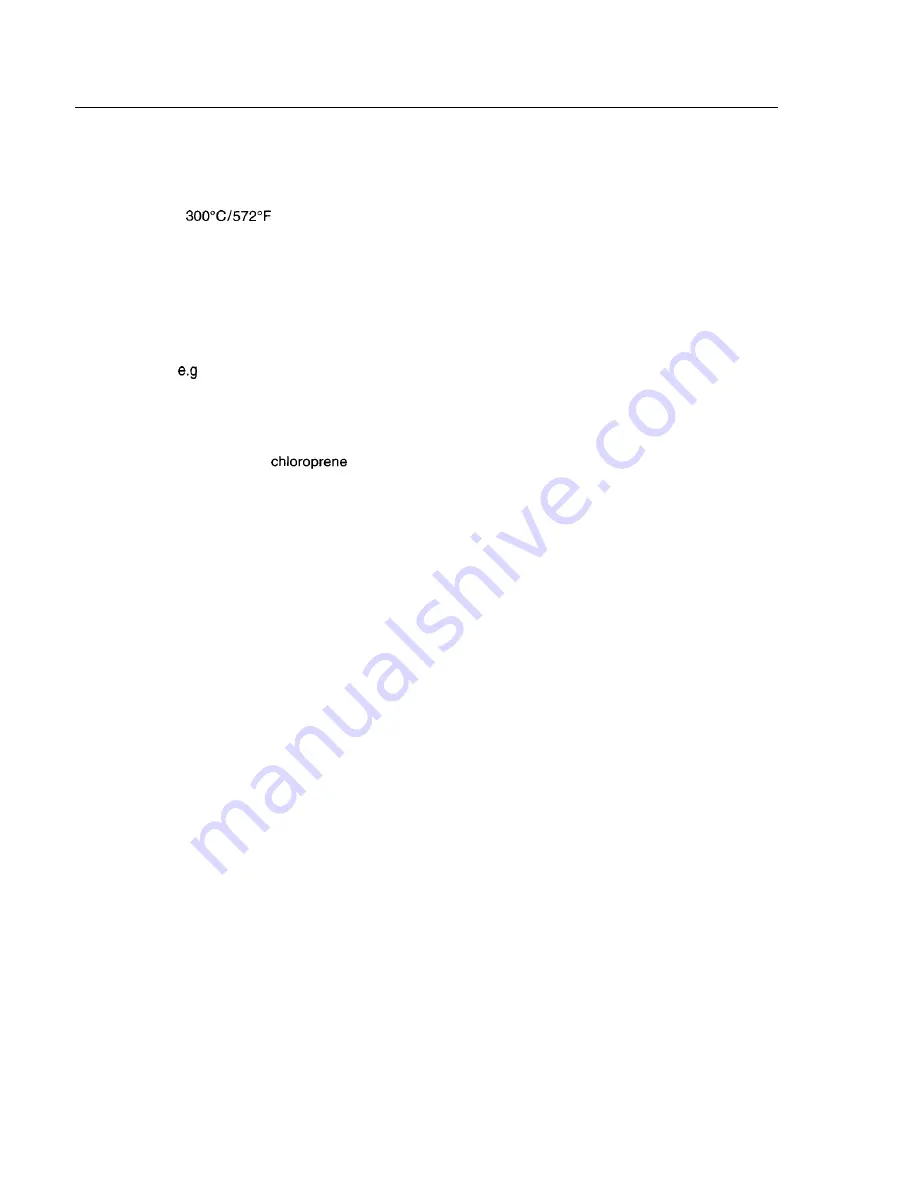
Safety rules for fluorocarbon rubber
Fluorocarbon rubber is a common material in seal
rings for shafts, and in O-rings, for example.
When fluorocarbon rubber is subjected to high tem-
peratures (above
),
hydrofluoric acid
can be formed, which is highly corrosive. Skin con-
tact can give severe chemical burns. Splashes in
your eyes can give severe chemical burns. If you
breathe in the fumes, your lungs can be permanently
damaged.
4
f
WARNING!
Be very careful when working on
engines which have been exposed to high tem-
peratures,
. overheating during a seizure or
fire. Seals must never be cut with an oxyacet-
ylene torch, or be burned up afterwards in an
uncontrolled manner.
•
Always use gloves made of
rubber
(gloves for handling chemicals) and protective
goggles.
•
Handle the removed seal in the same way as
corrosive acid. All residue, including ash, can be
highly corrosive. Never use compressed air to
blow anything clean.
•
Put the remains in a plastic box which is sealed
and provided with a warning label. Wash the
gloves under running water before removing
them.
The following seals are probably made from fluoro-
carbon rubber:
Seal rings for the crankshaft, camshaft, intermediate
shafts.
O-rings irrespective of where they are installed.
O-rings for cylinder liner sealing are almost always
made from fluorocarbon rubber.
Note that seals which have not been subjected to
high temperature can be handled normally.
8
Содержание MD2010
Страница 1: ...Workshop Manual Engine MD2010 MD2020 MD2030 MD2040 A 2 0 ...
Страница 20: ...Presentation 20 2 3 MD201OA B MS2L 17 16 15 14 MD2010A B MS2L 13 ...
Страница 80: ...Notes ...