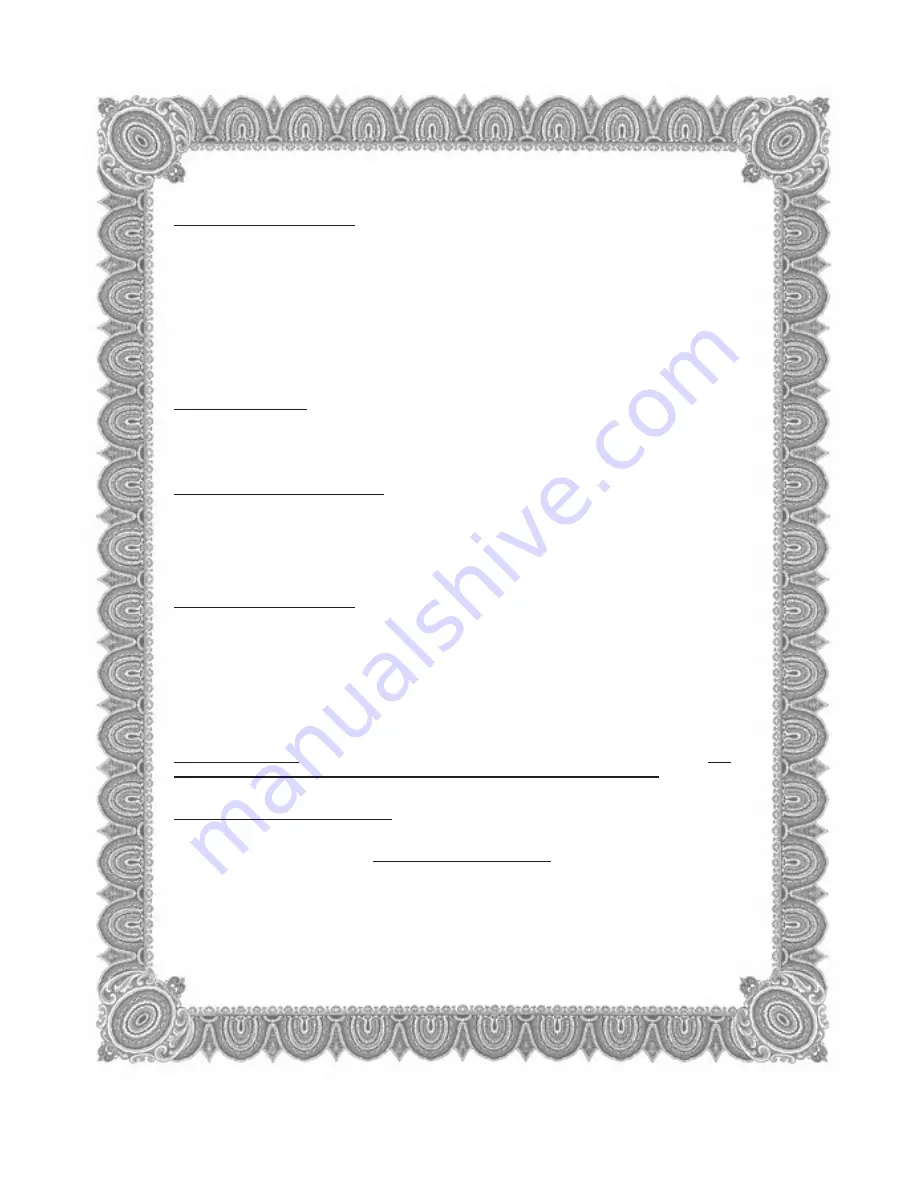
6
30A215-Mar2008
7
30A215-Mar2008
A. Warranty
ULTRAFRYER
®
LIMITED WARRANTY: IN-N-OUT BURGER – PDE VAT
Ultrafryer Systems warrants to the original purchaser of a gas or electric Ultrafryer
®
sold within the United States,
its territories and Canada, that it will be free of defects in material and workmanship for the periods listed below:
STAINLESS STEEL FRYER VAT –
Stainless Steel fryer vats are warranted for (10) ten years upon the terms herein-
after described. The (10) ten year warranty coverage applies ONLY to the Stainless Steel fryer vat and does not apply
to the other components such as controls, burner, gaskets, mounting hardware, or the baffles. The (10) ten year limited
warranty coverage for the Stainless Steel fryer vats are as follows: (1) Vats that fail due to faulty workmanship or materi-
als within the first sixty (60) months from the date of shipment will be exchanged at no cost. The cost of labor to install
the replacement vat will be covered by Ultrafryer Systems for vats, which fail within twelve (12) months from the date of
initial start up. Labor for vat replacements after the first year is the responsibility of the owner (2) Vats that fail within the
sixth through eight year will be exchanged at 50% of current selling price of said vat FOB San Antonio. (3) Vats that fail
within the ninth through tenth year will be exchanged at 70% of the current selling price of said vat FOB San Antonio.
