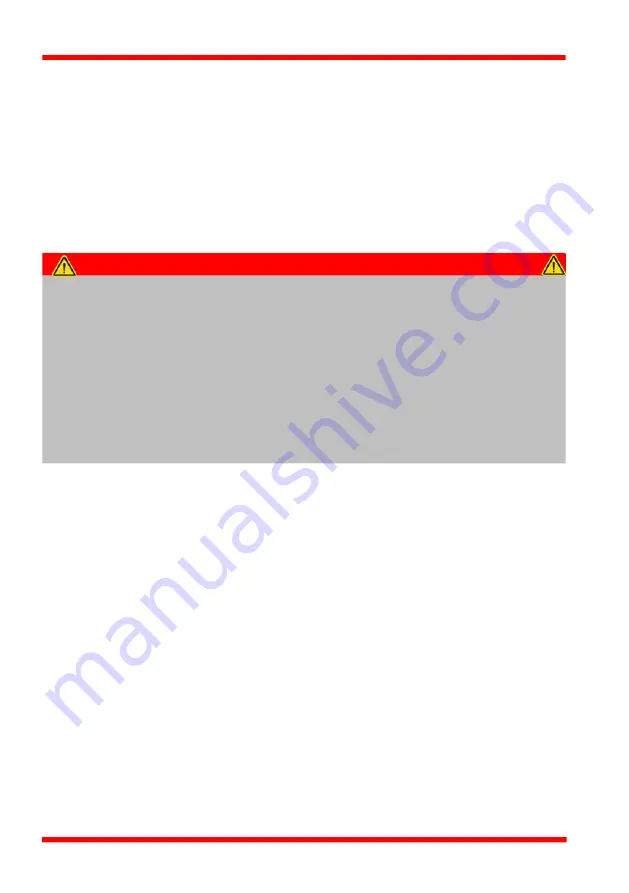
42
HA0378T Rev C Feb 2019
Chapter 5
Drive Input Source
- determines the input source(s) which control the output from the
HV amplifier circuit (i.e. the drive to the piezo actuators).
SW Only - the unit responds only to software inputs and the piezo drive output is
that set using the SetVoltOutput method (or the GUI panel ‘Output’ control).
BNC (+ SW) - the unit sums the signal on the rear panel EXT IN BNC connector with
the voltage set using the SetVoltOutput method (or the GUI panel ‘Output’ control).
Joystick (+ SW) - the unit sums the signal from the joystick control with the voltage
set using the SetVoltOutput method (or the GUI panel ‘Output’ control).
Jo BNC (+ SW) - the unit sums all three signals signal.
Feedback Source
- the type of feedback associated with the actuator being driven,
either Capacitive or Strain Gauge. The LPS710 piezo stage has a capacitive sensor
and this parameter is locked.
Monitor BNC
- the EXT OUT BNC connector on the rear panel can be used to monitor
the piezo actuator on an external device, e.g. oscilloscope. This can be a useful
means of monitoring the position stability and fine tuning the settings.
Output Signal
- the signal being monitored, Drive Voltage, Unprocessed Position
or Linearised Position - see also Section 3.9.
If
Drive Voltage
is selected, the signal driving the EXT OUT (Monitor) BNC is
a scaled down version of the piezo output voltage, with 150 V piezo voltage
corresponding to 10V.
If
Unprocessed Position
is selected, the signal driving the EXT OUT (Monitor)
BNC is the output voltage of the position demodulator. This signal shows a
slight nonlinearity as a function of position and a small offset voltage. As a
result it is not as accurate as the linearized position. However, having not
undergone any digital processing it is free of any potential digital signal
processing effects and can be more advantageous for loop tuning and
transient response measurement.
If
Linearized Position
is selected, the signal driving EXT OUT is linearized and
scaled so that the 0 to full range (800 µm) corresponds to 0 to 10 Volts.
Caution
When driving the piezo stage from an external input source, the external
signal is summed with the software input (GUI panel or SetVoltOP
software method) and, if connected and selected, the Joystick.
In closed loop a smaller drive voltage than 150V is required to give
800 µm travel. However, in open loop the drive voltage can be set from
-25 V to 150 V with a typical travel of over 1100 µm. When using an
external source and switching from open loop to closed loop, care must
be taken that the travel range is not pushed to its limit. If closed loop is
selected with excessive drive voltages applied, the stage may jump
position and/or drift.
If absolute positioning is required use closed loop mode only