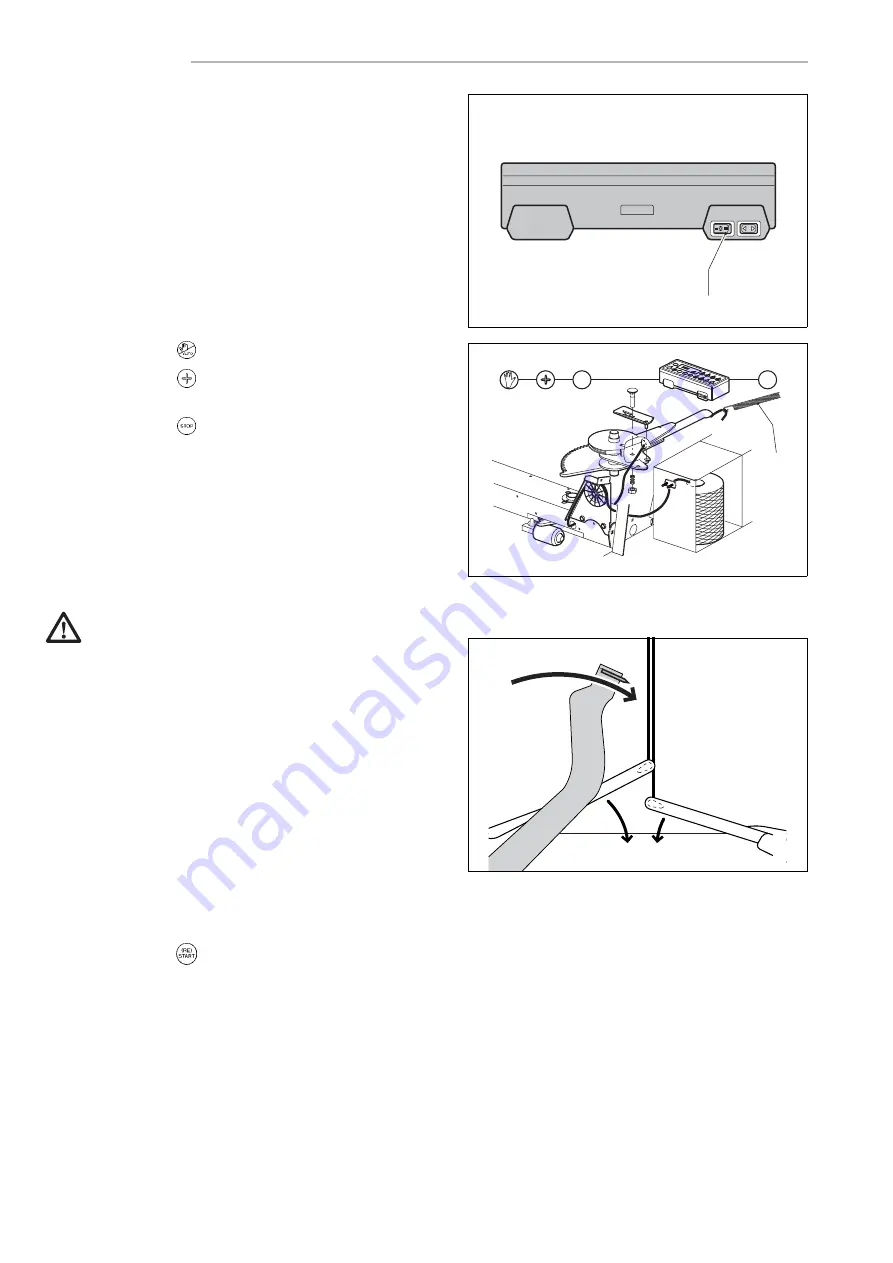
Chapter 9
G0201WAD3EN
57
twine tie
9.5.3
Routing the twine - AUTOFORM
1
Set the main switch of the control box to 1 (ON).
2
Push button
to go to manual mode.
3
Push button
until arms are pointing straight back-
ward into bale chamber.
4
Push button
to shut down the system.
DANGER
Special caution is required within in the area of the
very sharp twine cutting knife that cuts the twine at the
end of every cycle!
5
Guide the twine in accordance with the diagram
through the mechanism (both lh and rh sides).
Use spring (4) to run the twine through the tube.
The twine ends shall protrude about 10 cm (4") out of
the tying tubes.
6
Push button
to move the system in its starting posi-
tion.
16
W
A9921
(RE)
STAR
T
STOP
PROG
AUT
O
AUTO
Ps
50
80
START
STOP
1
2
3
5
W
A0059
4
W
A9943
Содержание RV 1601
Страница 1: ...G0201WAD3EN RV 1601 RV 1901 Operation manual WA0080 ...
Страница 2: ......
Страница 4: ......
Страница 8: ...G0201WAD3EN 6 Preface ...
Страница 106: ...G0201WAD3EN 104 ...
Страница 107: ......