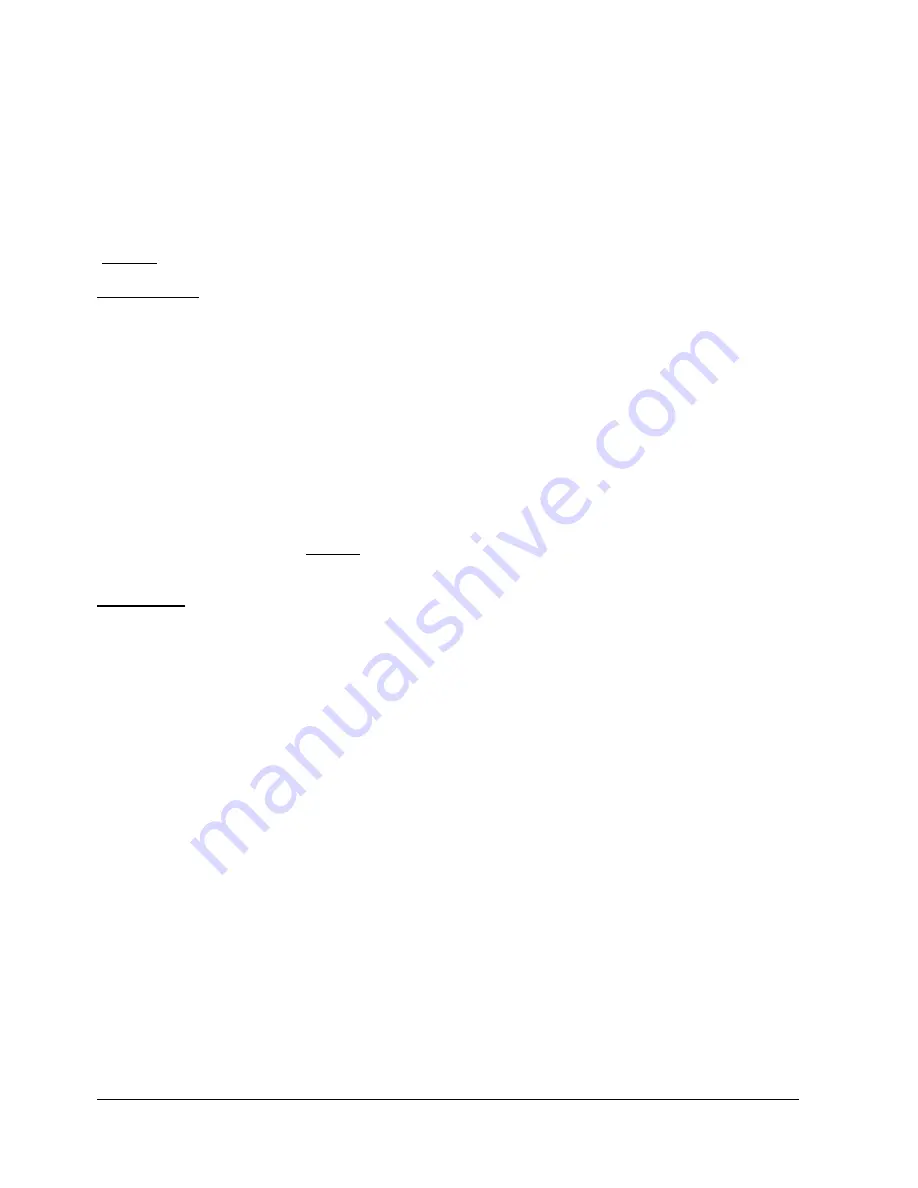
Technical Reference
Manual-XPM3m Revision Date: August 2014
SMEMA INTERFACE
The SMEMA Interface is:
Standard, (installed on all ovens
)
An option, (NOT installed on all ovens)
(SMEMA is the acronym for Surface Mount Equipment Manufacturer’s Association)
DESCRIPTION
On the XPM3m, all SMEMA functionality is built into the oven controller and an external PLC is not used.
The XPM3m utilizes a board tracking/SMEMA interface circuit board E3151801 located on the on-load and off-load
ends of the oven, and photo-sensors are mounted on brackets above each end of the oven. A 14 pin round AMP
connector is attached to cables on each end of the Reflow Oven.
Each E3151801 board supports the following:
1. Connections for 3 board tracking sensors per on-load and or off-load.
2. Connections for 2 lanes of SMEMA control. A relay must be installed onto a socket on each E3151801 board for
each SMEMA lane (one on the on-load, one on the off-load).
3. LED status indicators for board tracking sensors and SMEMA output relays.
NOTE:
Ovens with a Dual Rail conveyor (with two sets of rails and chains) have two separate sets of SMEMA Interface
sensors. Each conveyor must be ready to receive product before it independently sends a “Ready” signal to its
respective “upline” equipment. EITHER conveyor can send a “Product at Offload” signal to the “downline”
equipment.
OPERATION
Action by the Reflow Oven operator is not necessary for the SMEMA interface to function. As long as the upline /
downline connections are made and a component failure has not occurred, operation will be automatic when the
Reflow Oven is powered up.
The SMEMA interface accepts a 'Board Available' signal from the upline (onload side) of the Reflow Oven on pins
3&4 of the onload connector. It replies with a 'Busy' signal on pins 1&2 of the onload connector to the machine
upline. On the downline (offload) side, a 'Board Available' signal is sent on pins 3&4 and looks for a 'Busy' signal to
come back on pins 1&2 of the offload connector.
Because the Reflow Oven should not be stopped with product in the heat zone, the busy signal coming from the
downline end is used to generate the busy signal for the upline equipment without stopping the Reflow Oven. When
all of the conditions are ‘False’, the Reflow Oven is “not busy” and will accept more product from the upline
equipment. If any of the conditions are ‘True’, the Reflow Oven will transmit a "busy" signal to the upline equipment.
This should stop the upline equipment from sending product to the Reflow Oven, thus preventing a product buildup.
The upline “busy” signal can be a result of one (or more) of the following:
1. Board at ‘on-load’
2. Board Jam at off-load
3. Downline machine is not ready
4. Oven is not ‘Process Ready’
Содержание XPM3m
Страница 79: ...Technical Reference Manual XPM3m Revision Date August 2014 LIGHT TOWER Continued ...
Страница 90: ...Technical Reference Manual XPM3m Revision Date August 2014 ENHANCED COOLING PACKAGE EC 1 FLOW DIAGRAM ...
Страница 92: ...Technical Reference Manual XPM3m Revision Date August 2014 ENHANCED COOLING PACKAGE EC 2 FLOW DIAGRAM ...
Страница 94: ...Technical Reference Manual XPM3m Revision Date August 2014 ENHANCED COOLING PACKAGE EC 3 FLOW DIAGRAM ...