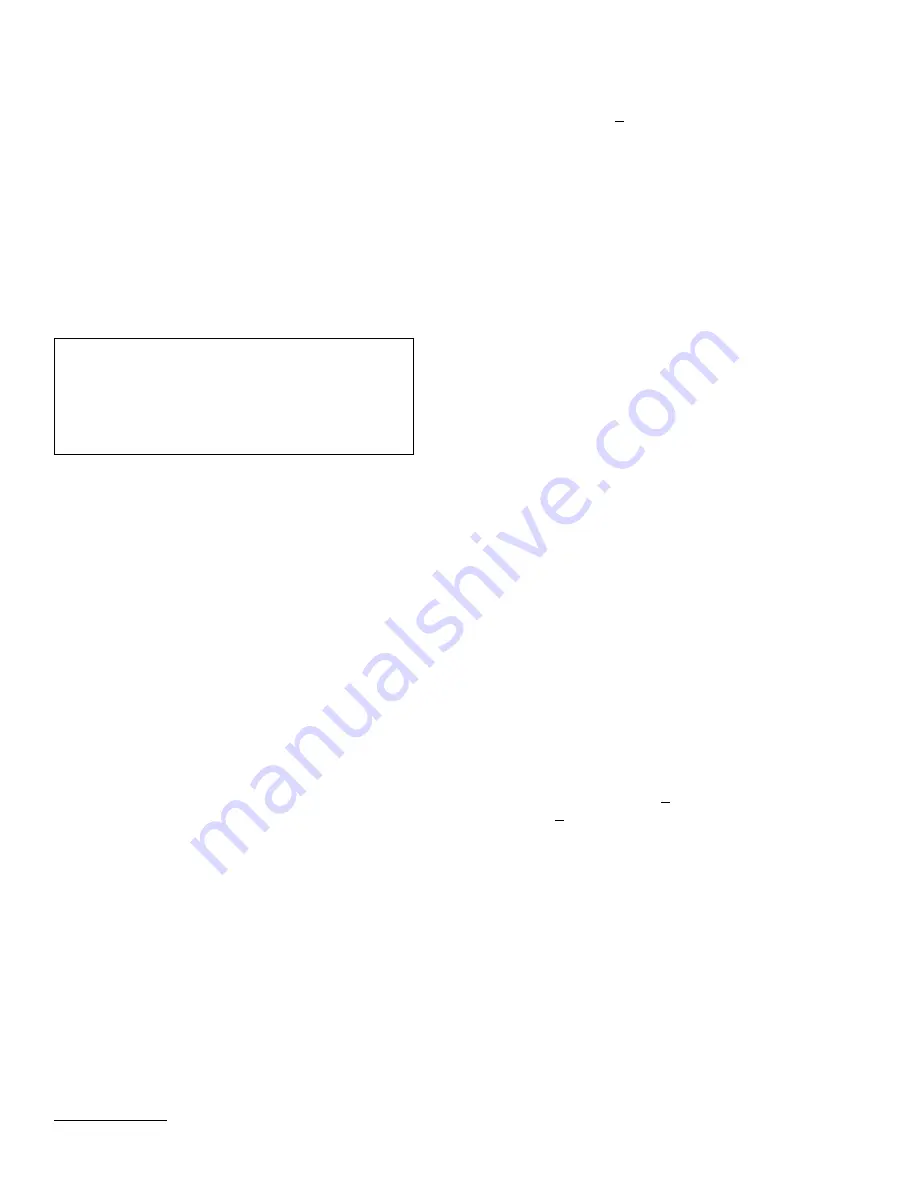
YORK INTERNATIONAL
26
SYSTEM START-UP AND OPERATION
Checking the System 24 Hours Prior to Initial Start-
Up (No Power)
1. UNIT CHECKS
A. Inspect the unit for shipping or installation damage.
B. Assure that all piping has been completed and
flushed.
C. Check that the unit is properly charged and that
there are no piping leaks.
D. Suction and discharge stop valves and the refrig-
erant liquid stop valves are open (ccw).
CAUTION
Compressor lubrication circuit must be primed with
YORK “C” oil prior to start-up. Priming should be
done through the Schrader fitting at the compres-
sor oil pump. Stroke oil pump 10 times to prime the
lubrication circuit.
E. “Full” oil quantity is shown by an oil level showing
in the upper sight glass. “Low” oil quantity is shown
by an oil level showing in the lower sight glass. If it
is necessary to add oil, connect a YORK oil pump
to the oil charging valve, but do not tighten the
flare nut on the delivery tubing. With the bottom
(suction end) of the pump submerged in oil to avoid
the entrance of air, operate the pump until oil drips
from the flare nut joint, allowing the air to be ex-
pelled, and tighten the flare nut. Open the com-
pressor oil charging valve and pump in oil until oil
reaches the proper level as described above.
