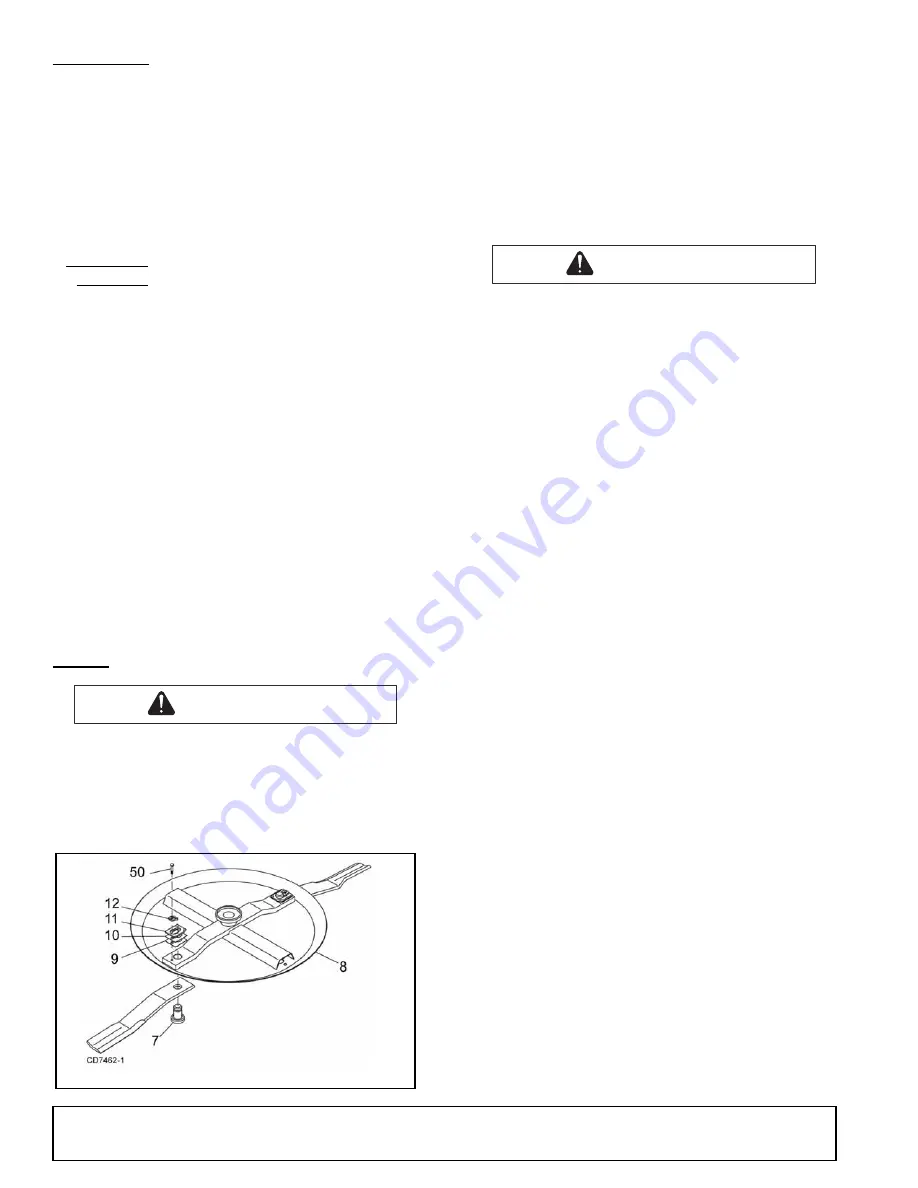
16
Owner Service
MAN1279 (15/04/2019)
LUBRICATION
Do not let excess grease collect on or around parts, particularly when operating
in sandy areas.
See Figure 6 for lubrication points and frequency or lubrication based on nor-
mal operating conditions. Severe or unusual conditions may require more fre-
quent lubrication.
Use a lithium grease of #2 consistency with a MOLY (molybdenum disulfide)
additive for all locations unless otherwise noted. Be sure to clean fittings thor-
oughly before attaching grease gun. One good pump of most guns is sufficient
when the lubrication schedule is followed.
Gearbox Lubrication
For gearbox, use a high quality gear oil with a viscosity index of 80W or 90W
and an API service rating of GL–4 or –5 in gearboxes.
Check gearbox daily for evidence of leakage, and contact your dealer if leak-
age occurs. Use sealant on vent plug threads during installation. Check vent
plug periodically and clean if it does not relieve pressure.
Driveline Lubrication
1.
Lubricate the driveline slip joint every eight operating hours. Failure to
maintain proper lubrication could result in damage to U-joints, gearbox,
and driveline.
2.
Lower cutter to ground, disconnect driveline from tractor PTO shaft, and
slide halves apart but do not disconnect from each other.
3.
Apply a bead of grease completely around male half where it meets
female half. Slide drive halves over each other several times to distribute
grease.
Seasonal Lubrication
In addition to the daily recommended lubrication, a more extensive application
is recommended seasonally.
1.
Fill CV double yokes with 20 pumps of grease with the joints in a straight
line.
2.
Articulate CV body to maximum angle several times to ensure full
coverage of joints.
3.
Place joints in the straight position and add 10 additional pumps of
grease to both joints.
4.
Wipe telescoping drive clean of all old grease and contaminants.
5.
Add a thin layer of new grease over telescoping drive.
BLADES
■
Before working underneath, read manual instructions, securely
block up, and check stability. Secure blocking prevents equipment from
dropping due to hydraulic leak down, hydraulic system failure, or
mechanical component failure.
■
Your dealer can supply genuine replacement blades. Substitute
blades may not meet original equipment specifications and may be dan-
gerous.
