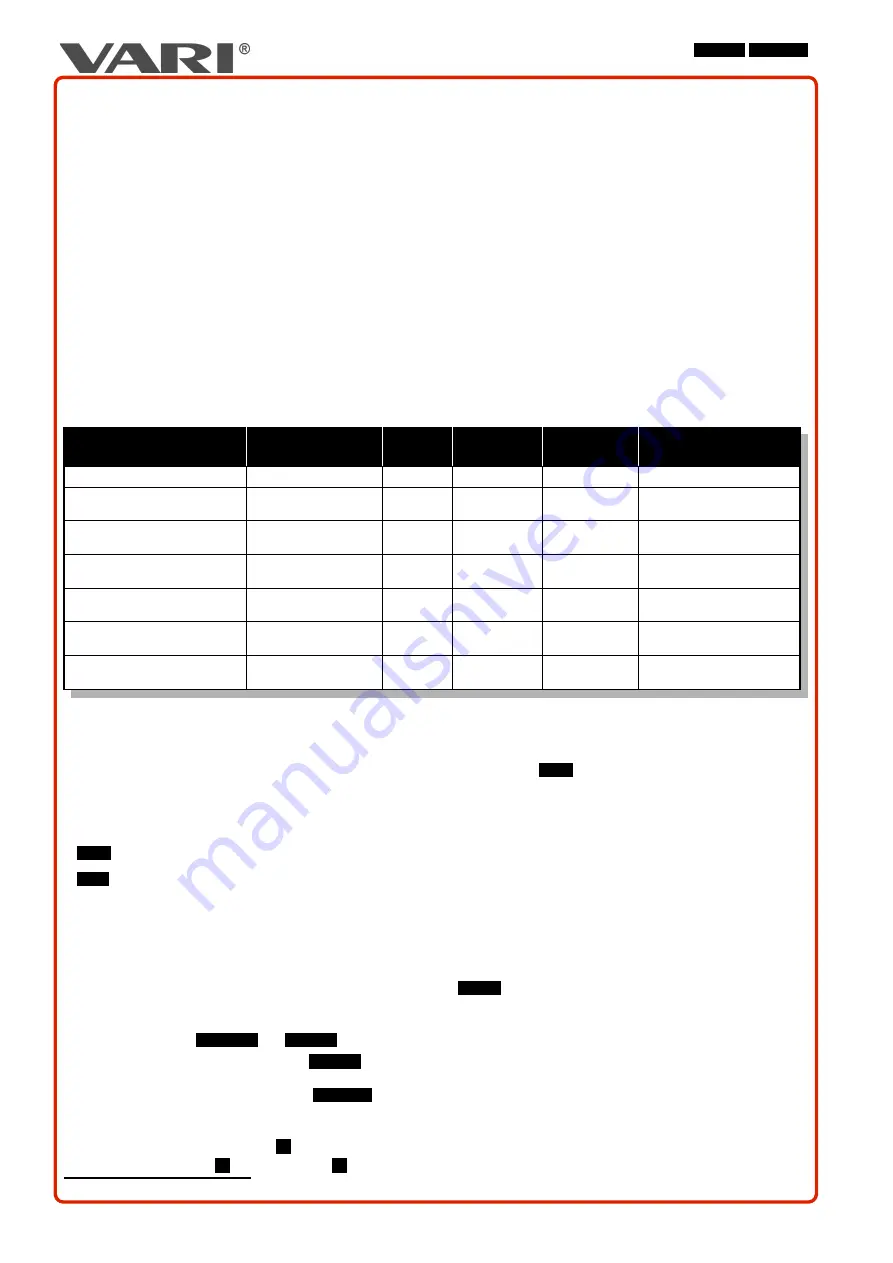
CB-800
CB-1000
2.7.3.2 G
EARBOX
OIL
CHANGE
•
The gearboxes are filled with oil with the volume and specifications per
•
The travel gearbox has a lifetime oil fill. If any oil leak is detected, contact the nearest authorised service centre.