(
Example
: If the current selling price for a particular vat is $2,000.00, then a failure during the sixth through eighth year
would be exchanged for $1,000.00; if the failure occurred in the ninth or tenth year it would be exchanged for $1,400.00.)
Proper credit issue for vat failures is contingent upon receipt, by Ultrafryer Systems, of the serial number identification
tag for any failed vat.
ULTRAFRYER PARTS –
All parts on the Ultrafryer® are covered for a period of one (1) year from the initial date
of start up. This is to include gas valves, switches, thermostats, etc. Ultrafryer Systems reserves the right to charge for
certain parts such as computers, filter pumps and motors or any item over the amount of $100.00 until Ultrafryer Systems
receives the defective part back
.
After inspection, credit for the part will
be issued to the purchaser provided the
part is deemed defective and that defect is not the result of neglect or abuse by the user
. The shortening filtration
system, (hoses) are warranted for ninety (90) days from the initial date of start up.
PROCESSING WARRANTY CLAIMS –
The equipment owner must promptly notify Ultrafryer Systems Warranty
Department of any alleged defects as soon as they are discovered by calling 1-800-525-8130. After such notice, the
Warranty Department will perform its obligation under this warranty within a commercially reasonable period of time. If
alleged defects develop after normal business hours, on weekends or on holidays the owner must call Ultrafryer Systems
first at the above number. This number is monitored 24 hours a day, 7 days a week. Ultrafryer Systems will notify an
authorized service agent to make repairs during normal hours or after hours. Any parts that need to be shipped back to
Ultrafryer Systems will be shipped back
prepaid by the customer
marked with the processing number and to the
atten-
tion of the WARRANTY DEPARTMENT.
NON WARRANTY COVERAGE –
This warranty does not include coverage for any consequential cost of damages
including, but not limited to, any loss in store sales, spoiled food products, transportation, duty or custom cost. This
warranty does not cover the Ultrafryer® exported to countries outside the United States and its territories. This warranty
does not cover original installation and adjustments such as leveling, calibrations and electrical and gas connections. This
warranty does not cover travel over 100 miles or 2 hours driving time from the location of the Ultrafryer® or overtime
or holiday charges unless the Warranty Department granted prior approval. This warranty does not cover damage due
to misuse, abuse, alteration or accident. This Warranty does not cover improper or unauthorized repair or installation,
damage in shipment, normal maintenance items such as gaskets, hoses, and exterior finishes. Ultrafryer Systems will
begin the fryer warranty one week after shipment but will adjust the warranty upon receiving approved documentation.
We reserve the right to void component part warranty on any Ultrafryer that is stored more than six (6) months after ship-
ment from Ultrafryer Systems and not put into service.
LABOR COVERAGE –
The cost for labor to replace parts are covered for one (1) year after the initial start up.
The
Warranty Department must be promptly notified of any defects within the first year of operation
.
The labor war-
ranty does not include the cost to repair or clear dirty
filter systems or perform any adjustments that would normally fall
under the tasks associated with a proper start up and/or demonstration.
Labor is covered by Ultrafryer Systems for
repairs by an AUTHORIZED service agent
. Owner is responsible for all costs associated with fryer installation and
start up unless prior arrangements have been made with Ultrafryer Systems.
DISCLAMIER OF WARRANTIES
Other than as stated herein, ULTRAFRYER SYSTEMS makes no warranty of any kind, express or implied, including
but not limited to any warranty of merchantability of fitness for a particular purpose, including trade usage. Ultrafryer
Systems’ sole obligation, and purchaser’s sole remedy, under this warranty is repair or replacement, at the discretion of
Ultrafryer Systems, of any part or component that proves to be defective in materials or workmanship. In no event shall
Ultrafryer Systems be liable for consequential, incidental, or special loss or damages arising from the use of, or inability
to use, the ULTRAFRYER
®
. This limited warranty is the only and complete statement with respect to warranties of NEW
Ultrafryer
®
PAR-3 Gas ULTRAFRYERS
®
sold after June 1
st
, 2000. There are no other documents or oral statements for
which Ultrafryer Systems will be responsible. Effective 3-1-2008.
PDF compression, OCR, web optimization using a watermarked evaluation copy of CVISION PDFCompressor