Close the compressor oil charging valve.
F. Assure water pumps are on. Check and adjust
water pump flow rate and pressure drop across
cooler. Verify flow switch operation.
G. Check panel to see that it is free of foreign mate-
rial (wires, metal chips, etc.).
H. Visually inspect wiring (power & control). Must
meet NEC and all local codes.*, **
I. Check for proper size fuses in main and control
power circuits.
J. Verify that field wiring matches the 3-phase power
requirements of the compressor. See nameplate.**
K. Assure 115VAC Control Power to TB1 has 30A
minimum capacity.*
L. Be certain all control bulbs are inserted completely
in their respective wells and are coated with heat
conductive compound.
2. PANEL CHECKS (Power On, System Switch “Off”)
A. Apply 3 phase power and verify its value.**
B. Apply 115VAC and verify its value on the terminal
block in the lower right of the Logic Panel. Make
the measurement between terminals 41 and 2.
Should be 10%.*
C. Assure crankcase heaters are on. Allow crank-
case heaters to remain on a minimum of 24 hours
before startup. This is important to assure no re-
frigerant is in the oil at start-up!
D.
Checking The Electronics
A few simple checks will assure that the panel
electronics are working and that the system will
run when you come back in 24 hrs. for start-up.
Checking the Microprocessor Board and its Par-
allel Interface
Display the Return Water Temp. Setpoint and
verify that it matches the Return Water Temp.
Setpoint Switches.
Checking the Analog Input Board and the Micro-
processor Board’s A/D Converter
Display the Low Suction Pressure Cutout, Low Wa-
ter Temp. Cutout, and Low Ambient Cutout. These
displays should match the printout placed inside
the unit. The printout will provide the unit specs. on
the cutouts as ordered by the customer. Deviation
from these could be due to a defective board or
tampering with the Analog Input Board pots.
Checking the R.P. Relay
Remove the wire on terminal 3 & 4 of the terminal
block in the lower right corner Logic Panel. Note:
Water flow should be present and any remote cy-
cling devices jumpered. By removing the wire, we
simulate an open flow switch or cycling device. Con-
sequently an “A” code should appear on the display.
Checking the Power Supply Board
If the other boards check out alright, there is al-
most a100% chance that the Power Supply Board
is functioning properly. If any board malfunctions,
check its supply voltages. UNREG voltages nor-
mally measure 40% high + 10%. REG voltages
should be +.1V.
E. By performing the previous checks, we will assure
most of the system is functioning properly. Ther-
mistors and transducers can be checked at this point.
The display can be checked against a gauge if de-
sired. To assure proper return and leaving water
temp. displays, flow must be present. We won’t be
worrying about checking out the Relay Output Board.
This board is easy to diagnose and can easily be
field repaired with factory assistance if the need
arises.
INITIAL START-UP
After the operator has read the proceeding pages, has
become familiar with the control panel and its functions,
and has performed the proceeding unit checks and
panel checks, the unit can be put into operation. Pro-
ceed by setting the switches as follows:
(YCHA100)
*See Fig. 7.
**See Fig. 8.
Содержание YCAQ10
Страница 20: ...YORK INTERNATIONAL 20 LD01779 YCHA100 FIG 9 WIRING DIAGRAM YCHA100...
Страница 21: ...FORM 150 40 NM20 21 YORK INTERNATIONAL YCHA100 LD01779 D...
Страница 22: ...YORK INTERNATIONAL 22 LD01780 L YCHA100 FIG 9 Continued...
Страница 23: ...FORM 150 40 NM20 23 YORK INTERNATIONAL LD01780 R YCHA100...
Страница 24: ...YORK INTERNATIONAL 24 YCHA100 LD01781 FIG 9 Continued...
Страница 25: ...FORM 150 40 NM20 25 YORK INTERNATIONAL LD01782 YCHA100...
Страница 46: ...YORK INTERNATIONAL 46 LD01787...
Страница 47: ...FORM 150 40 NM20 47 YORK INTERNATIONAL LD01788...
Страница 48: ...YORK INTERNATIONAL 48 LD01789...
Страница 49: ...FORM 150 40 NM20 49 YORK INTERNATIONAL LD01790...
Страница 50: ...YORK INTERNATIONAL 50 LD01791...
Страница 51: ...FORM 150 40 NM20 51 YORK INTERNATIONAL LD01792...
Страница 77: ......
Страница 78: ......
Страница 79: ......
Страница 80: ......
Страница 81: ......
Страница 82: ......
Страница 83: ......
Страница 84: ......
Страница 85: ......
Страница 86: ......
Страница 87: ......
Страница 88: ......
Страница 89: ......
Страница 90: ......
Страница 91: ......
Страница 92: ......
Страница 93: ......
Страница 94: ......
Страница 95: ......
Страница 96: ......
Страница 97: ......
Страница 98: ......
Страница 99: ......