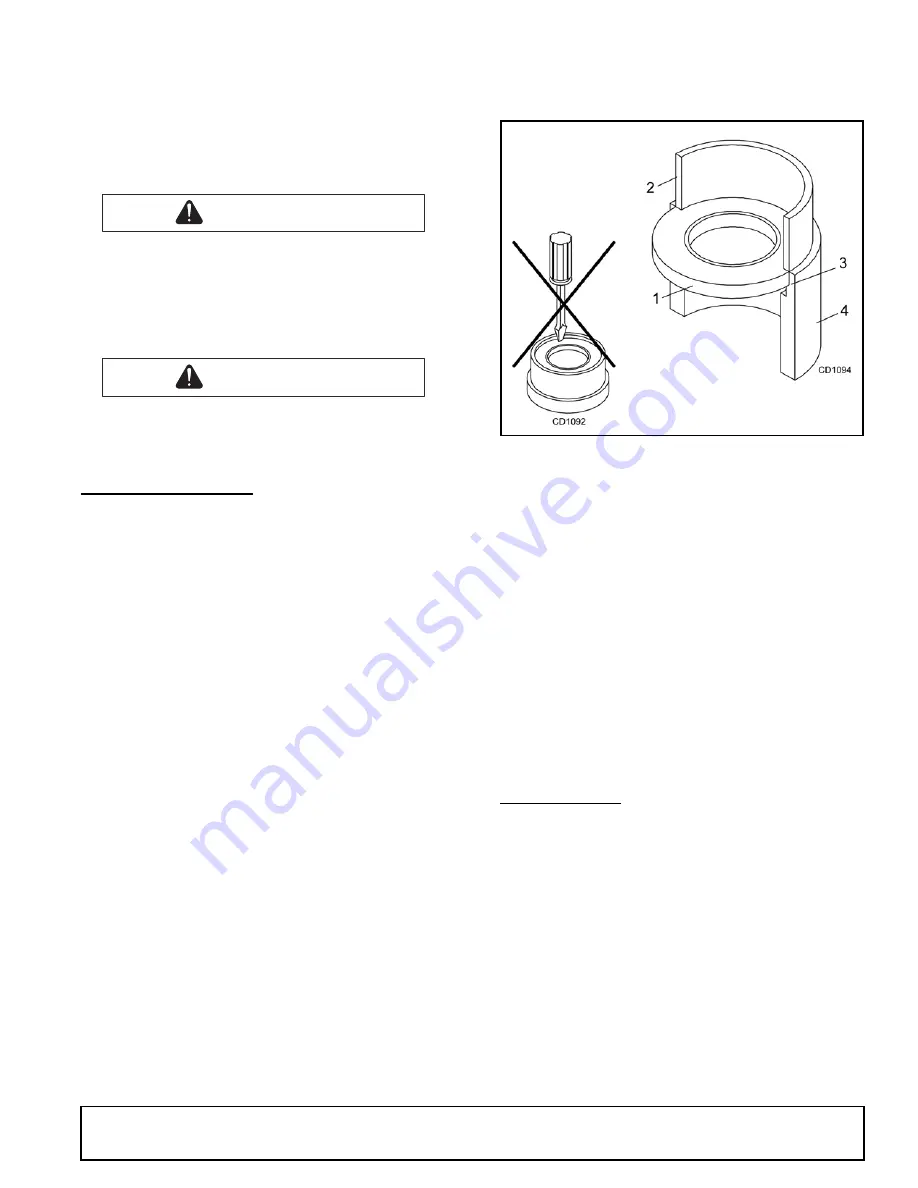
Dealer Service
21
MAN1279 (15/04/2019)
DEALER SERVICE
The information in this section is written for dealer service personnel. The
repair described here requires special skills and tools. If your shop is not prop-
erly equipped or your mechanics are not properly trained in this type of repair,
you may be time and money ahead to replace complete assemblies.
■
Before working underneath, read manual instructions, securely
block up, and check stability. Secure blocking prevents equipment from
dropping due to hydraulic leak down, hydraulic system failure, or
mechanical component failure.
■
Keep all persons away from operator control area while performing
adjustments, service, or maintenance.
■
Always wear relatively tight and belted clothing to avoid getting
caught in moving parts. Wear sturdy, rough-soled work shoes and protec-
tive equipment for eyes, hair, hands, hearing, and head; and respirator or
filter mask where appropriate.
GEARBOX MAINTENANCE
NOTE:
Read this entire section before starting any repair. Many steps
are dependent on each other.
1.
Fill gearbox with SAE 80W or 90W gear lube. Proper oil level is between
lowest ring and end of dipstick.
NOTE:
Repair to this gearbox is limited to replacing bearings, seals, and
gaskets. Replacing gears, shafts, and a housing is not cost effective. Pur-
chasing a complete gearbox is more economical.
2.
Inspect gearbox for leakage and bad bearings. Leakage is a very serious
problem and must be corrected immediately.
NOTE:
Bearing failure is indicated by excessive noise and side-to-side or
end-play in gear shafts.
