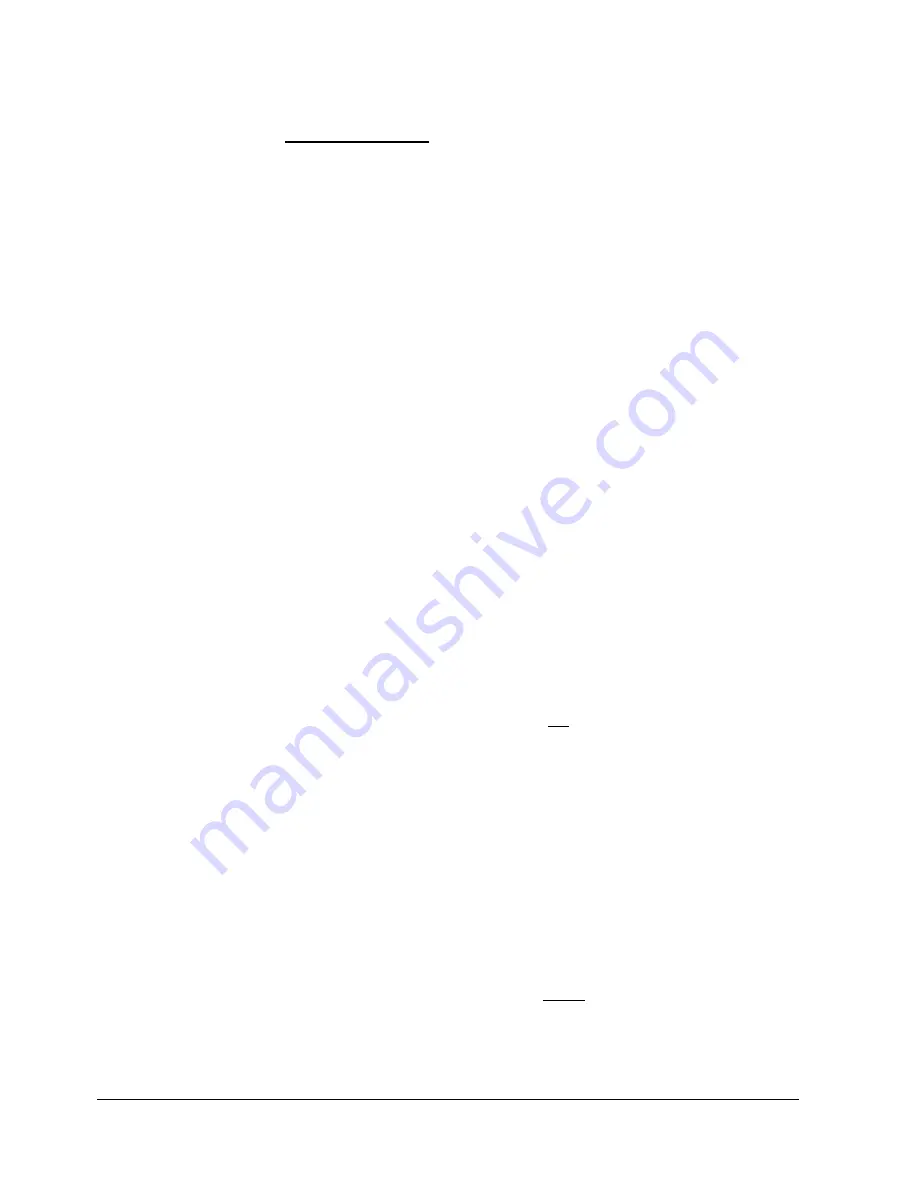
Technical Reference
Manual-XPM3m Revision Date: August 2014
DC DRIVE CALIBRATION
(RAIL WIDTH ONLY)
1.
Definitions-
A DC drive is actually a DC voltage amplifier. A small signal is sent to the drive and a large voltage is sent
to the motor. The typical DC drive uses an AC power source of 120 or 240 volts.
The set of controls found on a DC drive is:
A.
Minimum speed adjust
B.
Maximum speed adjust
C.
IR comp
D.
Torque
E.
Signal
2.
What do the controls do?
A.
Minimum speed adjust -- adjusts the minimum voltage output of the DC drive at the minimum-input
value. This value is typically 0 - 10% of the maximum input voltage.
B.
Maximum speed adjust – not used.
C.
IR comp -- this adjusts the feedback circuit from the output of the DC drive. If the output voltage
drops, the IR comp circuit senses the drop, and more power is fed to the motor. This function is
preset to a value that covers 90% of all applications.
D.
Torque -- this limits output current, and should only be adjusted by experienced people.
G.
Signal -- signal adjust is found on DC drives which provide an option of being controlled by a
computer. If the DC drive is adjusted by a speed control potentiometer, signal or signal adjust has
no function.
Note
: A DC drive with computer control will have a signal/manual selector switch or jumper. If the input
does not match the input selected, the DC drive will not operate correctly.
If a computer controls the DC drive, the maximum adjustment potentiometer will have no function.
3.
Additional useful information
A.
Always recalibrate when any component of a control system is changed.
B.
Conveyor speed can be calibrated to specific requirements. This takes practice, but can yield
greater speed accuracy.
C.
The conveyor speed should be measured with a stopwatch every sixty days.
D.
Motor brushes wear out.
E.
Calibration values may change with the age of the system.
F.
Always record the adjusting potentiometer settings before replacing or calibrating a DC drive.
G.
When replacing a DC drive, record the potentiometer settings; draw a sketch of the wire hookups;
make sure all wires have labels.
Содержание XPM3m
Страница 79: ...Technical Reference Manual XPM3m Revision Date August 2014 LIGHT TOWER Continued ...
Страница 90: ...Technical Reference Manual XPM3m Revision Date August 2014 ENHANCED COOLING PACKAGE EC 1 FLOW DIAGRAM ...
Страница 92: ...Technical Reference Manual XPM3m Revision Date August 2014 ENHANCED COOLING PACKAGE EC 2 FLOW DIAGRAM ...
Страница 94: ...Technical Reference Manual XPM3m Revision Date August 2014 ENHANCED COOLING PACKAGE EC 3 FLOW DIAGRAM ...