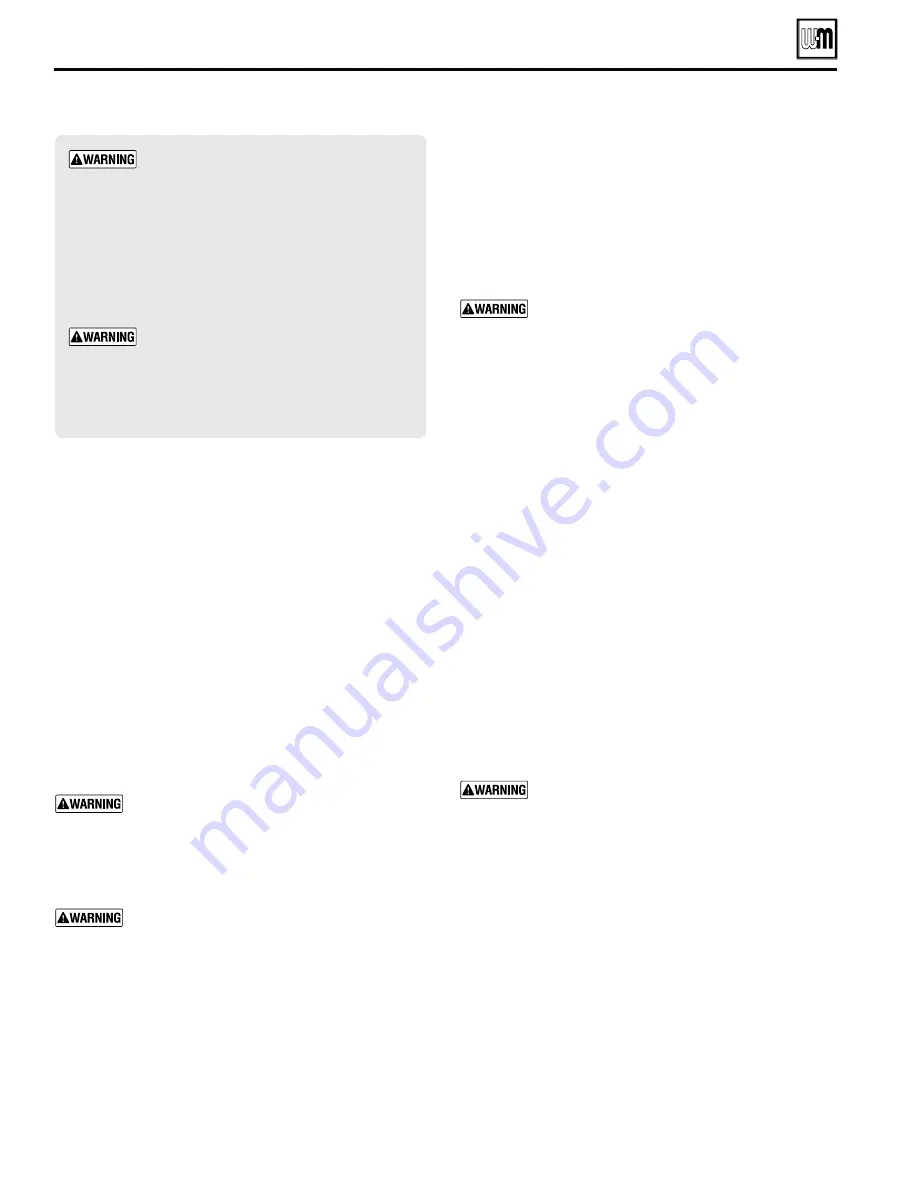
Part number 550-100-168/0516
92
SlimFit
®
Series 3
COMMERCIAL
CONDENSING
GAS
-
FIRED
WATER
BOILER
—
Boiler Manual
The boiler should be inspected and started
annually, at the beginning of the heating
season, only by a qualified service technician.
In addition, the maintenance and care of the
boiler designated in Figure 77, page 90 and
explained on the following pages must be
performed to assure maximum boiler ef-
ficiency and reliability. Failure to service and
maintain the boiler and system could result
in equipment failure.