Seal Replacement (Figure 12)
Recommended sealant for gearbox repair is Permatex
®
Aviation 3D Form-A-
Gasket or equivalent.
Leakage can occur at the vertical or horizontal gaskets and shaft seals.
Leakage at the horizontal gasket or seal can be repaired without removing the
gearbox from the cutter.
Seal Installation
NOTE:
Proper seal installation is important. An improperly installed seal will
leak.
1.
Clean area in housing where seal outer diameter (OD) seats. Apply a thin
coat of Permatex.
2.
Inspect area of shaft where seal seats. Remove any burrs or nicks with
an emery cloth.
3.
Lubricate gear shaft and seal lips.
4.
Place seal squarely on housing, spring-loaded lip toward housing. Select
a piece of pipe or tubing with an OD that will sit on the outside edge of the
seal but will clear the housing. Tubing with an OD that is too small will
bow seal cage and ruin seal.
5.
Carefully press seal into housing, avoiding distortion to the metal seal
cage.
Figure 12
. Seal Installation
Vertical Shaft Seal Replacement (Figure 13)
1.
Disconnect and remove the rear driveline from the gearbox.
2.
Remove vent plug (24) and siphon gear lube from housing through this
opening.
3.
Remove crossbar (see page 24).
4.
Remove protective seal (8) and vertical shaft seal (18). Replace seal (18)
with new seal.
Vertical seal should be recessed in housing. Horizontal seal (19) should
be pressed flush with outside of housing.
NOTE:
Distortion to seal cage or damage to seal lip will cause seal to
leak.
5.
Fill gearbox with SAE 80W or 90W gear lube until it runs out the level
plug.
6.
Remove and replace any seal damaged in installation.
Horizontal Shaft Seal Replacement (Figure 13)
1.
Disconnect and remove the rear driveline from the gearbox.
2.
Remove vent plug (24) and siphon gear lube from housing through this
opening.
3.
If the leak occurred at either end of horizontal shaft, remove oil cap (20)
and/or oil seal (19). Replace with new one.
4.
Fill gearbox with SAE 80W or 90W gear lube until it runs out the level
plug.
GEARBOX REPAIR
Removal from Cutter (Figure 13)
NOTE:
Gearbox is heavy: do not attempt to move without mechanical assis-
tance.
1.
Disconnect and remove the rear driveline from the gearbox.
2.
Remove cotter pin and nut from vertical shaft and remove crossbar (see
page 24).
3.
Remove the six bolts that attach gearbox to cutter and remove gearbox.
Disassembly (Figure 13)
1.
Remove top cover (22) from gearbox and pour out gear oil.
2.
Remove oil cap (20) (to be replaced).
3.
Remove snap ring (10) and shim (13) from input shaft (3).
4.
Support gearbox in hand press and push on input shaft (3) to remove
bearing (7).
5.
Remove six cap screws (23) and top cover (22) from housing. Remove
gear (1) from inside housing.
6.
Remove oil seal (19) from front of housing (to be replaced).
7.
Remove snap ring (10) and shim (13) from front of housing (2).
8.
Remove input bearing (7) by using a punch and hammer from outside of
housing.
WARNING
WARNING
CAUTION
CAUTION
1.
Seal
2.
Pipe or tube
3.
Seal seat
4.
Casting
Pipe or tube must
press at outer
edge of seal.
Incorrect
Installation
Содержание BATWING BW20.50QE
Страница 1: ...OPERATOR S MANUAL BATWING ROTARY CUTTER Rev 22 10 2019 BW20 50QE BW20 60QE BW20 70QE MAN1279...
Страница 10: ...10 Declaration of Conformity MAN1279 15 04 2019...
Страница 45: ...Common Components 45 MAN1279 15 04 2019 NOTES...
Страница 46: ...46 50 Series Parts MAN1279 15 04 2019 CENTER FRAME ASSEMBLY BW20 50QE...
Страница 50: ...50 50 Series Parts MAN1279 15 04 2019 WING CENTER GEARBOX ASSEMBLY BW20 50QE...
Страница 55: ...50 Series Parts 55 MAN1279 15 04 2019 NOTES...
Страница 56: ...56 60 Series Parts MAN1279 15 04 2019 CENTER FRAME ASSEMBLY BW20 60QE...
Страница 60: ...60 60 Series Parts MAN1279 15 04 2019 WING CENTER GEARBOX ASSEMBLY BW20 60QE...
Страница 66: ...66 70 Series Parts MAN1279 15 04 2019 CENTER FRAME ASSEMBLY BW20 70QE...
Страница 70: ...70 70 Series Parts MAN1279 15 04 2019 WING CENTER GEARBOX ASSEMBLY BW20 70QE...
Страница 81: ...MANUEL DE L UTILISATEUR BATWING FAUCHEUSE ROTATIVE R v 15 04 2019 BW20 50QE BW20 60QE BW20 70QE MAN1279...
Страница 90: ...10 Declaration of Conformity MAN1279 15 04 2019 10 D claration de conformit MAN1279 15 04 2019...