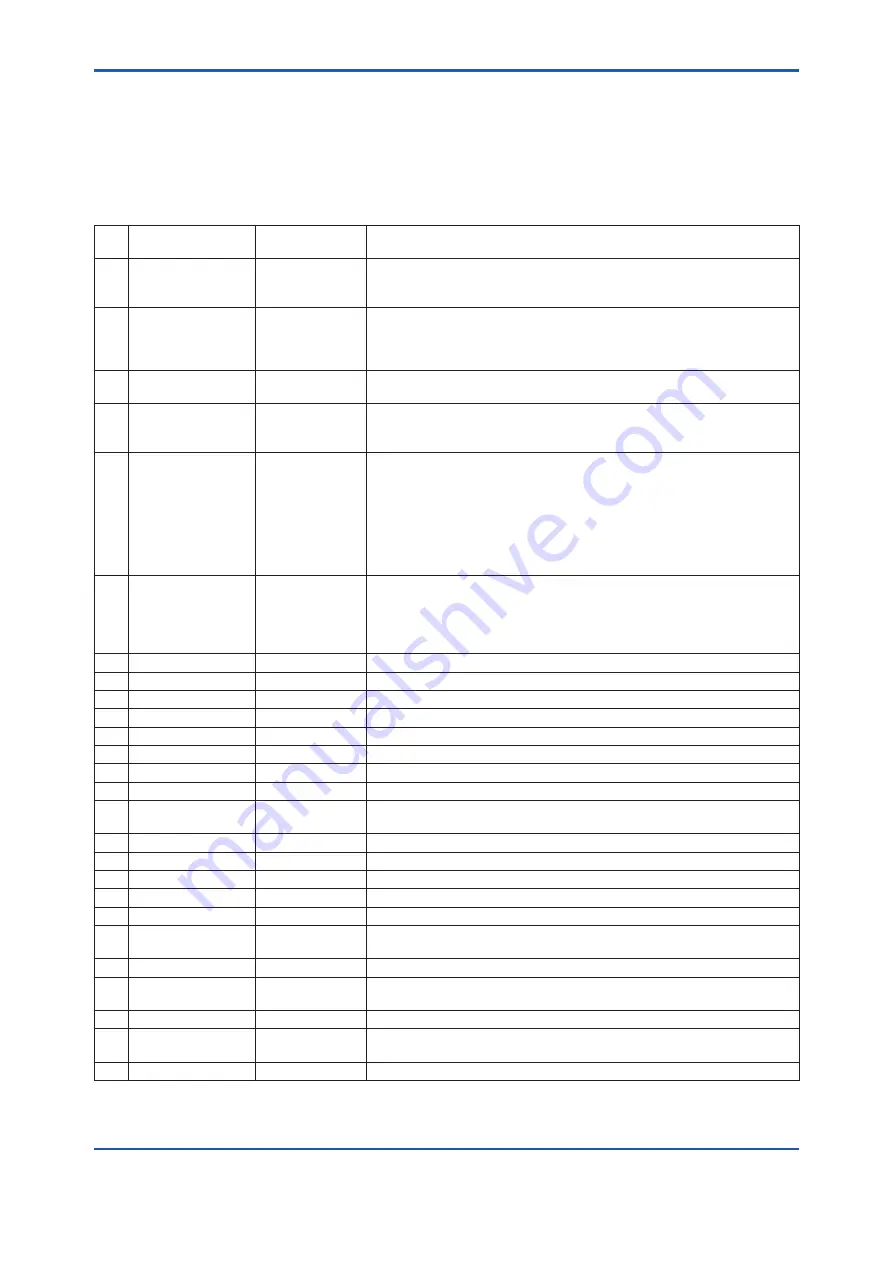
<7. HART Communication>
7-45
IM 01C25W05-01EN
7.3.2.2.11 Resetting the Reference Value
If the flow rate is changed greatly or if the fluid is changed during plant operation, acquire the reference value
again. If the flow rate changes by 25% or more relative to the flow rate that was present when the reference
value was acquired, acquire the reference value again.
When resetting the reference value, perform impulse line block purging as much as possible.
7.3.2.2.12 ILBD Parameter List
#
Parameter name
Factory default
value
Description
1
Diag Error
0x0000
The results detected by ILBD or heat trace monitoring are stored in this
parameter. Also the condition abnormality in the diagnostic process is
stored as an error.
2
Diag Option
0x08f8
Use this parameter to select the error messages and status to reflect in
the LCD and output signals. The errors assigned to each bit correspond to
the bits of Diag Error.
This parameter is selectable only when Diag Mode is set to Stop.
3
Diag Out Option
Off
Error status can be output with the 4 to 20 mA analog signal.
The available three output modes are Off, Burnout, and Fall back.
4
Diag Fixed Out Val
21.6 mA
A parameter for the fall back function in Diag Out option.
This specifies the output value of the 4 to 20 mA analog signal when
alarms occur. The value can be entered in the range of 3.8 to 21.6 mA.
5
Diag Mode
Stop
This parameter sets the ILBD operation mode.
Stop: Blockage detection is stopped.
Calculation: Block detection is executed.
Alarms are generated on the basis of detection results.
Reference: The reference values are set to the latest blockage detection
data.
When the reference values are updated, the mode automatically switches
to Calculation.
6
Diag Period
180 (sec)
This parameter sets the data sampling period for ILBD in the range of 20
to 65535 seconds.
If the process fluctuation values are unstable, increasing the sampling
period may improve the diagnostic accuracy.
This parameter can be entered only when Diag Mode is set to Stop.
7
Diag Supp Count
3
Detection count to generate an alarm.
8
Diag Description
Memo field. Up to 32 alphanumeric characters can be entered.
9
fDP
Average value of the sum of squares of differential pressure fluctuation.
10
fDP Status
Status of fDP
11
fP2
Average value of the sum of squares of module 2 side fluctuation.
12
fP2 Status
Status of fP2
13
fP1
Average value of the sum of squares of module 1 side fluctuation.
14
fP1 Status
Status of fP1
15
BlkF
The blockage level obtained by comparing the pressure fluctuation
between the module 1 side and module 2 side.
16
BlkF Status
Status of BlkF
17
DPAvg
Ratio of the average of differential pressure to the maximum span
18
DPAvg Status
Status of DPAvg
19
Ratio fDP
Differential pressure RMS compare value
20
Ratio fDP Status
Status of Ratio fDP
21
Ratio fP2
Module 2 side pressure RMS compare value
This is used to detect blockage in the module 2 side impulse line.
22
Ratio fP2 Status
Status of Ratio fP2
23
Ratio fP1
Module 1 side pressure RMS compare value
This is used to detect blockage in the module 1 side impulse line.
24
Ratio fP1 Status
Status of Ratio fP1
25
Ref fDP
Value of fDP obtained under steady state operation used as a reference
for blockage detection.
26
Ref fDP Status
Status of Ref fDP
Содержание DPharp EJXC40A
Страница 1: ...User s Manual Digital Remote Sensor IM 01C25W05 01EN IM 01C25W05 01EN 4th Edition...
Страница 16: ...2 Handling Cautions 2 6 IM 01C25W05 01EN Note 6 Control Drawing...
Страница 17: ...2 Handling Cautions 2 7 IM 01C25W05 01EN...
Страница 18: ...2 Handling Cautions 2 8 IM 01C25W05 01EN...