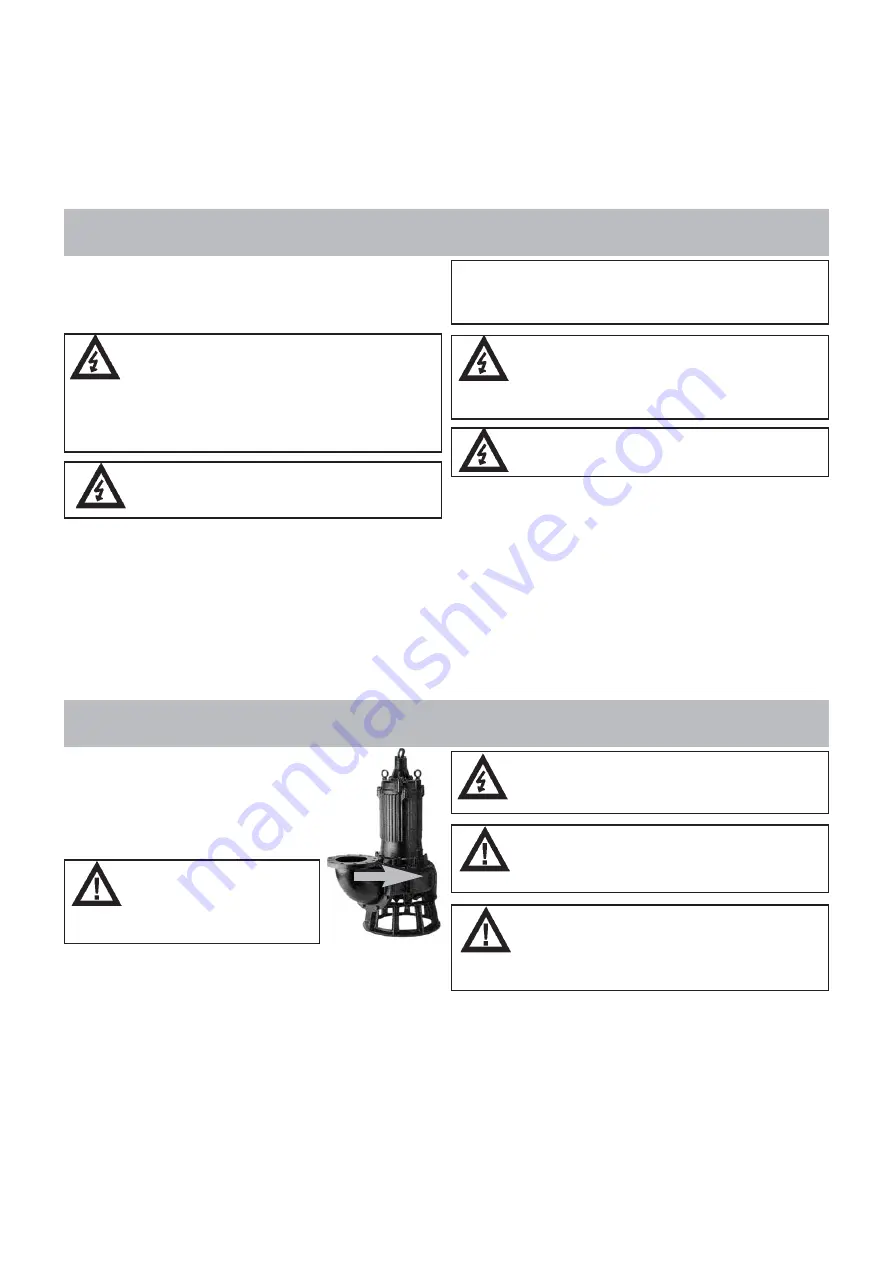
The pump must be connected to terminals or starting equipment installed at a
level which cannot be flooded.
All electrical work must be carried out by an authorized electrician.
Only open the motor at a workshop. All measurements must be made at the free
end of the cable.
Check that the nameplate of the pump to verify that its voltage and frequency are
correct.
Power supply variation must be within ±1Hz (frequency) and ±5% (voltage) of
rated values. Check that the thermal overload relays has been set to the pump’s
rated ampere draw.
Electrical Connections
CAUTION!
