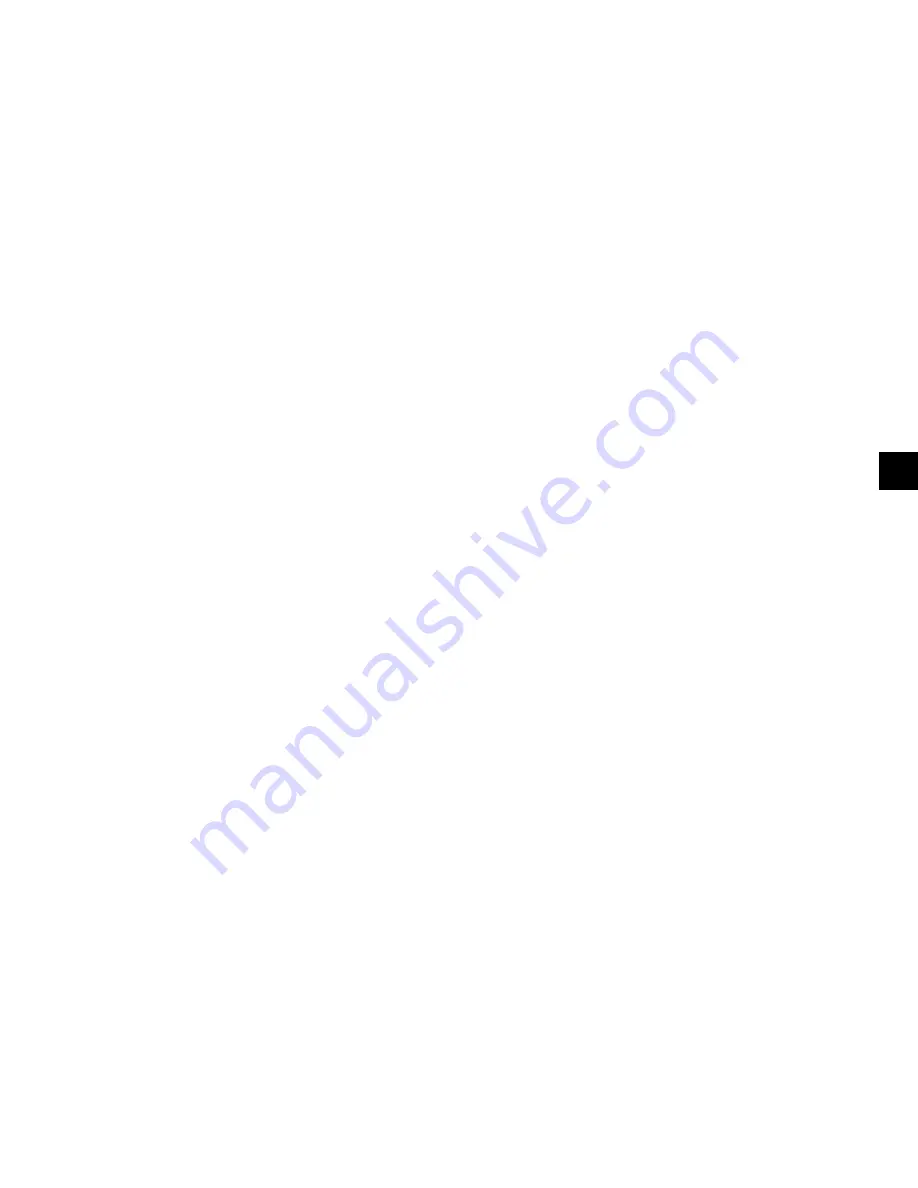
JOHNSON CONTROLS
43
SECTION 5 - COMMISSIONING
FORM 201.23-NM2
ISSUE DATE: 09/25/2020
5
Unit Switch
Place the UNIT switch on the keypad to the ON position.
Start-up
Press the SYSTEM SWITCHES key and place the
system switch for System 1 to the ON position. There
may be a few seconds delay before the first compres-
sor starts because of the anti-recycle timer). Be ready
when each compressor starts, to switch the UNIT
switch OFF immediately, if any unusual noises or other
adverse conditions develop.
When a compressor is running, the controller monitors
oil pressure, motor current, and various other system
parameters such as discharge pressure, chilled liquid
temperature, etc. Should any problems occur; the con-
trol system will immediately take appropriate action
and display the nature of the fault.
