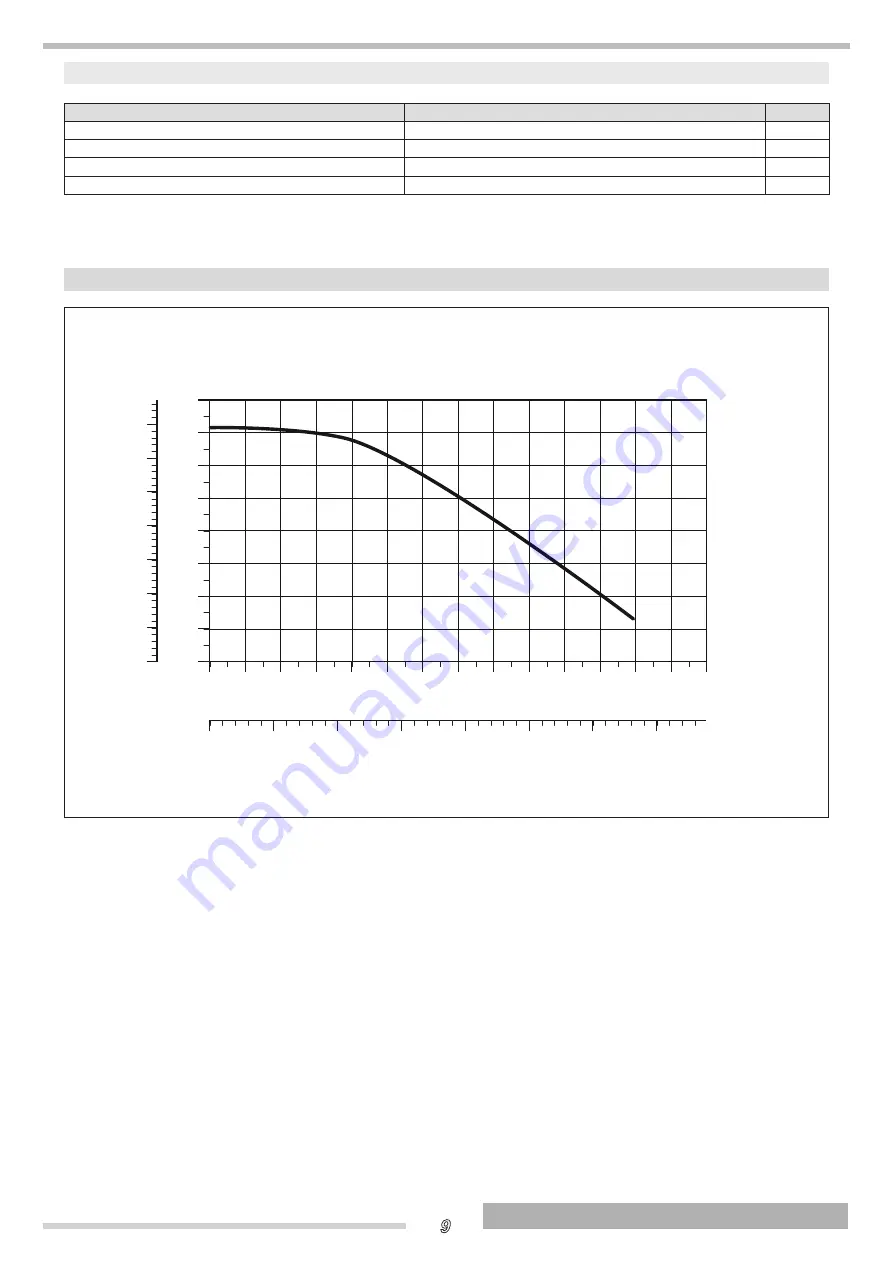
9
ENGLISH
Pump
DESCRIPTION
ACQUAHOME R BLU
Electrical consumption
52
W
EEI Part 3 (*)
≤ 0,20
P L,Avg (**)
≤ 23
W
Minimum pressure at pump suction inlet
0,5
bar
(*)
Energy efficiency rating according to regulations 641/2009-622/2012
(**)
Approximate average annual electricity consumption according to regulations 641/2009-622/2012
PUMP CURVES
Residual head [m] - [kPa]
Q [m³/h]
0
1
2
3
4
5
6
7
[m]
H
0
10
20
30
40
50
60
70
[kPa]
p
0,0
0,1
0,2
0,3
0,4
0,5
0,6
0,7
Q [l/s]
0,0 0,2 0,4 0,6 0,8 1,0 1,2 1,4 1,6 1,8
2,0 2,2 2,4 2,6 2,8
Flow-rate [m
3
/h] - [l/s]
The curves refer to a density of 983.2 Kg/m
3
, a water temperature of +20°C and a kinematic viscosity of 0.474 mm
2
/s (0.474 cSt).