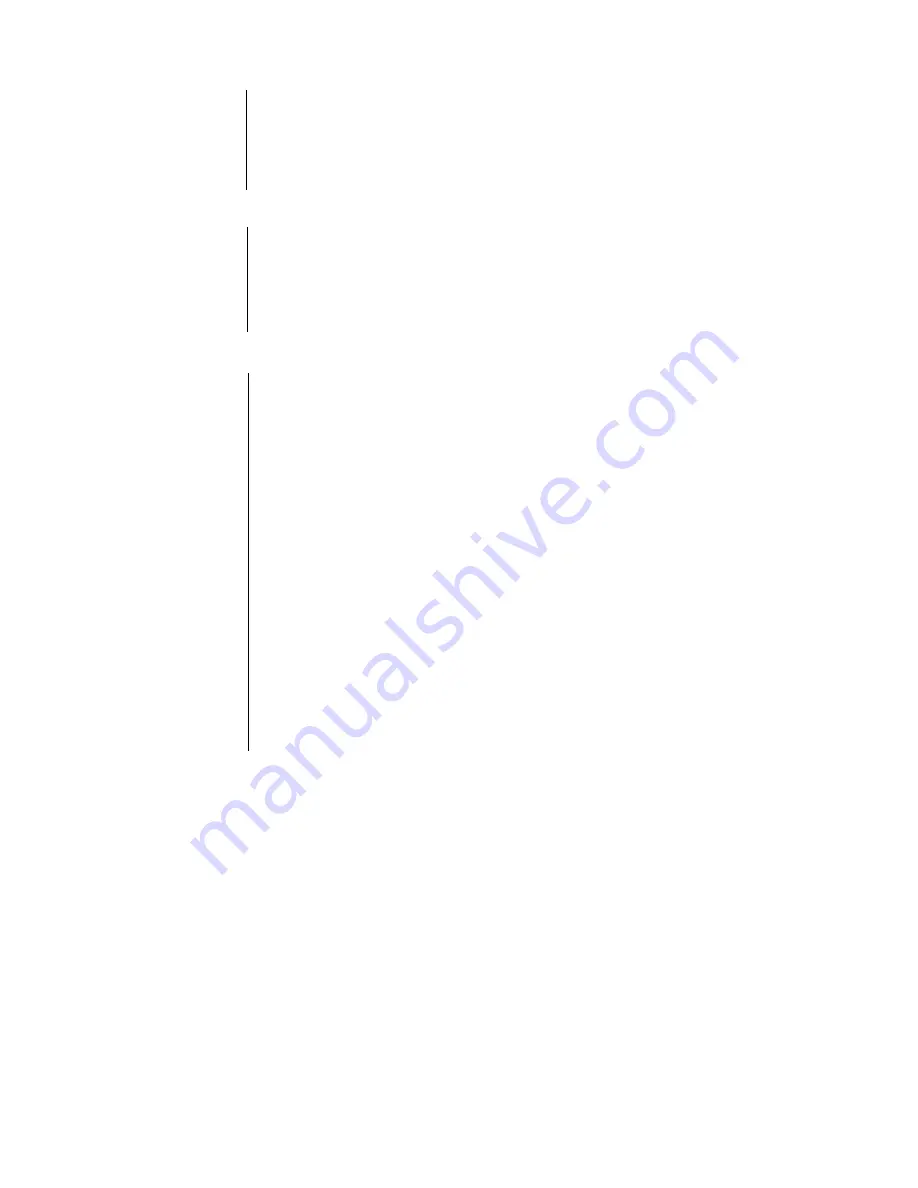
Solenoid repetitive cutting in and out
1. Battery discharged
2. Excessive voltage drop in sole-
noid power circuit caused by
badly oxidized lead ends
3. Solenoid holding winding bro-
ken or shorted
Starter motor armature rotates, flywheel inoperative
1. Overrun clutch slipping
2. Clutch operating lever broken
or pivot shaft dropped
3. One-way clutch guide ring or
buffer spring broken
Starter motor noisy
1. Starter motor retaining nuts
loose or drive-end housing broken
2. Starter wrongly mounted
3. Bearing shells or armature shaft
journals excessively worn
4. Stator pole loose (armature
touches pole)
5. Pinion or ring gear teeth dam-
aged
6. Pinion fails to disengage ring
gear:
- operating lever seized;
- overrun clutch jams in mesh with
armature shaft splines;
- clutch or solenoid springs loose
or broken;
- clutch hub circlip lost;
- solenoid armature sticking;
- ignition switch contact part faulty:
pins 30 and 50 fail to open
Starter motor - bench testing
If the starter motor fails to operate effectively, check it using
a tester. The wiring connections for the test are shown in Fig.7-
15. The cross-sectional area of leads to power source, ammeter
and starter solenoid terminal bolt should be at least 16 mm
2
.