The electrical installations must conform to national and local
regulations.
Connection of starter and motor conductors
If electrical connection of the pump is found to be difficult, contact your
Tsurumi dealer. To enable the correct connections, the number of
conductors, any monitoring equipment and the method of starting must be
known.
CAUTION!
All electrical equipment must always be earthed (grounded).
this applies both to the pump and to any monitoring equipment.
Improper wiring can lead to current leakage, electrical shock or fire.
Be sure to use a ground leakage breaker and an overcurrent protector (or
breaker) to prevent damage to the pump that may lead to electrical shock.
Imperfect grounding can cause the pump to be put out of operation by
electro-galvanic corrosion very quickly.
CAUTION!
Before connecting the cabtyre cable to the terminal board,
make sure that the power supply (i.e. circuit breaker) is
properly disconnected. Failure to do so may lead to electrical
shock, short, or injury caused by the unintended starting of the pump.
Cabtyre cable
If one or more extension cables are used, they may need to be of larger section
than the pump cable, according to length and possible other loads. A cable of
insufficient section results in loss of voltage and hence overheating of motor and
cable, which may lead to repeated motor stoppage, unreliability, shortcircuit, fire,
current leakage and electric shock. So does a damaged or unsecurely wired
cable, the more so if it is submerged. No attempt should be made to replace or
splice the pump cable, or open the motor, outside of a suitably manned workshop.
Always protect the cable against pulling, crushing grazing and kinking, as the
copper conductors are fragile and must remain insulated to avoid lack of voltage,
shortcircuiting or electric shock. Apply no load to a cable that is lying in a roll, as
a peak voltage can result, high enough to burn through the insulation.
NOTE!
If a plug and socket are used, the grounding lead should be longer than the
phases to ensure that the other leads will, in case of a strong pull, be torn
first.
Operation
Before Starting:
Check that all persons concerned agree that all
verifications have been completed. Check that all bolts
are tight and the pump´s weight is supported, the
discharge conduit has been connected up, nobody is
touching the water nor is unnecessarily near the
conduit or switchgear. Be prepared to stop at once.
CAUTION!
The starting jerk may be violent.
Don´t hold the pump handle when
checking the direction of rotation.
Make sure that the pump is firmly supported and
cannot rotate.
CAUTION!
Reversal of the direction of rotation on a plug that has no
phase transposing device may be done only by an authorized
person.
CAUTION!
If the built-in motor protection has tripped, the pump will stop
but will restart automatically when it has cooled down.
NEVER open the motor to make measurements, this can be
done at the free end of the cable.
3
CAUTION!
If a cable is damaged, it must always be replaced.
WARNING!
Never insert your hand or any other object into the inlet
opening on the underside of the pump casing when the pump
is connected to the power supply.
Before inspecting the pump casing, check that the pump has been isolated
from the power supply and cannot be energized.
Cable:
The pumps need to have their cable kept tight enough to prevent it from being
drawn into the pump inlet and cut. Voltage should not be applied to the cable as
long as it is not unrolled, as a voltage peak might occur that pierces the insulation.
If the power cable and level control cables are to go through concrete or earth,
they need to be long enough to allow the pump to be lifted onto a floor for
inspection. A conduit needs to be installed to pass the cables through, because
the power cable may not be removed from the motor to take away the entire pump
to a workshop, and the cable may need replacement.
The cable and its possible watertight connection and extension cable must reach
to a level beyond reach of flooding!
An electrician can extend a cable and make the splice waterproof, if he is
experienced in this, has the proper 3M or equivalent kit, and makes a 24-hour
immersion test (keeping the end out of the water and checking for at least 20 M
Ohm insulation); replacement of the cable, in a workshop only, is always
preferable. Voltage loss due to under-rated cabling between power source and
pump, is by far the most common cause of stopping during operation.
Notice: Keep strictly to these instruction otherwise the motor might burn
out!
The pump will jerk anti-clockwise when viewed from above, indicating that it is
running clockwise. If not, two of the three phases U, V, W should be transposed
with care by an electrician at the point of connection of pump cable to starter.
In the case of star delta please ask your Tsurumi dealer.
For connecting the cables correctly to the terminal board please
keep to the diagramm indicated in the table in the appendix