Electrical shock hazard — Turn off power
to the boiler before any service operation on
the boiler except as noted otherwise in this
instruction manual. Failure to turn off elec-
trical power could result in electrical shock,
causing severe personal injury or death.
Address reported problems
1. Inspect any problems reported by owner and correct before
proceeding.
Inspect boiler area
1. Verify that boiler area is free of any combustible materials,
gasoline and other flammable vapors and liquids.
2. Verify that air intake area is free of any of the contaminants
listed on page 22 of this manual. If any of these are present
in the boiler intake air vicinity, they must be removed. If they
cannot be removed, reinstall the air and vent lines per this
manual and the SlimFit Boiler Vent Supplement.
Inspect boiler interior & door gaskets
1. Remove front door and inspect interior of boiler.
2. Visually inspect the door gaskets. Make sure all are in good
condition. Obtain replacements if any gasket is damaged.
Door gaskets must be intact, and must provide a
reliable seal. Replace any damaged gasket.
3. Remove the venturi air inlet silencer and clean if necessary.
Replace silencer.
4. Vacuum any sediment from the inside of the boiler and
components. Remove any obstructions.
Do not use solvents to clean any of the boiler
components. The components could be damaged,
resulting in unreliable or unsafe operation.
Clean condensate trap
1. Remove flue inspection plug (item 45, page 3).
2. Inspect base collector with flash light. Flush out with water
as needed.
3. Loosen condensate trap line hose clamps and remove trap
line.
4. Empty water from trap line and inspect. Flush out if needed
with fresh water.
5. Check condensate fittings and condensate line to drain. Flush
if necessary to clean.
6. Reinstall condensate trap line and tighten hose clamps.
7. Fill trap with fresh water by pouring into flue inspection
plug opening.
8. Replace flue inspection plug.
Check all piping for leaks
Eliminate all system or boiler leaks. Continual fresh
make-up water will reduce boiler life. Minerals
can build up in sections, reducing heat transfer,
overheating heat exchanger, and causing heat
exchanger failure. Leaking water may also cause
severe property damage.
1. Inspect all water and gas piping and verify to be leak free.
2. Look for signs of leaking lines and correct any problems
found.
3. Check gas line using procedure on page 48.
Check air openings
1. Verify that combustion and ventilation air openings to the
boiler room and/or building are open and unobstructed.
Check operation and wiring of automatic combustion air
dampers, if used.
2. Verify that boiler vent discharge and air intake are clean and
free of obstructions.
Flue vent system and combustion air
piping
1. Visually inspect entire flue gas venting system (and air pip-
ing, if installed) for blockage, deterioration or leakage. Repair
any joints that show signs of leakage in accordance with vent
manufacturer’s instructions. When air is ducted to boiler,
verify that air inlet pipe is connected and properly sealed.
Failure to inspect for the above conditions and have
them repaired can result in severe personal injury
or death.
Check water system
1. Verify all system components are correctly installed and
operational.
2. Check the cold fill pressure for the system. Verify it is correct
(usually around 12 psig).
3. Watch the system pressure as the boiler heats up (during
testing) to ensure pressure doesn’t rise too high. Excessive
pressure rise indicates expansion tank sizing or performance
problem.
4. Inspect automatic air vents and air separators. Remove air
vent caps and briefly press push valve to flush vent. Reinstall
caps. Make sure vents do not leak. Replace any leaking vents.
5. Check system water chemistry (inhibitor concentration, pH
and hardness). See page 83.
Annual startup
(continued)
Содержание 550 MBH
Страница 126: ...Part number 550 100 168 0516 126 SlimFit Series 3 COMMERCIAL CONDENSING GAS FIRED WATER BOILER Boiler Manual Notes ...
Страница 127: ...Part number 550 100 168 0516 127 SlimFit Series 3 COMMERCIAL CONDENSING GAS FIRED WATER BOILER Boiler Manual Notes ...
Страница 128: ...GAS FIRED WATER BOILER Boiler Manual SlimFit Series 3 COMMERCIAL CONDENSING GAS FIRED WATER BOILER Boiler Manual ...