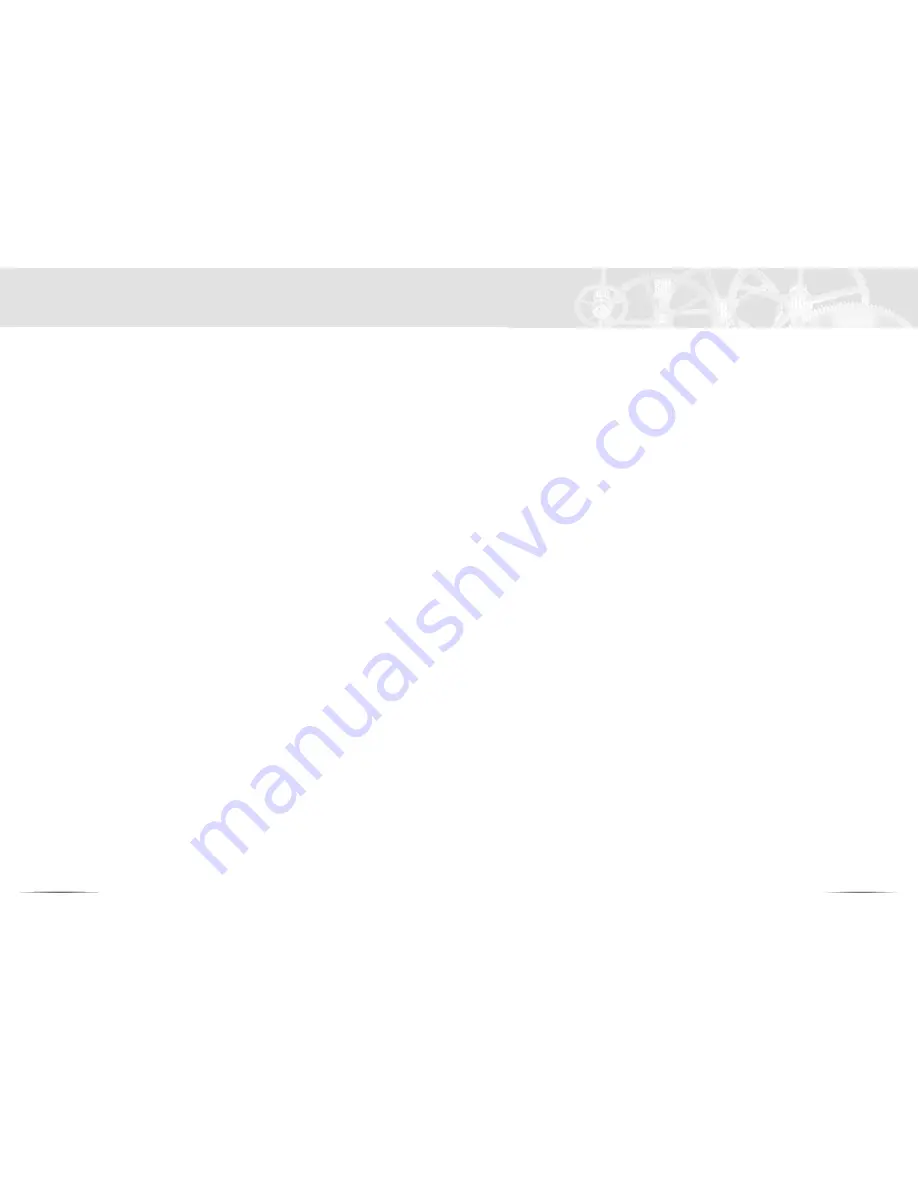
Technology and Function
of the Mechanica M
2
66
67
Abraham-Louis Breguet
*
empirically developed the balance spring
*
named for him in 1795. The Breguet balance spring has a bent
up Terminal curve
*
that is also turned inward. It was later precisely
calculated by Eduoard Phillips
*
. Through the asymmetrical
deformation of the conventional flat hairspring, the contact points of
the bearings with the pivots create additional friction
*
energy that
disturbs the oscillating system—affecting it anisochronously. The
Phillips Terminal curve, on the other hand, makes for symmetrical
(concentric), and thus even, »breathing« of the balance spring, but
does need more height than a simple flat hairspring.
Rate precision has always been strongly dependent upon
temperature change. Metal alloys normally expand through heat,
though the inner stability is reduced, and the material becomes softer
and the spring loses elasticity. This phenomenon results in a change
in frequency for the oscillating system since the balance
*
increases in
inertia through the expansion and the balance spring becomes softer
and less elastic. In a word, the isochronism
*
is lost. Thus, the balance
spring is greatly dependent upon the temperature surrounding it.
In 1896, Swiss physicist and later Nobel Prize winner Charles-Edouard
Guillaume
*
invented an iron-nickel alloy with an especially small
thermal expansion coefficient and increasing elasticity with increasing
temperature, which he called
INVAR
*
(
invar
iable). Invar, however,
had a deceptive element: the high inner tensions of the metal
structure. Only through elaborate tempering
*
(heat treatment) can
the desired constant temperature behavior be achieved. Invar alloys
are used everywhere where the highest value is placed on stable
material characteristics during temperature deviation. Invar is still
today the base material for most balance springs and pendulum rods
in precision timepieces.
In 1931, Swiss countryman Dr. Reinhard Straumann
*
further
developed Invar, making it one of seven elements comprising an
unbreakable, self-compensating, rust-free and antimagnetic alloy.
This alloy, however, demands a special cold deformation before
undergoing a lavish heat treatment. It was given the (today) well-
known name
NIVAROX
*
(
ni
cht
var
iable und
ox
ydfest/ »not variable
and oxide-proof«) and registered for a patent. This is the material
that the balance spring of your Mechanica M2 is made of.
Beside Invar, another material for the manufacture of monometallic
balance and escapement components as well as balance springs has
become commonplace:
GLUCYDUR
*
. The name is made up of the
French words
gluci
nium (meaning »beryllium«) and
dur
(»hard«).
Glucydur is a very hard alloy comprising copper and 2-3 percent
beryllium. It is non-magnetic, not oxidizing and has a very low
thermal expansion. This alloy is also known as beryllium copper and
is often used for highly stressed springs and relay contact material
and for railroads (current collectors). A decisive disadvantage is that
the alloy element beryllium is highly poisonous. When working
beryllium copper, one therefore needs to be very careful.
The manufacture of high-quality balance springs begins with the
precise combination of all pure materials for the melting mixture. In
a vacuum space, these are poured into a raw cast block of about 20
cm diameter and 80 kg in weight from which is created a highly
precise wire with a diameter of only 0.075 mm—thus thinner than a
human hair—over the course of numerous individual operations like
extrusion molding, warm and cold rolling, and forming by machines
using diamond stretching stones. The precise, round wire is then
rolled out to create the flat reel used for balance springs in an
air-conditioned room at an incredible precision of 0.1 thousandths of
a millimeter (1/10 micron).
The rolled strip only a few tenths of a millimeter wide and a few
hundredths of a millimeter thick are cut to the appropriate lengths
and rolled out on an arbor before being subjected to warming
treatment of about 700°C in a vacuum or a protective gas atmos-
phere. This allows the springs to take on the desired spiral shape and
at the same time receive the necessary hardness and elasticity
(thermoelastic coefficient) by creating an emulsive process in the
alloy. The quality of balance springs are judged by their temperature
coefficient, or the dependence of the elasticity on temperature.