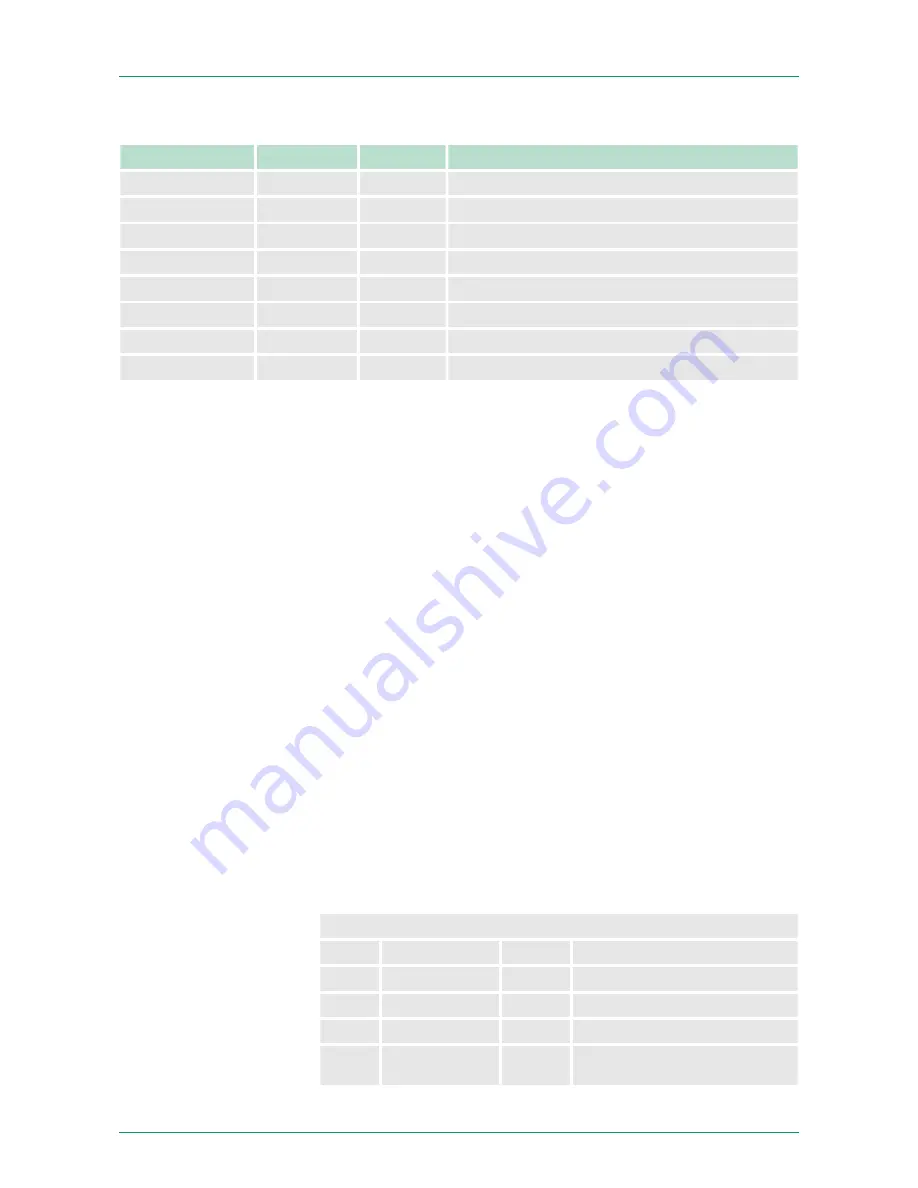
Parameter
Declaration
Data type
Description
PROTOCOL
IN
BYTE
1=ASCII, 2=STX/ETX, 3=3964R
PARAMETER
IN
ANY
Pointer to protocol-parameters
BAUDRATE
IN
BYTE
Number of baudrate
CHARLEN
IN
BYTE
0=5bit, 1=6bit, 2=7bit, 3=8bit
PARITY
IN
BYTE
0=Non, 1=Odd, 2=Even
STOPBITS
IN
BYTE
1=1bit, 2=1.5bit, 3=2bit
FLOWCONTROL IN
BYTE
1 (fix)
RETVAL
OUT
WORD
Return value (0 = OK)
All time settings for timeouts must be set as hexadecimal value. Find
the Hex value by multiply the wanted time in seconds with the bau-
drate.
Example:
Wanted time 8ms at a baudrate of 19200baud
Calculation: 19200bit/s x 0.008s ≈ 154bit → (9Ah)
Hex value is 9Ah.
Here you fix the protocol to be used.
You may choose between:
1: ASCII
2: STX/ETX
3: 3964R
4: USS Master
5: Modbus RTU Master
6: Modbus ASCII Master
At ASCII protocol, this parameter is ignored.
At STX/ETX, 3964R, USS and Modbus you fix here a DB that con-
tains the communication parameters and has the following structure
for the according protocols:
Data block at STX/ETX
DBB0: STX1
BYTE
(1. Start-ID in hexadecimal)
DBB1: STX2
BYTE
(2. Start-ID in hexadecimal)
DBB2: ETX1
BYTE
(1. End-ID in hexadecimal)
DBB3: ETX2
BYTE
(2. End-ID in hexadecimal)
DBW4: TIMEOUT
WORD
(max. delay time between 2
telegrams)
Parameters
PROTOCOL
PARAMETER (as DB)
VIPA System 300S CPU
Deployment PtP communication
Parametrization> FC/SFC 216 - SER_CFG
HB140 | CPU | 315-2AG13 | GB | Rev. 14-40
94