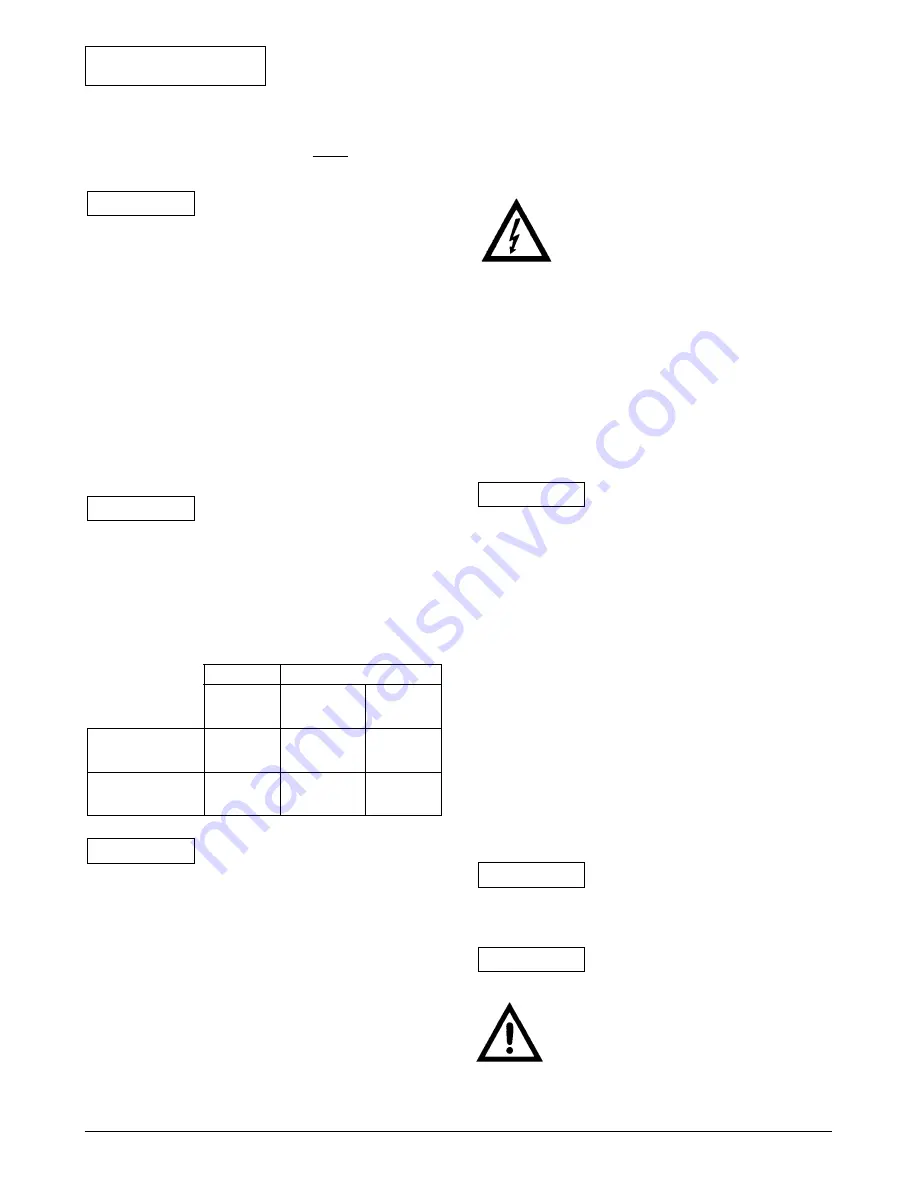
ENGLISH
42
2.
The enclosed plain washers
must
be used bet-
ween the screw/nut head and the combi flange
(fig. 3, pos. 1).
Safety elements (e.g spring rings) are
not permitted.If the pump is not cor-
rectly installed the nut can get in
caught the slot. As a result, due to in-
sufficient screw pretensioning, the
performance of the flanged connec-
tion can be affected.
3.
It is recommended that screws with a strength
class of 4.6 are used for flanged connections.
When using screws made from a material other
than 4.6 (e.g. screws made from material 5.6 or
an even higher-performance material), only the
permissible screw tightening torque correspon-
ding to material 4.6 is to be used during installa-
tion.
