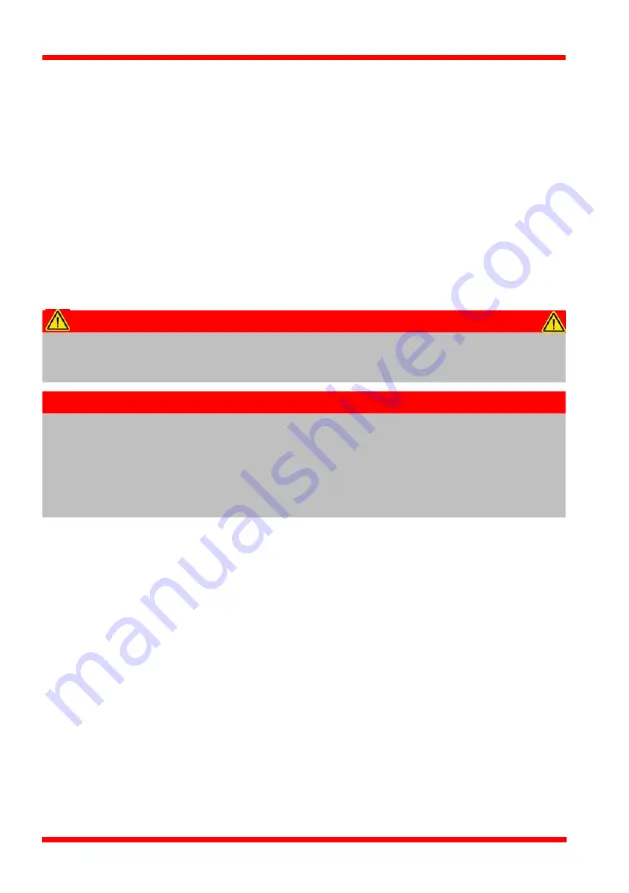
44
HA0378T Rev C Feb 2019
Chapter 5
Loop Tuning
- When operating in Closed Loop mode, the proportional, integral and
differential (PID) constants can be used to fine tune the behaviour of the feedback
loop to changes in the output position. While closed loop operation allows more
precise control of the position, feedback loops need to be adjusted to suit the different
types of device that can be mounted on the stage. Due to the wide range of devices
that can be used with the LPS710 and their different masses, some loop tuning may
be necessary to optimize the response of the system and to avoid instability. The
default parameters have been set for stable operation with a 30g load.
These slider controls adjust the settings for the PID parameters, and any changes are
applied immediately after clicking the Set button. In this way, the window can be left
open and adjustments made whilst observing the effect on the system.
Once satisfactory performance is obtained, click OK to save the settings, or cancel to
discard the changes. Click OK to close the window.
Prop
- The Proportional parameter makes a change to the output which is
proportional to the current error value. A high proportional gain results in a large
change in the output for a given error. If set too high, the system can become
unstable.
It accepts values in the range 0 to 10000 (default 0).
Int
- The Integral parameter accelerates the process towards the demanded set
point value, ensuring that the positional error is eventually reduced to zero. If set
too high, the output can overshoot the demand value.
It accepts values in the range 0 to 10000. (default 790).
Deriv
- The Derivative parameter damps the rate of change of the output, thereby
decreasing the overshoot which may be caused by the integral term. However, the
differential term also slows down system response. If set too high, it could lead to
instability due to signal noise amplification.
It accepts values in the range 0 to 10000 (default 0).
Warning
High amplitude oscillation due to inappropriate PID/Notch filter parameter
settings can cause damage to the piezo stage. If such oscillation is apparent,
switch immediately to open loop or disable the stage.
Note
The default values have been optimised for a 30g load and to work with the
LPS710 stage shipped with the controller.
Due to the type of load the LPS710 presents to the PPC001 controller, the
system is most sensitive to the integral (Int) tuning parameter and the
notch filter settings. In most applications the deriviative parameters can
be left at their default values.