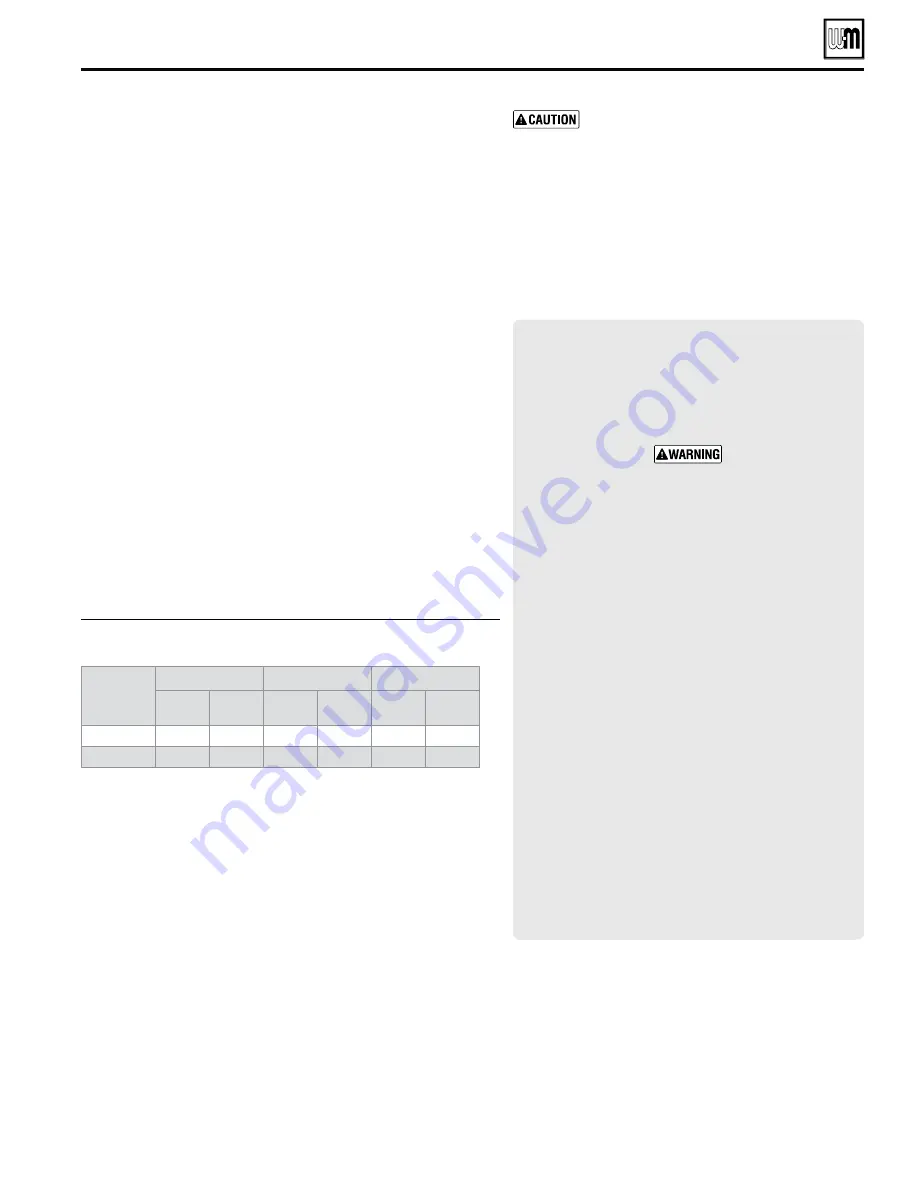
Part number 550-100-168/0516
95
Check flue gas temperature
1. Set the boiler to high fire. Then adjust the Control module display
to view flue gas temperature and boiler return temperature.
2. The flue gas temperature should be no more than 54 °F higher than
the boiler return temperature.
3. If the flue temperature is higher than this, shut down the boiler, al-
low to cool, and follow the procedure starting on page 105 to clean
the heat exchanger.
Check blower speeds
1. For installations at altitudes above 5,500 feet, make sure the control is
set up for high altitude in the boiler setup menu. The Control module
automatically adjusts low fire and ignition rates to compensate for
high altitude conditions.
2. For installations below 5,500 feet, DO NOT enable high altitude.
3. Use the Control display to navigate to Manual test mode (see
Figure 68, page 78).
4. Set the firing rate to Low (low fire).
5. Write down the blower RPM value shown and compare to the value
in the table below. Low fire rate (and corresponding blower speed)
is adjusted in the boiler setup menu.
6. Set the firing rate to MEDIUM (ignition rate).
7. Write down the blower RPM value. It should be within 200 RPM of
the value listed in the table below.
8. Set the firing rate to High (high fire).
9. Write down the blower RPM value. It should be within 200 RPM of
the value given in the table below.
10. If any of the values are outside the ranges listed in the previous steps,
contact the factory for technical assistance.
