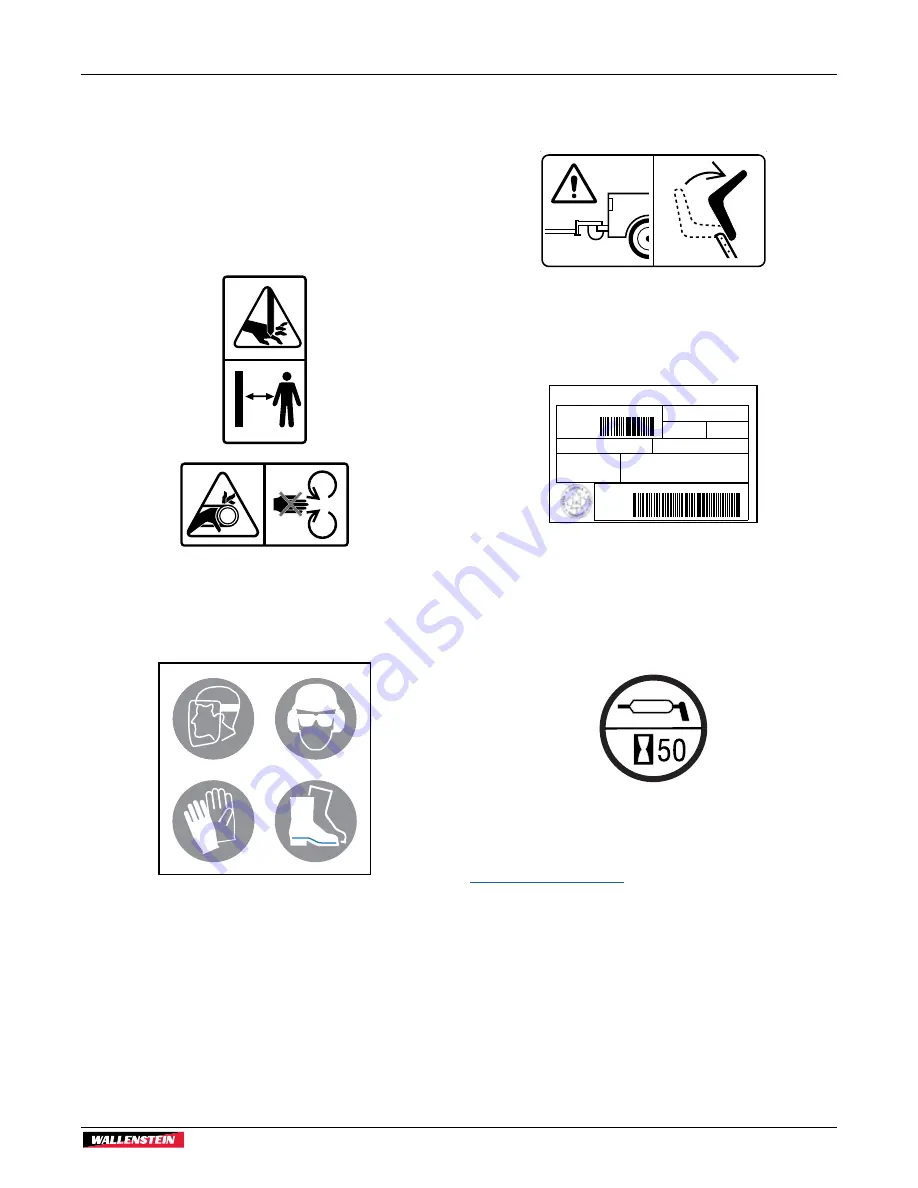
WP1624 Series
Firewood Processor
Introduction
7
1.4 Types of Decals on the Machine
When getting familiar with the Wallenstein product, notice that
there are numerous decals located on the machine. There are
different types of decals for safety, information, and product
identification. The following section explains what they are for
and how to read them.
Safety Decals
have a yellow background and are generally two
panel. They can be either vertical or horizontal.
Safety Notice
decals have a blue background and are generally
rectangular with single or multiple symbols. This decal shows
suggested PPE requirements for safe operation.
Informative
decals have a white background and can vary in the
number of panels. These decals provide operating information
on a feature of the machine.
Product
decals are associated with the product and carry
various messages such as model, serial number, and
manufacturer.
VIN/
NLV:
MODEL: ##########
#########
Manufactured by:
Wallenstein Equipment Inc., 7201 Line 86, Wallenstein ON N0B2S0, Canada
TYPE OF VEHICLE/TYPE DE VEHICLE:
TRA / REM
GAWR/PNBE (KG): GVWR/PNBV (KG):
###
DIMENSION- RIM/JANTE
/
E
R
I
T
:
PNEU:
COLD INFL. PRESS/PRESS DE
CONFLA A FROID (PSI/LPC):
THIS VEHICLE CONFORMS TO ALL APPLICABLE STANDARDS
PRESCRIBED UNDER THE CANADIAN MOTOR SAFTEY REGULATIONS
IN EFFECT ON THE DATE OF MANUFACTURE / CE VEHICLE EST
CONFORME A TOUTES LES NORMES QUI LUI SONT APPLICABLES EN
VERTU DU REGLEMENT SUR LA SECURITE DES VEHICLES
AUTOMOBILES DU CANADA EN VIGUEUR A LA DATE DE SA FABRICATION.
###
###
###
###
Maintenance
decals have a green background. They can have
various messages and vary in the number of panels. These
decals indicate the maintenance type and can indicate the
service interval. Maintenance decals are further explained in the
Service and Maintenance section.
For complete illustrations of decal locations on the machine,
download the parts manual for this product model at
Содержание P3 PULSE WP1624
Страница 18: ...WP1624 Series Firewood Processor Safety 18 Safety Signs 0 4 3 9 10 5 14 8 13 15 Fig 4 Safety Decal Locations...
Страница 62: ...Service and Maintenance WP1624 Series Firewood Processor 62 1 2 4 5 6 3 Fig 76 Lubrication Diagram...
Страница 87: ......
Страница 88: ...WallensteinEquipment com...