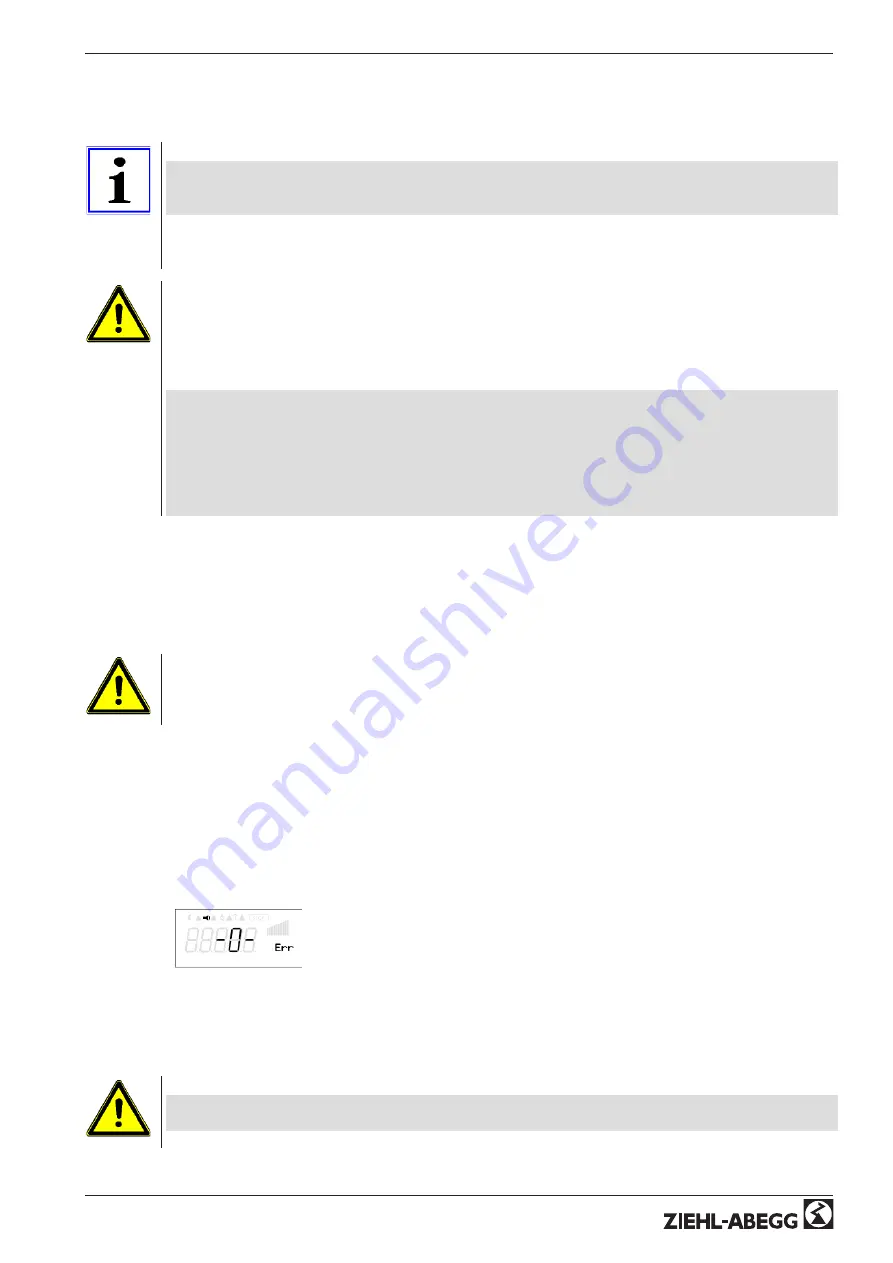
5.5 Connection EC-Controller output
5.5.1
Motor connection
Information
•
The motor leads are connected to the terminals: PE, U, V, W.
•
Connection hall-sensors (position indicators) to terminals: +15V, GND, H1, H2, H3.
•
The maximum length of the motor cable is 10 m, a longer cable is not permissible!
•
For each Controller can be attached only one motor.
•
Only the from Ziehl-Abegg given combination of controller and motor is permissible.
Attention!
•
EC-motors
never use direct at the line
. A electronic commutation unit EC-Controller is
necessary. Every EC-Motor needs a separate commutation unit.
•
The unit
´
s name shows the rated current, e.g. type EXDM2.7 (I
R
= 2.7A). The unit
´
s size shows
the max. motor current (see documentation of fans and motor). The EC-Controller
´
s rated
current must be every time higher than the max. motor current of the fan.
•
When commissioning, you must set the motor to the rated current stated on the rating
plate (
F
Motorsetup).
•
It is essential to check the direction of rotation of the fan during the initial commissioning.
To do this, note the direction of the arrow on the fan housing. We will not be responsible
under any circumstances for warrantee for damage caused because the direction of
rotation is wrong. A reversal of the direction of rotation could be programmed (
F
Motorsetup).
5.5.2
Disconnection between controller and motor (repair switch)
Ideally, a repair switch should be installed
before the controller
(supply line disconnect).
In the case of complete disconnection (entire load) after the controller, the enable (controller OFF /
ON) must be disconnected simultaneously. I.e., an additional control contact is needed. Switching on
the motor while simultaneously issuing the enable (ON) achieves secure energizing with low satura-
tion of the controller. For this a programming is necessary (
F
IO Setup Enable ON / OFF).
Attention!
When switching on the motor plus existing release: under certain circumstances, this can occur under
full modulation of the controller.
5.6 Motor protection
Motor protection is possible by connecting thermostats
“
TB
”
(thermal contacts) or thermistors
“
TP
”
(PTC).
A maximum of six individual thermistors (DIN 44081 or DIN 44082) may be connected in series to a
single device.
The unit switches off when a connected thermostat or thermistor has tripped the circuit (interruption
between both terminals
“
TB/TP
”
or
“
TK/PTC
”
. The unit then remains switched off. A programmed
fault-indicating relay is triggering.
Motor fault
Display during motor fault
Possibilities for re-starting after the drive has cooled down terminals
“
TB/TP
”
or
“
TK/PTC
”
by:
•
By switching the mains voltage off and then on again.
•
By simultaneously depressing the three keys:
P
,
▲
,
▼
(if a fault is indicated).
•
By digital input for remote (enable ON/OFF) or by Reset-input (
F
IO Setup - Digital Inputs).
Attention!
•
Use a separate screend connection cable for temperature monitoring.
•
An outside voltage may never be connected to the terminals
“
TB/TP
”
and/or
“
TK/PTC
”
!
Operating Instruction
Econtrol
–
model series EXDM
Electrical installation
L-BAL-E008-GB 0945 Index 005
Part.-No. 00156742-GB
13/85