Oil Pressure
When a compressor starts, press the relevant “System
Pressures” key and verify that oil differential pressure
(oil pressure-suction pressure) develops immediately.
If oil pressure does not develop, the automatic con-
trols will shut down the compressor. Under no circum-
stances should a restart attempt be made on a compres-
sor, which does not develop oil pressure immediately.
Switch the UNIT switch to the OFF position.
Refrigerant Flow
When a compressor starts, a flow of liquid refrigerant
will be seen in the liquid line sight glass. After several
minutes of operation, and provided a full charge of re-
frigerant is in the system, the bubbles will disappear
and be replaced by a solid column of liquid.
Loading
Once the unit has been started, all operations are fully
automatic. After an initial period at minimum capacity,
the control system will adjust the unit load depending
on the chilled liquid temperature and rate of tempera-
ture change. If a high heat load is present, the control-
ler will increase the speed of the compressor(s).
Condenser and Fan Rotation
Once a compressor is running, discharge pressure rises
as refrigerant is pumped into the air-cooled condenser
coils. This pressure is controlled by stages of fans to
ensure maximum unit efficiency while maintaining
sufficient pressure for correct operation of the con-
densers and the lubrication system.
As discharge pressure rises, the condenser fans operate
in stages to control the pressure. Verify that the fans
operate in the correct direction of rotation and opera-
tion is correct for the type of unit.
Suction Superheat
Check suction superheat at steady full compressor
load only. Measure suction temperature with a thermo-
couple on the copper line about 6 in. (150 mm) before
the compressor suction service valve. Measure suction
pressure at the suction transducer access valve or the
compressor suction service valve. Superheat should
be 10°F to 12°F (5.55°C to 6.67°C) and should be
reasonably close to the panel display. Superheat set-
ting is programmable on the control panel, but is not
mechanically adjustable. The Flash Tank Drain Valve
controller modulates the 2 phase Drain Valve Stepper
Motor to control system superheat. Superheat control
is a function of suction pressure and suction tempera-
ture measurements from the sensors that are routed to
the Chiller Control Board which in turn sends control
signals to the Flash Tank Drain and Fill Valve Control-
ler located in the left, back wall of the Chiller Controls
Cabinet.
Subcooling
Check liquid subcooling at steady full compressor load
only. It is important that all fans are running for the
system. Measure liquid line temperature on the copper
line at the main liquid line service valve. Measure liq-
uid pressure at the liquid line service valve. Subcooling
should be 5°F to 7°F (2.77°C to 3.88°C). YCIV 0157
subcooling should be 10°F (5.55°C). No bubbles
should show in the sight glass. If subcooling is out of
range, add or remove refrigerant as required to clear
the sight glass. Do not overcharge the unit. Subcooling
should be checked with a flash tank level of approxi-
mately 35% with a clear sight glass.
General Operation
After completion of the above checks for System 1,
switch OFF the SYS 1 switch on the keypad and repeat
the process for each subsequent system. When all run
correctly, stop the unit, switch all applicable switches
to the ‘ON’ position and restart the unit.
Assure all checks are completed in the
Equipment Pre
Start-up and Start-up Checklist
(Pages 56 through
61)
. The chiller is then ready to be placed into opera-
tion.
Содержание YCIV Series
Страница 14: ...JOHNSON CONTROLS 14 FORM 201 23 NM2 ISSUE DATE 09 25 2020 THIS PAGE INTENTIONALLY LEFT BLANK...
Страница 32: ...JOHNSON CONTROLS 32 FORM 201 23 NM2 ISSUE DATE 09 25 2020 THIS PAGE INTENTIONALLY LEFT BLANK...
Страница 40: ...JOHNSON CONTROLS 40 FORM 201 23 NM2 ISSUE DATE 09 25 2020 THIS PAGE INTENTIONALLY LEFT BLANK...
Страница 50: ...JOHNSON CONTROLS 50 FORM 201 23 NM2 ISSUE DATE 09 25 2020 THIS PAGE INTENTIONALLY LEFT BLANK...
Страница 105: ...JOHNSON CONTROLS 105 SECTION 6 TECHNICAL DATA FORM 201 23 NM2 ISSUE DATE 09 25 2020 THIS PAGE INTENTIONALLY LEFT BLANK...
Страница 325: ...JOHNSON CONTROLS 325 FORM 201 23 NM2 ISSUE DATE 09 25 2020 NOTES...