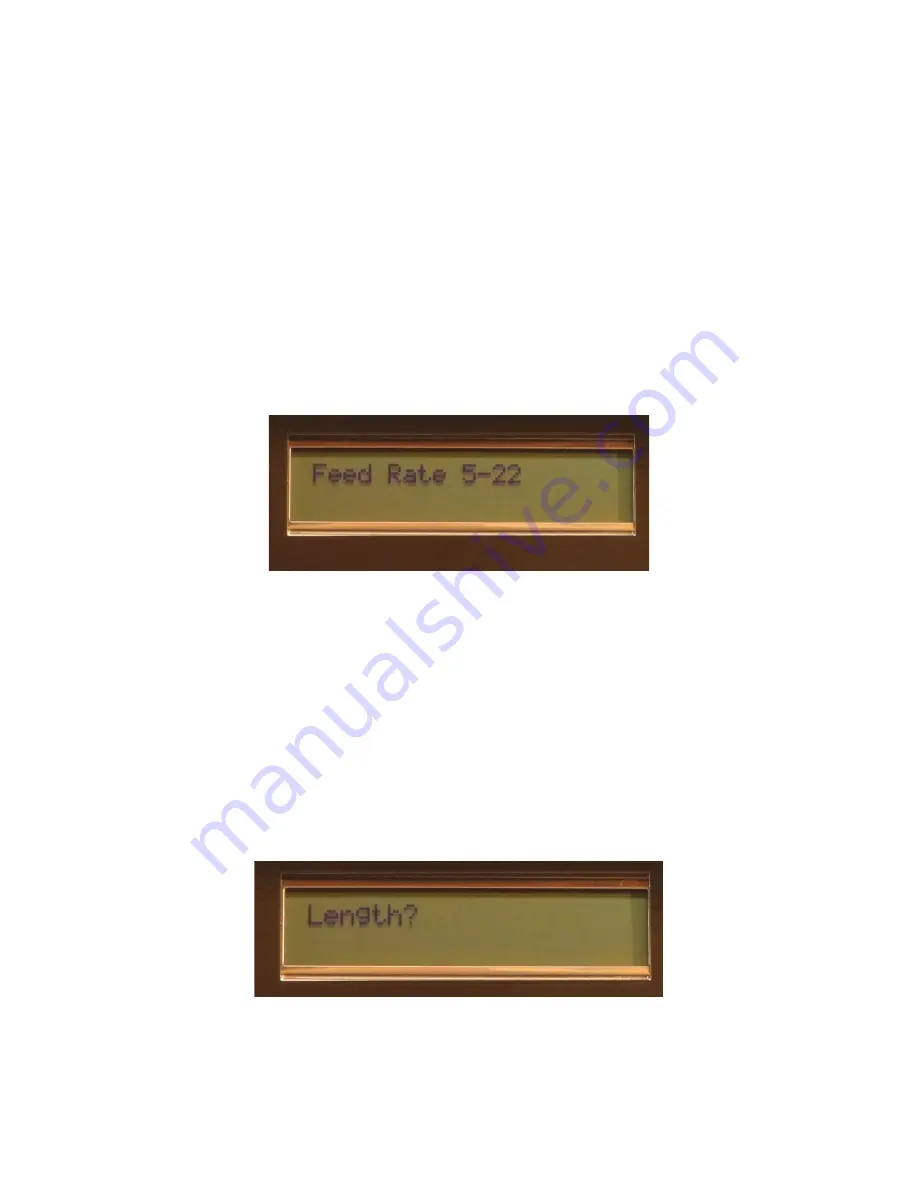
10
Keyboard Commands
FEED JOG Allows you to manually operate the feed rollers
KNIFE JOG Allows you to manually operate the knife
RE-SET Allows you to clear the machine and start a new program
STOP Allows you to stop the machine and save all data in the memory. The STOP function
Also allows you to clear a data entry while programming
–
for example, if an incorrect value
was entered for length or cut time.
ENTER Allows you to enter program data
Entering A program
Feed Rate
Figure 3
When the control panel is turned on the loading screen and version number will be displayed.
The next series of prompts will be cut settings. The first prompt will be for feed rate. "FEED RATE
5-22 " (figure 3) will appear on the LCD. This will determine how fast the material will feed
through the machine, in inches. While our machines can feed up to 22 inches per second, the
speed required to run the machine successfully will largely be determined by the material
being cut. We recommend starting somewhere in the middle and working up if necessary.
Older machines may not have variable speed, in which case this prompt will be omitted. Type
in the desired speed and press ENTER.
Length
Figure 4
Содержание 1000 4.5 Hot cutter
Страница 1: ...Service Manual for 1000 Series Strip cutters Rev 1 1 6 6 22 ...
Страница 53: ......
Страница 54: ......
Страница 55: ......
Страница 56: ......
Страница 57: ......
Страница 58: ......
Страница 59: ......
Страница 66: ...Drive Transistor Test ...