•
Change interval for the drive gearbox per
.
•
To access the oil plug of the drive gearbox, it is necessary to remove both brushes-see
Chap. 2.7.5 Brush change
page 35
Fig. 27
•
Change oil when the gearbox is warmed up to its operating temperature.
•
Start the engine, close the fuel valve on the engine, and allow the engine to run until it shuts down from lack of fuel.
•
Remove the oil plug and pour the old oil into a prepared container by tilting the machine forward.
•
Fill the gearbox with fresh oil - do not overfill!
2.7.3.3 L
UBRICATION
P
OINTS
•
Of the commonly sold oils, any spray oil is suitable for lubrication. When selecting plastic lubricants (grease) any lubricant intended for
water pump lubrication is sufficient. However, its application usually requires the dismantling of the corresponding slide assembly. We also
recommend the use of so-called "white spray petroleum jelly", it flows well into the gaps and does not lose its lubricating properties in the
long term.
•
There is no need to remove any covers from the machine to lubricate the bowden cables on the handlebar. The other lubrication points
may be reached after removing the plastic covers.
Lubrication point -
description
Interval within
season
After
season
Lubricant
Figure
Note
Bowden cables
At least 2x (5 drops)
Yes
Oil
Cable entry to all the Bowdens
Drive pulley
Every 20 hours (2 drops)
Yes
Oil/lubricating
grease
Fig. 20
Arm housing
Travel clutch pulley
Every 20 hours (2 drops)
Yes
Oil/lubricating
grease
Fig. 21
Frame contact surface
Sweeper roller gearbox mount
-
Yes
Oil/lubricating
grease
Fig. 24
Wheel extraction control
After every machine
washing
Yes
Spray grease
Fig. 25
Thread end and sliding washer
Support wheel
After every machine
washing
Yes
Spray grease
Fig. 26
All the fork and wheel bearings
Handlebars - mounting
-
Yes
Lubricating
grease
Fig. 19
Screw connection
Table 20: Lubrication intervals
2.7.4 T
YRE
P
RESSURE
•
Keep the same pressure in the left and right wheels – the machine better holds a straight track.
•
Adjust tire pressure to MAX before shutting down the machine for long periods of time
MAX
.
Do not exceed the maximum tyre pressure – there is a risk of the tyre explosion!
If the pressure in the tyre is low, the inflation valve on the tube may get cut off.
•
MAX
imum
(recommended) tyre pressure:
20 PSI
(
137 kPa
or
1.38 bar
or
1.36 atm
or
0.138 MPa
)
•
MIN
imum
permissible tyre pressure:
18 PSI
(
124.1 kPa
or
1.24 bar
or
1.22 atm
or
0.124 MPa
)
•
If there is a permanent tyre pressure leakage, make sure that there is no defect on the tyre tube – repair it if necessary.
If you are not sufficiently manually skilled, have the operations done by an authorised tyre service centre.
2.7.5 B
RUSH
CHANGE
•
The minimum diameter limit when the brushes are already worn out, is
26 cm
.
Always replace both brushes,
even if only one of them is damaged. Different diameters result in poor sweeping function.
•
Fig. 27
shows a label
OUTSIDE
and
INSIDE
, the right orientation of the brushes in relation to the brush drive:
(a) Brushes for the 80 cm width of the
CB-800
machine must face the
drive
of the brushes with the additional bristles among the
spirals
(b) Brushes for the 100 cm width of the
CB-1000
machine must face outwards through their deeper cavity in the brush plastic tube
1.
Secure the machine against movement. Adjust the support wheel to the highest position, so that there is a gap of about 2 cm
from the ground under the bristles.
2.
Unscrew the
two M10 nuts
1
on the carrier bolt.
3.
Slide the brushes
2
out of the carriers
3
.
63
If the tyre pressure is lower than the minimum, the tyre-casing structure will be damaged and the service life will be significantly reduced.
35
re
vi
ze
1
2/
20
21