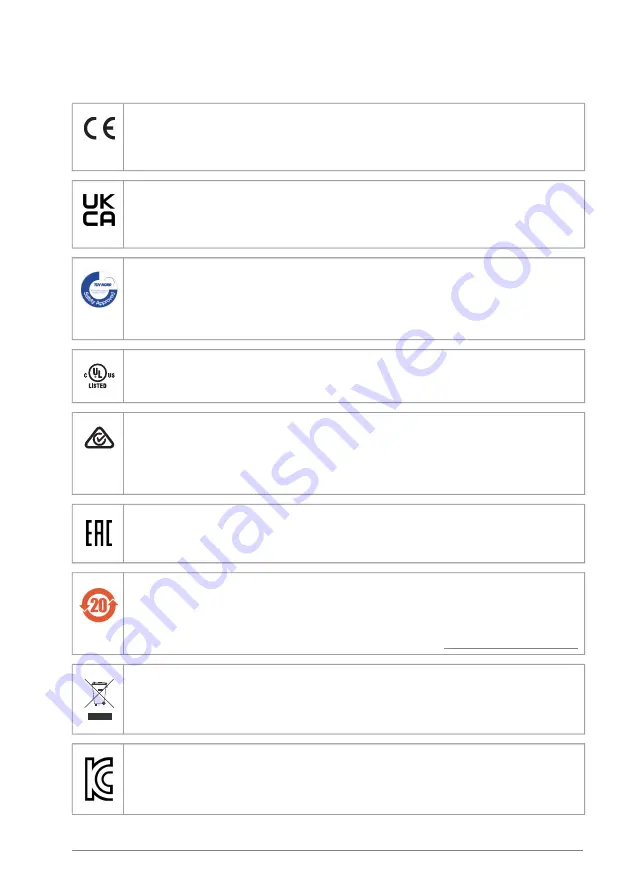
Markings
CE mark
Product complies with the applicable European Union legislation. For fulfilling
the EMC requirements, see the additional information concerning the drive EMC
compliance (IEC/EN 61800-3).
UKCA (UK Conformity Assessed) mark
Product complies with the applicable United Kingdom’s legislation (Statutory In-
struments). Marking is required for products being placed on the market in Great
Britain (England, Wales and Scotland).
TÜV Safety Approved mark (functional safety)
Product contains Safe torque off and possibly other (optional) safety functions
which are certified by TÜV according to the relevant functional safety standards.
Applicable to drives and inverters; not applicable to supply, brake or DC/DC con-
verter units or modules.
UL Listed mark for USA and Canada
Product has been tested and evaluated against the relevant North American
standards by the Underwriters Laboratories. Valid with rated voltages up to 600 V.
RCM mark
Product complies with Australian and New Zealand requirements specific to EMC,
telecommunications and electrical safety. For fulfilling the EMC requirements,
see the additional information concerning the drive EMC compliance
(IEC/EN 61800-3).
EAC (Eurasian Conformity) mark
Product complies with the technical regulations of the Eurasian Customs Union.
EAC mark is required in Russia, Belarus and Kazakhstan.
Electronic Information Products (EIP) symbol including an Environment Friendly
Use Period (EFUP).
Product is compliant with the People’s Republic of China Electronic Industry
Standard (SJ/T 11364-2014) about hazardous substances. The EFUP is 20 years.
China RoHS II Declaration of Conformity is available from
.
WEEE mark
At the end of life the product should enter the recycling system at an appropriate
collection point and not placed in the normal waste stream.
KC mark
Product complies with Korean Registration of Broadcasting and Communications
Equipment Clause 3, Article 58-2 of Radio Waves Act.
Technical data 123
Summary of Contents for ACS180
Page 1: ...ABB MACHINERY DRIVES ACS180 drives Hardware manual...
Page 2: ......
Page 4: ......
Page 12: ...12...
Page 36: ...36...
Page 41: ...4 Tighten the mounting screws Mechanical installation 41...
Page 58: ...58...
Page 76: ...76...
Page 90: ...90...
Page 130: ...Frame R0 130 Dimension drawings...
Page 131: ...Frame R1 Dimension drawings 131...
Page 133: ...Frame R3 Dimension drawings 133...
Page 134: ...Frame R4 134 Dimension drawings...
Page 142: ...142...
Page 162: ...Declarations of conformity 162 The Safe torque off function...
Page 163: ...The Safe torque off function 163...
Page 164: ...164 The Safe torque off function...
Page 165: ...The Safe torque off function 165...
Page 166: ...166...