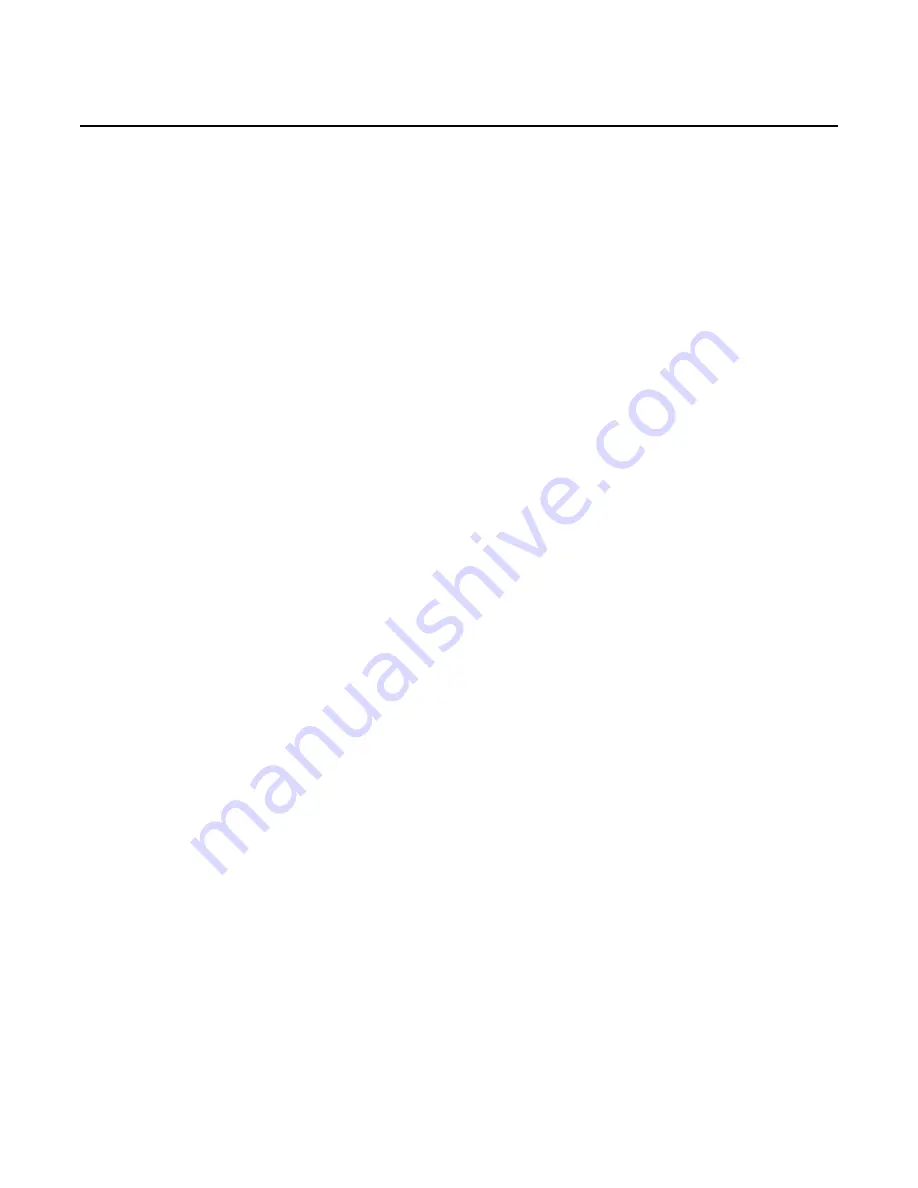
RT-SVX25C-EN
51
Troubleshooting
Note:
Before resetting Cooling Failures and Heating Lockouts check the Failure Status Diagnostics
by the methods previously explained. Diagnostics will be lost when the power to the unit
is disconnected.
Method 1
To reset the system from the space, turn the “Mode” selection switch at the zone sensor to the “Off”
position. After approximately 30 seconds, turn the “Mode” selection switch to the desired mode,
i.e. Heat, Cool or Auto.
Method 2
To reset the system at the unit, cycle the unit power by turning the disconnect switch “Off” and then
“On”.
Lockouts can be cleared through the building management system. Refer to the building
management system instructions for more information.
Zone Temperature Sensor (ZTS) Service Indicator
The ZSM SERVICE LED is a generic indicator, that will signal the closing of a Normally Open switch
at any time, providing the Indoor Motor (IDM) is operating.
This indicator is usually used to indicate a clogged filter, or an air side fan failure.
The RTRM will ignore the closing of this Normally Open switch for 2 (±1) minutes. This helps
prevent nuisance SERVICE LED indications. The exception is the LED will flash 40 seconds after the
fan is turned “On” if the Fan Proving Switch is not made.
Clogged Filter Switch
This LED will remain lit the entire time that the Normally Open switch is closed. The LED will be
turned off immediately after resetting the switch (to the Normally Open position), or any time that
the IDM is turned “Off”.
If the switch remains closed, and the IDM is turned “On”, the SERVICE LED will be turned “On” again
after the 2 (±1) minute ignore delay.
This LED being turned “On”, will have no other affect on unit operation. It is an indicator only.
Fan Failure Switch
When the “Fan Failure” switch is wired to the RTOM, the LED will remain flashing the entire time
the fan proving switch is closed, indicating a fan failure, and it will shut the unit operations down.
Zone Temperature Sensor (ZTS) Test
Note:
These procedures are not for programmable or digital models and are conducted with the
Zone Sensor Module electrically removed from the system.
Test 1
Zone Temperature Thermistor (ZTEMP)
This component is tested by measuring the resistance between terminals 1 and 2 on the Zone
Temperature Sensor. Below are some typical indoor temperatures, and corresponding resistive
values.
Содержание TC*150-301
Страница 13: ...RT SVX25C EN 13 Unit Dimensions Figure 1 WITHOUT ECONOMIZER 5 8 WITH ECONOMIZER 5 0 ...
Страница 30: ...30 RT SVX25C EN Installation Figure 17 5 HVAC units 10 HVAC units ...
Страница 31: ...RT SVX25C EN 31 Installation Figure 18 Typical field wiring diagrams for optional controls ReliaTel only ...
Страница 61: ......
Страница 62: ......