&IGURE
Blower speeds for altitudes up to 5,500 feet (factory
setting) and high altitude (over 5,500 ft)
-ODEL
3LIM&ITn
,OWlRE
)GNITION
(IGHlRE
Factory
setting
High
altitude
Factory
setting
High
altitude
Factory
setting
Maximum
setting
550
1300
1900
2500
2800
5725
5950
750
1300
1825
2350
2650
5275
5500
Check boiler relief valve
1. Inspect the relief valve and lift the lever to verify flow as
in the following warnings, excerpted from a relief valve
manufacturer’s warning label. Before operating any relief
valve, ensure that it is piped with its discharge in a safe
area to avoid severe scald potential. Read “
Install water
piping
” starting on page 12, before proceeding further.
Safety relief valves should be reinspected AT LEAST ONCE
EVERY THREE YEARS, by a licensed plumbing contractor
or authorized inspection agency, to ensure that the product
has not been affected by corrosive water conditions and
to ensure that the valve and discharge line have not been
altered or tampered with illegally. Certain naturally occur-
ring conditions may corrode the valve or its components
over time, rendering the valve inoperative. Such conditions
are not detectable unless the valve and its components are
physically removed and inspected. This inspection must
only be conducted by a plumbing contractor or authorized
inspection agency — not by the owner. Failure to reinspect the
boiler relief valve as directed could result in unsafe pressure
buildup, which can result in severe personal injury, death or
substantial property damage.
Following installation, the valve lever must be operated AT
LEAST ONCE A YEAR to ensure that waterways are clear.
Certain naturally occurring mineral deposits may adhere to
the valve, rendering it inoperative. When manually operating
the lever, water will discharge and precautions must be taken
to avoid contact with hot water and to avoid water damage.
Before operating lever, check to see that a discharge line is
connected to this valve directing the flow of hot water from
the valve to a proper place of disposal. Otherwise severe per-
sonal injury may result. If no water flows, valve is inoperative.
Shut down boiler until a new relief valve has been installed.
2. If the relief valve weeps or will not seat properly, replace
the relief valve. Ensure that the reason for relief valve
weeping is the valve and not over-pressurization of the
system due to expansion tank waterlogging or under-
sizing.
SlimFit
®
Series 3
COMMERCIAL
CONDENSING
GAS
-
FIRED
WATER
BOILER
—
Boiler Manual
Manual Test Mode for Single and
Multiple Boilers
Single Boiler
1. Navigate to Manual Test Mode screen under DIAGNOSTICS menu.
2. Generate a call for heat and wait until the burner is lit, if not yet in
operation.
3. Press ENTER and select the desired FORCE RATE. Rate will be
forced to setting for 10 minutes.
Multiple Boiler Running
1. Generate a call for heat on a Network Priority or a Local Priority
a. Local Priority—allows Force Rate only on the boiler with the
call for heat. Follow Single Boiler procedure, above.
b. Network Priority—allows Force Rate on any boiler in the net-
work. Follow procedure outline below in steps 2-5.
2. On the Master boiler, navigate to Manual Test Mode screen under
DIAGNOSTICS menu. Select desired boiler to be tested.
3. The Manual Test Mode screen will automatically appear on the boiler
you selected. On the selected boiler’s control, press ENTER and select
the desired FORCE RATE (HIGH, MED, OR LOW).
Review with owner
1. Review the User’s Information Manual with the owner.
2. Emphasize the need to perform the maintenance sched-
ule specified in the User’s Information Manual (and in
this manual as well).
3. Remind the owner of the need to call a licensed con-
tractor should the boiler or system exhibit any unusual
behavior.
4. Remind the owner to follow the proper shutdown proce-
dure and to schedule an annual startup at the beginning
of the next heating season.
When forcing a rate on a Network Priority
call, only boilers running Local Priority
calls will remain on. All other boilers on
the network will not fire until the Manual
Test has ended. Ensure critical applications
remain heated. Long periods of low heating
can cause property damage.
4. The selected boiler will run at the forced rate until it is
either returned to AUTO, the user selects “End Manual
Test” on the Master’s Manual Test Mode screen, or after
30 minutes of inactivity on the Master control.
5. To test the next boiler, return to the master and select
the next desired boiler to test.
Annual startup
(continued)
Содержание 550 MBH
Страница 126: ...Part number 550 100 168 0516 126 SlimFit Series 3 COMMERCIAL CONDENSING GAS FIRED WATER BOILER Boiler Manual Notes ...
Страница 127: ...Part number 550 100 168 0516 127 SlimFit Series 3 COMMERCIAL CONDENSING GAS FIRED WATER BOILER Boiler Manual Notes ...
Страница 128: ...GAS FIRED WATER BOILER Boiler Manual SlimFit Series 3 COMMERCIAL CONDENSING GAS FIRED WATER BOILER Boiler Manual ...