Permissible screw tightening torques:
for M 12
f
40 Nm,
for M 16
f
95 Nm
If higher-performance screws (
≥
4.6)
are tightened to tightening torques
other than those permitted, splinte-
ring may occur around the edges of
the slots due to the higher screw
tensions. This will cause the screws
to lose their pretensioning and the
flanged connection could leak.
4.
Sufficiently long screws are to be used:
ATTENTION!
ATTENTION!
x
Loosen 2 M5 hexagon socket screws (SW4) (pos. 4),
x
Remove control module from motor (pos. 5),
x
To install, reverse the above sequence.
If the pump is running off a generator (ro-
tor driven by admission pressure pump), a
dangerous voltage is created at the motor
terminals after the control module is re-
moved. The motor terminals are designed
as VDE-approved bushings, so that there
is no danger if simply touched with the
finger. However, there would be a danger
if a pointed object (nail, screwdriver, wire)
were poked into one of the bushings.
For easy installation there are 2 or 3 (depending on
pump type) pilot pins on the back of the control mo-
dule which snap into corresponding holes in the motor
housing. Only when these pilot pins have secured the
control module to the motor housing does the central
earthing pin and then the winding pins make contact
(fig. 4).
Between the motor housing and the
control module there is a flat seal (fig.
4, pos. 6) which is responsible for the
thermal decoupling of the two com-
ponents. This seal must always be
placed between the module and the
motor when installing the control
module.
5.1.2 Removing/installing the motor impeller
unit
To remove the motor, 4 M6 hexagon socket screws
(SW5) must be loosened. These screws can be reached
with the following tools (fig. 5, pos. 2):
x
90° offset socket-head screwdriver
x
spherical head socket-head screwdriver
x
[
” reversing ratchet with suitable bit
If only the control module is to be moved into a diffe-
rent position, the motor does not need to be comple-
tely removed from the pump housing. The motor can
be turned to the desired position in the pump housing,
provided there is sufficient room available.
Be careful not to damage the O-ring
situated between the motor head
and the pump housing. The O-ring
must lie untwisted in the bevel of the
end shield pointing to the impeller.
The shaft is inextricably linked to the
impeller, the end shield and the rotor.
This unit is secured against uninten-
tional removal from the motor. If the
rotor with its strong magnets is not in
the motor housing, it has a consider-
able potential for danger e.g. by sud-
denly attracting objects made from
iron/steel, influencing electrical
equipment (risk to people with pace-
ATTENTION!
ATTENTION!
ATTENTION!
Treading
min. screw length
DN 32 /
DN 50 /
DN 40
DN 65
Flanged
end PN6
M12
55 mm
60 mm
Flanged
end PN10
M16
60 mm
65 mm
When fitting bolting flanges, make
sure the screws are of sufficient
length. The screw thread must pro-
trude from the nut by at least one
turn (fig. 3, pos. 2).
x
Place the two shells of the lagging in position and
press together so that the pilot pins snap into their
appropriate opposite holes.
5.1.1 Removing/installing the control module
The control module can be separated from the motor
by loosening 2 screws (fig. 4):
x
Loosen terminal box lid screws (pos. 1),
x
Remove terminal box lid (pos. 2),
x
Remove sealing stopper using a suitable tool, avoid
damaging the stopper (pos.3),
ATTENTION!
Содержание Wilo-Stratos -Z
Страница 2: ...Fig 1a Fig 1b Fig 2a Fig 3 Fig 2b...
Страница 3: ...Fig 5 Fig 4 Fig 6 Fig 7...
Страница 4: ...Fig 8 Fig 9 Fig 11 Fig 10 Fig 12...
Страница 6: ...Fig 15 Fig 15 LON Fig 15 PLR Fig 15 SBM Fig 15 Ext Min Fig 15 Ext Off...
Страница 14: ...DEUTSCH 8 Displaylage horizontal vertikal Lageeinstellung in Men punkt 3...
Страница 41: ...ENGLISH 35 Display position horizontal vertical Position setting in menu point 3...
Страница 95: ...NEDERLANDS 89 Display richting horizontaal vertikaal Instelling van de richting in menu punt 3...
Страница 118: ......