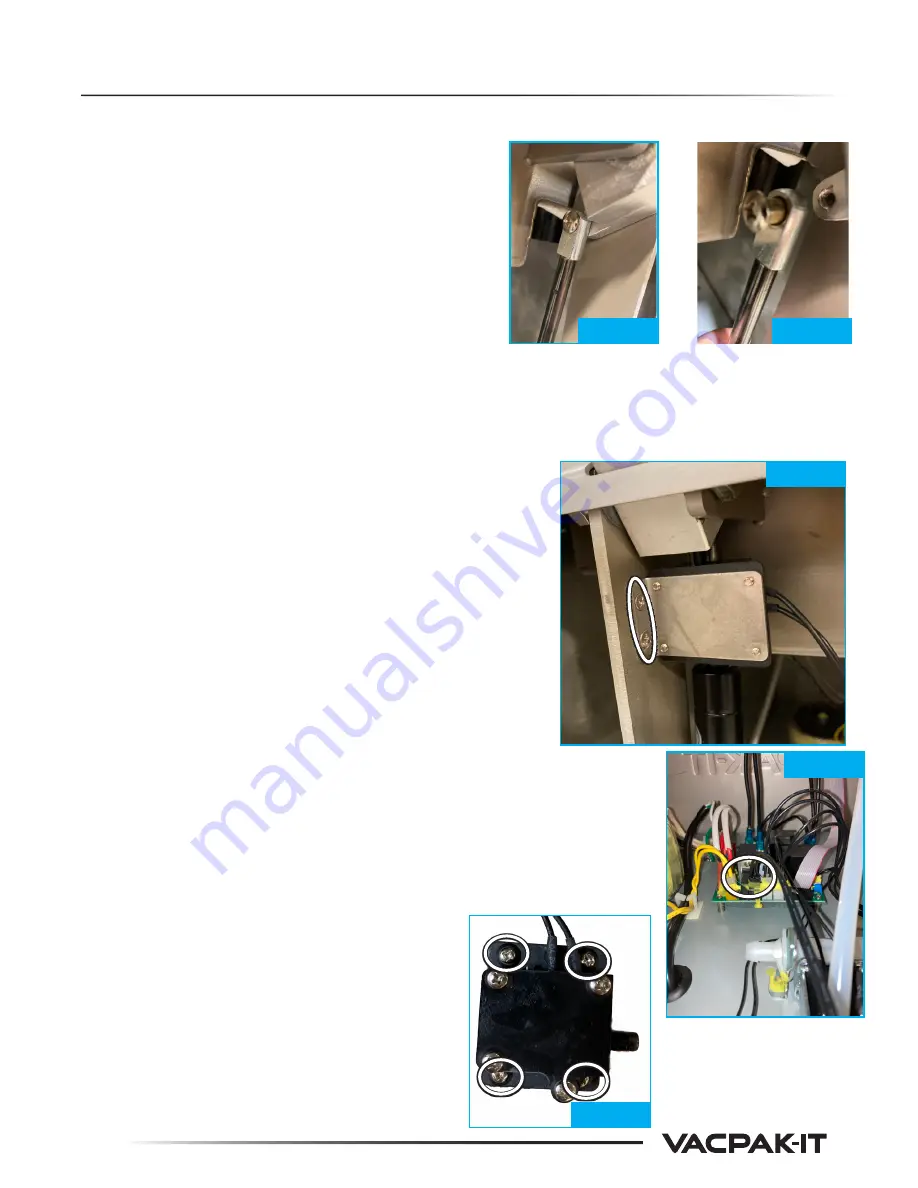
17
Part Replacement Continued
5. Remove Phillips head screw from upper Lid
Strut mounting tab (Fig. 27)
6. Remove Lid Strut from upper mounting post
(Fig. 28)
7. Installation is reverse of removal steps
Fig. 27
Fig. 28
Time Estimate: Approximately 10 minutes
Testing: Ensure mounting bracket is not bent or damaged
Good = Continuity between wires when toggle
pin is depressed
Bad = No continuity between wires when toggle
pin is depressed, replace
Part: #186PMICRSW2
1. Follow pre-maintenance steps on page 10
2. Remove Phillips head screws from the rear panel of
the machine
Note: 11 screws on 186VMC16F, 8 screws on
186VMC20F and 186VMC20FGF
3. Remove 2 Phillips head screws from microswitch
mounting plate (Fig. 29)
4. Disconnect wire plug from main circuit board (Fig. 30)
5. Remove 4 Phillips head screws from
mounting plate and remove microswitch (Fig. 31)
6. Installation is reverse of removal steps
Lid Microswitch
Fig. 29
Fig. 30
Fig. 31
Содержание 186VMC16F
Страница 22: ...22 Wire Diagram for VMC16F ...
Страница 23: ...23 Wire Diagram for VMC20F ...
Страница 24: ...24 Wire Diagram for VMC20FGF ...