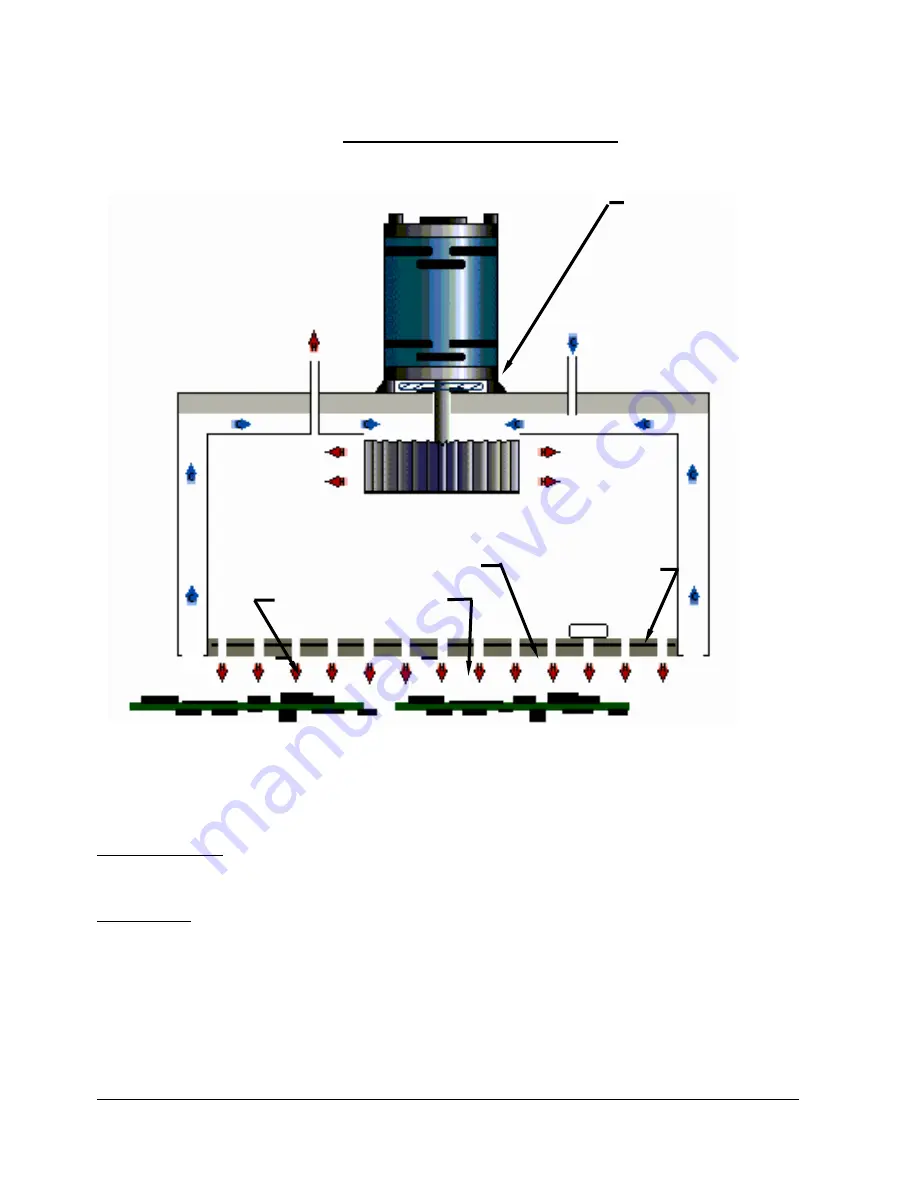
Technical Reference
Manual-XPM3m Revision Date: August 2014
XPM3m HEATING CELL DESCRIPTION
HEATING CELL CROSS-SECTION
CONSTRUCTION:
The heat Cells are assembled and sealed as self-contained units with the Fan Motor, and Over
Temperature Switch mounted and wired to terminals, and the Thermocouples (1 or 2) mounted and wired to
connectors.
OPERATION:
The relatively thick heater assembly has a series of holes allowing heat transfer to the oven gases
passing from the Cell Cavity to the process tunnel.
Recirculation occurs through the low-pressure intakes at the sides of the Cell. These gasses are drawn into the cell
cavity, where they are passed through the heater and back into the process tunnel.
Fan Speed controls the velocity of the heated atmosphere, which influences the heat transfer to the PCB.
FAN MOTOR
INSULATION
EXHAUST
HEATER ASSEMBLY
THERMOCOUPLES
OVER TEMPERATURE
SWITCH
HEAT SLINGER
FAN BLADES
AIR OR
NITROGEN IN
Содержание XPM3m
Страница 79: ...Technical Reference Manual XPM3m Revision Date August 2014 LIGHT TOWER Continued ...
Страница 90: ...Technical Reference Manual XPM3m Revision Date August 2014 ENHANCED COOLING PACKAGE EC 1 FLOW DIAGRAM ...
Страница 92: ...Technical Reference Manual XPM3m Revision Date August 2014 ENHANCED COOLING PACKAGE EC 2 FLOW DIAGRAM ...
Страница 94: ...Technical Reference Manual XPM3m Revision Date August 2014 ENHANCED COOLING PACKAGE EC 3 FLOW DIAGRAM ...