Blade Removal (Figure 7)
Figure 7
. Blade Assembly
1.
Disconnect driveline from tractor PTO.
2.
Raise cutter and block securely (see Figure 6).
3.
Align crossbar (8) with blade access hole in the cutter frame. Remove
cap screw (50), blade pin lock clip (12, keyhole plate (11), and shims (9 &
10). Carefully drive blade pin (7) out of crossbar.
4.
Rotate crossbar and repeat for opposite blade.
NOTICE
■
If blade pin (7) is seized in crossbar and extreme force will be
needed to remove it, support crossbar from below to prevent gearbox
damage.
Blade Installation (Figure 7)
NOTICE
■
Crossbar rotation has clockwise rotation on left gearbox and anti-
clockwise rotation on the right and centre gearboxes when looking down
on cutter. Be sure to install blade cutting edge to lead in correct rotation.
■
Service and maintenance work not covered in OWNER SERVICE
must be done by a qualified dealership. Special skills, tools, and safety
procedures may be required. Failure to follow these instructions can
result in serious injury or death.
■
Before servicing, adjusting, repairing or unplugging, stop tractor
engine, place all controls in neutral, set park brake, remove ignition key,
and wait for all moving parts to stop.
■
Never perform service or maintenance with engine running.
■
Keep all persons away from operator control area while performing
adjustments, service, or maintenance.
■
Before working underneath, disconnect driveline from tractor, lower
wings to ground, raise cutter, and pin transport bar in raised position.
Attach parking jack and lower to ground. Securely block all four corners
of centre section and each wing with jack stands. Blocking up prevents
the cutter from dropping due to hydraulic leak down, hydraulic system
failure, or mechanical component failure.
■
If you do not understand any part of this manual and need assis-
tance, see your dealer.
■
Always wear relatively tight and belted clothing to avoid entangle-
ment in moving parts. Wear sturdy, rough-soled work shoes and protec-
tive equipment for eyes, hair, hands, hearing, and head. Wear a respirator
or filter mask where appropriate.
NOTE:
Always replace or sharpen both blades at the same time.
1.
Inspect blade pin (7) for nicks or gouges, and if you find any, replace the
blade pin.
2.
Insert blade pin through the blade. Blade should swivel on blade pin; if it
doesn’t, determine the cause and correct.
3.
Align crossbar (8) with blade access hole in cutter frame. Apply a liberal
coating of Never-Seez
®
or equivalent to blade pin and crossbar hole.
Make sure blade offset is down away from cutter.
4.
Insert blade pin (7) through blade. Push blade pin through crossbar.
5.
Install shims (9 & 10) over blade pin.
NOTE:
Only use enough shims to allow keyhole plate (11) to slide into
blade pin groove.
6.
Install blade clip (12) over keyhole plate and into blade pin groove.
7.
Secure into position with cap screw (50). Torque cap screw to 115 Nm
(85 lbs-ft).
8.
Repeat steps for opposite side.
NOTE:
Blade should be snug but should swivel on pin without having to
exert excessive force. Blade should not move more than a 1/4 inch up or
down at the tip. Keep any spacers not used in the installation as replace-
ments or for future installation.
Blade Sharpening
NOTICE
■
When sharpening blades, grind the same amount on each blade to
maintain balance. Replace blades in pairs. Unbalanced blades will cause
excessive vibration, which can damage gearbox bearings. Vibration may
also cause structural cracks to cutter.
1.
Sharpen both blades at the same time to maintain balance. Follow
original sharpening pattern.
2.
Do not sharpen blade to a razor edge—leave at least a 1.6 mm (1/16 in.)
blunt edge.
3.
Do not sharpen back side of blade.
Splitter Gearbox
Fill gearbox until oil runs out the side plug on gearbox.
Wing Gearbox
Fill gearbox until oil is just above lower line on dipstick.
WARNING
WARNING
7.
Blade pin
8.
Crossbar assembly
9.
Shim, 18 GA
10.
Shim, 20 GA
11.
Keyhole plate
12.
Blade lock clip
50.
1/2 NC x 1-1/4 HHCS GR5
CAUTION
CAUTION
Содержание BATWING BW20.50QE
Страница 1: ...OPERATOR S MANUAL BATWING ROTARY CUTTER Rev 22 10 2019 BW20 50QE BW20 60QE BW20 70QE MAN1279...
Страница 10: ...10 Declaration of Conformity MAN1279 15 04 2019...
Страница 45: ...Common Components 45 MAN1279 15 04 2019 NOTES...
Страница 46: ...46 50 Series Parts MAN1279 15 04 2019 CENTER FRAME ASSEMBLY BW20 50QE...
Страница 50: ...50 50 Series Parts MAN1279 15 04 2019 WING CENTER GEARBOX ASSEMBLY BW20 50QE...
Страница 55: ...50 Series Parts 55 MAN1279 15 04 2019 NOTES...
Страница 56: ...56 60 Series Parts MAN1279 15 04 2019 CENTER FRAME ASSEMBLY BW20 60QE...
Страница 60: ...60 60 Series Parts MAN1279 15 04 2019 WING CENTER GEARBOX ASSEMBLY BW20 60QE...
Страница 66: ...66 70 Series Parts MAN1279 15 04 2019 CENTER FRAME ASSEMBLY BW20 70QE...
Страница 70: ...70 70 Series Parts MAN1279 15 04 2019 WING CENTER GEARBOX ASSEMBLY BW20 70QE...
Страница 81: ...MANUEL DE L UTILISATEUR BATWING FAUCHEUSE ROTATIVE R v 15 04 2019 BW20 50QE BW20 60QE BW20 70QE MAN1279...
Страница 90: ...10 Declaration of Conformity MAN1279 15 04 2019 10 D claration de conformit MAN1279 15 04 2019...