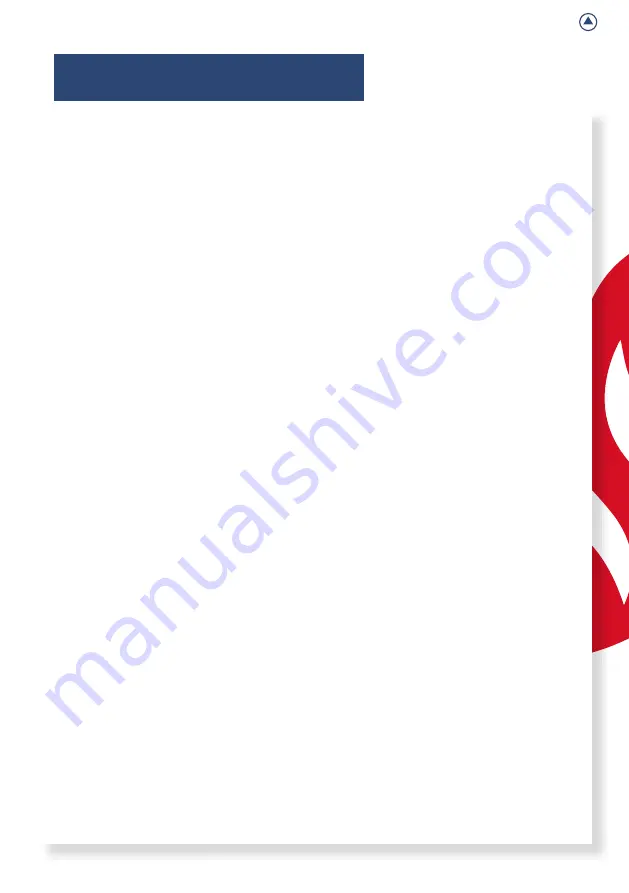
Attaching the bottom bar cont.
• All 6 rivets must be fitted and secured to prevent the curtain pulling through the
retainers.
• Drill through the fabric with a 6.5mm drill bit (the pre drilled bottom bar holes
should align and you should only be drilling the fabric) the bottom bar has been
factory assembled and no cutting or drilling is required. If the holes do not align
then you have not arranged the angles correctly. The rail at either end when
assembled has two 6.5mm holes drilled at 50mm and 100mm from each end. the
front and rear angle joints never align and must be fully overlapped to maintain
the rails strength. insert the M6 x 16 screw into the holes with the screwhead
on the 40 x 20 angle side roller side of the bottom bar. Attach the nyloc nut on
the opposite side and tighten accordingly. Proceed all the way along the bottom
bar until the bolts have been installed. If the screws are fitted the opposite way
round the nuts will hit the headbox and prevent the bottom bar pulling tight and
closing flush with the headbox.
• Carefully trim the excess material which is below the now assembled bottom
bar with a Stanley knife or similar, take extreme care as not to slip and cut the
curtain above the bottom bar.
Nylon cover caps are provided for the nyloc nuts.
• Curtains require a minimum bottom bar weight of 10kg per motor to close under
gravity failsafe. this allows for friction against the smoke seals and the fabric
rubbing on the guide surfaces.
• For assemblies where multi rollers are used the bottom bar is one continuous rail.
The curtain fabrics are overlapped. Where the fabrics overlap it is essential that
the fabric is pulled tight prior to the angles being secured together which will
provide a good seal to the overlapping fabrics. The fabrics should overlap true
and plum.
• Wide roller assemblies will deflect due to their own weight and curtain assembly
load. This deflection may cause the bottom bar to sag when fully retracted. To
overcome this remove the bottom bar screws in the middle of the rail and pull
the fabric through to replicate the sag at the head box. Re drill the curtain fabric
and replace the fixings accordingly. Do not over exaggerate this and check when
the bottom bar is in its fire safe position it still seals along the closing surface. If
this does not rectify the issue then packers can be inserted between the roller
tube and the fabric at the points of the sag. This will increase the circumference
of the roll and give an increase in the travel distance, off cuts of the fabric
should be used for the packers. Start small and slowly increase to achieve the
required retract position and the bottom bar pulls up flush with the head box, It
is possible to use both methods.
Summary of Contents for Evo1-MCP 1
Page 4: ...Back to contents Mechanical Installation Instructions 4...
Page 17: ...Back to contents Control Panel Lighting 17...
Page 20: ...Back to contents Motor Control Board Lighting 20...
Page 22: ...Back to contents General Overview Instructions 22...
Page 25: ...Back to contents Control Panel Wiring 25...
Page 30: ...Back to contents Motor Control Board Wiring 30...
Page 36: ...Back to contents Dip Switch Settings 36...
Page 39: ...Back to contents Override Switch Wiring to Control Panel 39...
Page 41: ...Back to contents Override Switch Wiring to Motor Control Board 41...
Page 44: ...Back to contents Control Panel Function Programming 44...
Page 54: ...Back to contents Optional Extras 54...
Page 58: ...Wiring of Optional Extras 58...
Page 64: ...Back to contents Fault Finding 64...
Page 67: ...Back to contents Maintenance Service 67...
Page 74: ...Back to contents Standard Drawings Headbox and Guides 74...
Page 84: ...Back to contents 44 0 1204 383839 info a1shutters co uk www a1sgroup com...