The starter motor test temperature should be (25±5)
°
ë. The
brushes must slide smoothly on the commutator.
Functional test.
By closing switch 5 (Fig.7-15), operate the
starter motor three times from a 12 volt source at different braking
conditions, eg. at the braking moments of 2; 6 and 10 N•m (0.2; 0.6
and 1 kgf•m). The starter motor should be switched on for no longer
than 5 seconds with minimum 5 second intervals in-between.
If the starter motor fails to turn the tester ring gear or pro-
duces unusual noise, dismantle the starter motor and examine its
components.
Fully locked ring test.
Lock the tester ring gear, operate the
starter motor and measure the current, voltage and braking
moment to be maximum 550 amps, 7.5 volts and at least 13.7
N•m (1.4 kgf•m) respectfully. Do not switch on the starter motor
for over than 5 seconds.
When the braking moment is below, while the current is over
the values specified, the likely reason is an internal short-circuit of
the stator or armature winding or earthed winding.
When the braking moment and current are below the values
specified, the possible cause is an oxidized or dirty commutator,
severely worn brushes or weak springs, sticking brushes, loose
stator winding terminals, eroded or burnt solenoid terminal bolts.
At fully locked condition, the starter armature must not turn;
when otherwise the one-way clutch is faulty.
Dismantle the starter motor, replace or overhaul damaged
components to remedy the situation.
No-load test.
Disengage the tester ring gear from the starter
motor pinion. Operate the starter motor, measure the current flow
and armature shaft speed to be respectively maximum 60 amps
and (5000±1000) rpm at 11.5-12 volts across the starter motor
terminals.
If the amperage and drive shaft rpm readings differ from the
values specified, the possible causes are likely to be the same as
those for the test described above.
Solenoid test.
Insert a shim of 12.8 mm between stop collar
21 (Fig.7-13) and pinion and operate the solenoid. The solenoid
cut-in voltage, with the pinion resting against the shim, should not
exceed 9 volts at ambient (20±5)
°
ë. Any higher voltage indicates
the solenoid or drive failure.
Starter motor relay.
The relay cut-in voltage should not
exceed 8 volts at (23±5)
°
ë. When higher, it is an indication of a
failed relay or drive.
Starter overhaul
Dismantling
Undo the nut on the lower solenoid terminal bolt and discon-
nect the stator winding lead. Undo the solenoid retaining nuts and
remove the solenoid. Remove the end cap (Fig.7-16) from the
pinion-end cover.
Unscrew and remove protective case 8. Recover lock ring 9,
undo clamp bolts 12 and separate yoke 11 with housing 5 from
housing 1 with armature 13.
Unscrew the brush holders from the stator winding leads,
then separate the yoke from the commutator end housing. Extract
springs 7 and brushes 6.
Undo the cotter pin and withdraw the lever and armature /
actuator assembly, next disconnect the operating lever.
147
1. Bench test starter motor, renew
overrun clutch
2. Renew lever or refit pivot shaft
3. Renew clutch
1. Tighten retaining nuts or over-
haul starter motor
2. Check starter fitting
3. Renew starter motor
4. Tighten pole retaining screw
5. Renew drive or flywheel
6. Carry out the following:
- renew operating lever;
- clean and lubricate splines with
motor oil;
- renew clutch or solenoid;
- renew damaged components;
- renew solenoid or eliminate stick-
ing
- check correct contact closing at
different key positions; renew faulty
contact unit
1. Recharge battery
2. Check leads and connections
between battery and solenoid ter-
minal 50
3. Renew solenoid
Содержание 21213
Страница 1: ...VAZ VEHICLES VAZ 21213 VAZ 21214 VAZ 21214 20 VAZ 21215 REPAIR MANUAL ...
Страница 8: ...8 Fig 2 2 Front sectional view of the engine ...
Страница 135: ...135 ...
Страница 136: ...136 ...