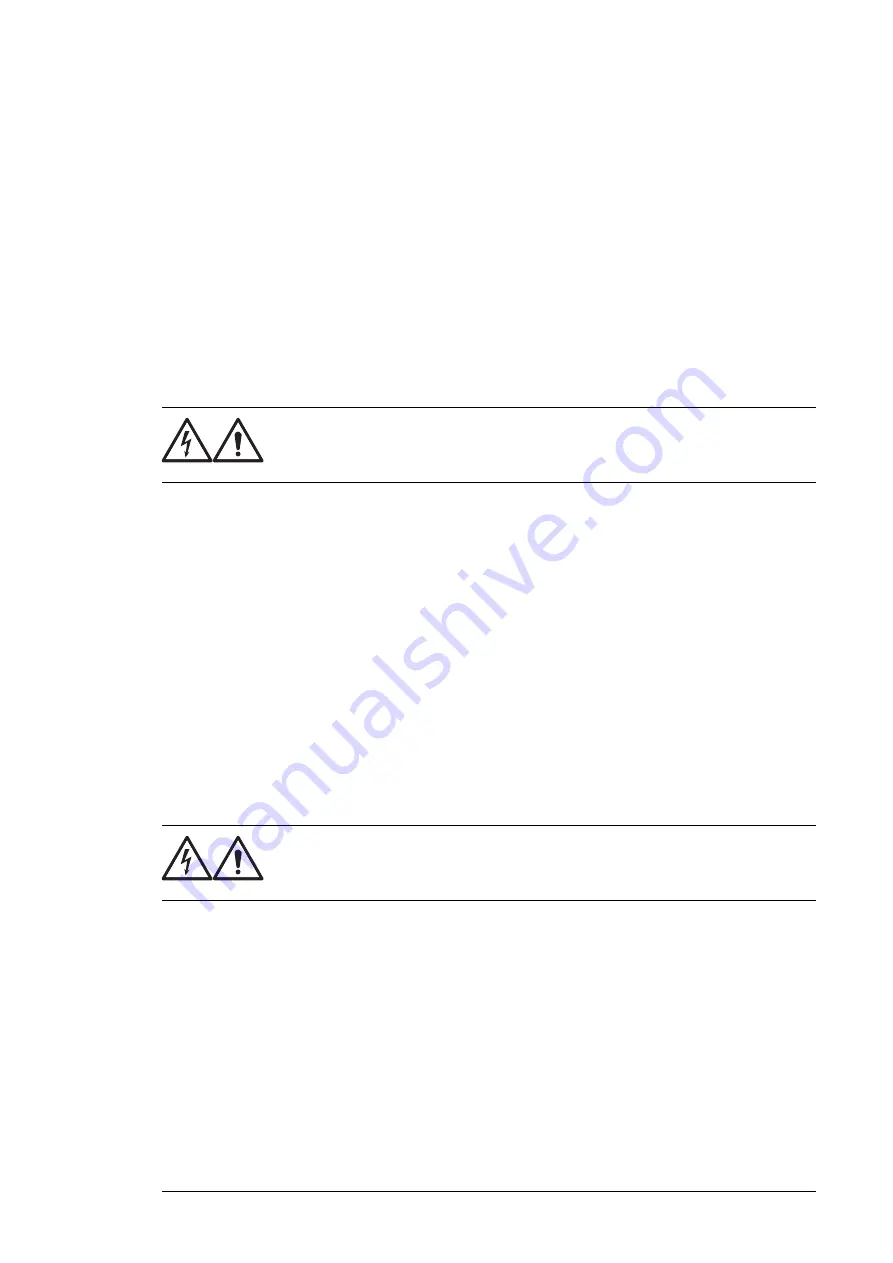
Replacing the control unit
See
BCU-02/12/22 control units hardware manual
(3AUA0000113605 [English]). The spare
part control units are of type BCU-22. It can be used for replacing the BCU-02.
Reduced run
A “reduced run” function makes it possible to continue operation with one drive module if
the other module is out of service, for example because of maintenance work. In principle,
reduced run is possible with only one module, but the physical requirements of operating
the motor still apply; the remaining module in use must be able to provide the motor with
enough magnetizing current.
■
Starting reduced run operation
WARNING!
Obey the safety instructions of the drive. If you ignore them, injury or death,
or damage to the equipment can occur.
1.
Stop the drive and do the steps in section
Electrical safety precautions (page 15)
before
you start the work.
2.
If the control unit is powered from the faulty module, connect the control unit to another
24 V DC power supply. ABB recommends using an external power supply with
parallel-connected drive modules.
3.
Disconnect all cables from the module to be serviced and remove it from its bay. See
section
Replacing the standard drive module (page 130)
.
4.
Switch on the power to the remaining drive module.
5.
Enter the number of drive modules present into parameter
95.13 Reduced run mode
.
6.
Reset all faults and start the drive module. The maximum current is now automatically
limited according to the new drive module configuration. A mismatch between the number
of detected modules (
95.14
) and the value set in
95.13
will generate a fault.
7.
If the STO function is in use, validate it as described in chapter Safe torque off function.
■
Resuming normal operation
WARNING!
Repeat the steps described in section Electrical safety precautions. If you
ignore them, injury or death, or damage to the equipment can occur.
1.
Reinstall the module into its bay.
2.
Switch on the power to the drive module package.
3.
Enter “0” into parameter
95.13 Reduced run mode
.
4.
If the STO function is in use, validate it as described in chapter Safe torque off function.
Maintenance 131
Summary of Contents for ACS880-04FXT
Page 1: ... ABB INDUSTRIAL DRIVES ACS880 04FXT drive module packages Hardware manual ...
Page 2: ......
Page 4: ......
Page 40: ...40 ...
Page 54: ...54 ...
Page 82: ...82 ...
Page 86: ...M10 86 Electrical installation ...
Page 106: ...106 ...
Page 118: ...118 ...
Page 122: ...122 ...
Page 132: ...132 ...
Page 136: ...136 ...
Page 158: ...158 ...
Page 160: ...Standard configuration IP00 UL Type Open 160 Dimension drawings ...
Page 161: ...Drive module with optional support brackets IP00 UL Type Open Dimension drawings 161 ...
Page 163: ...Mounting plate opening 3AXD50000038119 Dimension drawings 163 ...
Page 164: ...3AXD50000038119 164 Dimension drawings ...
Page 182: ... Declaration of conformity 182 The Safe torque off function ...
Page 183: ...The Safe torque off function 183 ...
Page 184: ...184 ...