure
1.
Route the cables to the control unit.
2.
Strip the cable ends and conductors. When connecting to the drive I/O, use electrical
tape or shrink tubing to contain the strands. Elsewhere, twist the outer shield strands
into a bundle, crimp a lug onto it and connect it to the nearest chassis grounding point.
3.
Connect the conductors to the appropriate detachable terminals of the control unit, see
section
Default I/O connection diagram (page 110)
Note:
Keep any signal wire pairs twisted as close to the terminals as possible. Twisting the
wire with its return wire reduces disturbances caused by inductive coupling. Keep the shields
continuous as close to the terminals of the control unit as possible. Leave the other end of
the shield unconnected or ground it indirectly via a few nanofarads high-frequency capacitor,
eg, 3.3 nF / 630 V. The shield can also be grounded directly at both ends if they are in the
same ground line with no significant voltage drop between the end points.
Wiring the microswitches of the fuses
Wire the microswitches of the drive input fuses to the DIIL input as shown below or to an
external switch for stopping the drive in case of a blown fuse.
Electrical installation 99
11
Summary of Contents for ACS880-04FXT
Page 1: ... ABB INDUSTRIAL DRIVES ACS880 04FXT drive module packages Hardware manual ...
Page 2: ......
Page 4: ......
Page 40: ...40 ...
Page 54: ...54 ...
Page 82: ...82 ...
Page 86: ...M10 86 Electrical installation ...
Page 106: ...106 ...
Page 118: ...118 ...
Page 122: ...122 ...
Page 132: ...132 ...
Page 136: ...136 ...
Page 158: ...158 ...
Page 160: ...Standard configuration IP00 UL Type Open 160 Dimension drawings ...
Page 161: ...Drive module with optional support brackets IP00 UL Type Open Dimension drawings 161 ...
Page 163: ...Mounting plate opening 3AXD50000038119 Dimension drawings 163 ...
Page 164: ...3AXD50000038119 164 Dimension drawings ...
Page 182: ... Declaration of conformity 182 The Safe torque off function ...
Page 183: ...The Safe torque off function 183 ...
Page 184: ...184 ...