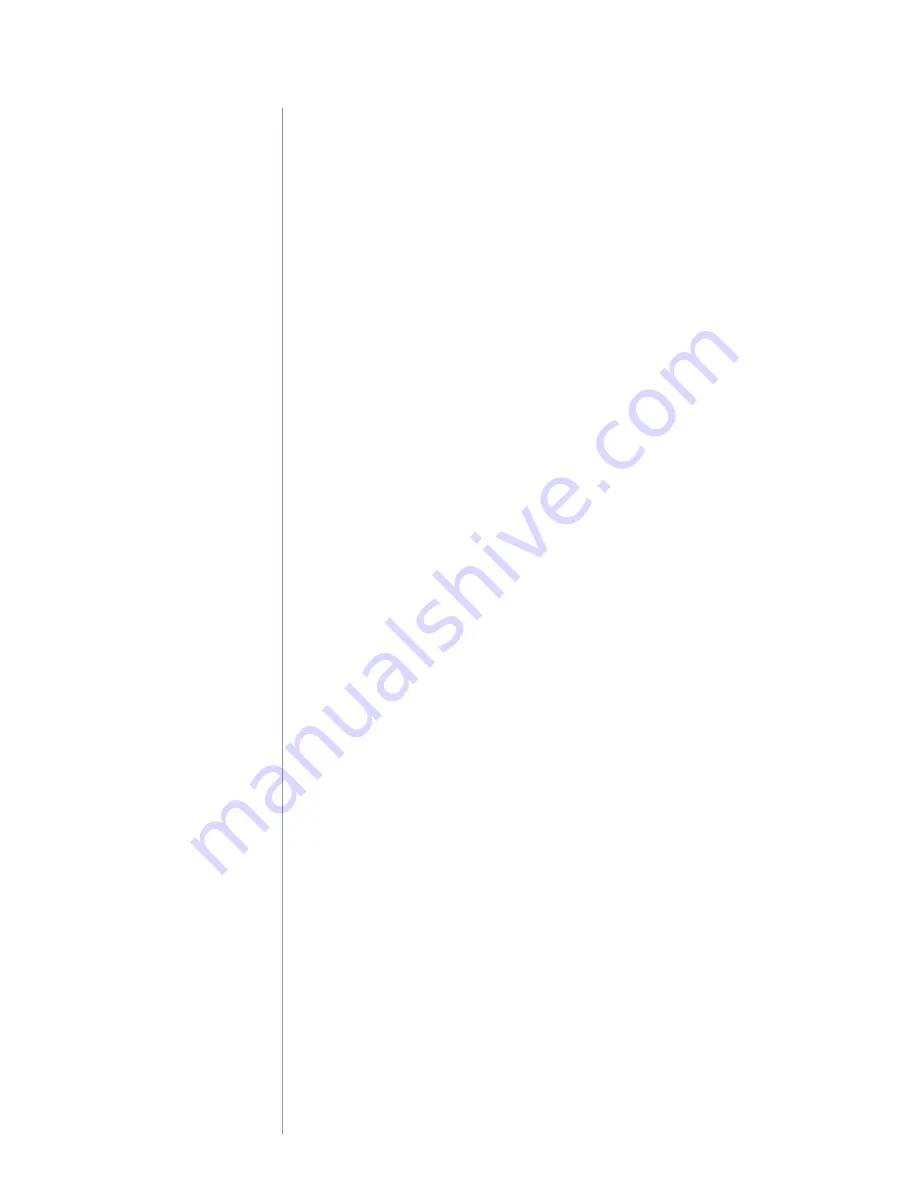
©2004 TESA Switzerland All Rights Reserved.
Page 3-14
User's Manual
MH3D
Measuring With a Ball Probe
Qualifying Probes
All probes must be qualified before accurate measurements can be made.
There are two primary purposes for this:
• To calculate the effective tip diameter.
• To learn the location of the center of the probe tip in the measuring
volume. This is important to obtain properly compensated data when the
positional feedback is filtered through the error map.
Before qualifying a probe,
• Verify that the proper probe type is selected in the software.
• Verify the probe shaft diameter for your machine.
• Verify the reference offsets for your probe.
• Verify that the qualification or reference sphere diameter is correct within
the software configuration.
Refer to your software manual for a detailed description of the probe calibration
process.
To measure with a ball probe, firmly hold the Z-rail and gently make contact
with the surface of the part with the ball probe. Be sure there are no vibrations or
bouncing and that the probe has come completely to rest against the part. To
measure a point with a hard ball probe, bring the probe into contact with the part
surface and press the “Scan” (left) button on the ZMouse or the right hand
button on the desk mouse.
The measurement software continually monitors the measuring direction or
“sense” and automatically corrects or “compensates” for the probe radius.
The measurement software also continually monitors the location of the meas-
urement point within the measuring volume. The “approach” vector, or the
vector created from the last monitored point to the first measurement point, is of
critical importance for all features. For planar surfaces, the approach vector is
used in the calculation of the positive direction of the feature’s vector. The
approach vector should be as perpendicular to the feature’s surface as possible.
After the first point is taken, it is OK to slide the probe on the feature’s surface
between taking points.
Содержание MH3D
Страница 1: ...User s Manual MH3D 2004 TESA Switzerland All Rights Reserved Page 0 1 U S E R S M A N U A L English ...
Страница 2: ... 2004 TESA Switzerland All Rights Reserved Page 0 2 User s Manual MH3D ...
Страница 6: ... 2004 TESA Switzerland All Rights Reserved Page 1 2 User s Manual MH3D ...
Страница 17: ...User s Manual MH3D 2004 TESA Switzerland All Rights Reserved Page 2 1 CHAPTER 2 Construction Construction ...
Страница 18: ... 2004 TESA Switzerland All Rights Reserved Page 2 2 User s Manual MH3D ...
Страница 34: ... 2004 TESA Switzerland All Rights Reserved Page 2 18 User s Manual MH3D Cables Power supply Printer ...
Страница 35: ...User s Manual MH3D 2004 TESA Switzerland All Rights Reserved Page 3 1 CHAPTER 3 Operation Operation ...
Страница 36: ... 2004 TESA Switzerland All Rights Reserved Page 3 2 User s Manual MH3D ...
Страница 53: ...User s Manual MH3D 2004 TESA Switzerland All Rights Reserved Page 3 19 ...
Страница 54: ... 2004 TESA Switzerland All Rights Reserved Page 3 20 User s Manual MH3D Useful Probe Dimensions TESASTAR_i ...
Страница 56: ... 2004 TESA Switzerland All Rights Reserved Page 3 22 User s Manual MH3D MH3D Notes ...
Страница 57: ...Page 4 1 2004 TESA Switzerland All Rights Reserved User s Manual MH3D CHAPTER 4 Maintenance Maintenance ...
Страница 58: ...Page 4 2 2004 TESA Switzerland All Rights Reserved User s Manual MH3D ...
Страница 69: ...User s Manual MH3D 2004 TESA Switzerland All Rights Reserved Page 5 1 CHAPTER 5 Glossary Glossary ...
Страница 70: ... 2004 TESA Switzerland All Rights Reserved Page 5 2 User s Manual MH3D ...
Страница 92: ... 2004 TESA Switzerland All Rights Reserved Page 5 24 User s Manual MH3D MH3D Notes ...
Страница 93: ...User s Manual MH3D 2004 TESA Switzerland All Rights Reserved Page A 1 CHAPTER A Appendix Appendix ...
Страница 94: ... 2004 TESA Switzerland All Rights Reserved Page A 2 User s Manual MH3D ...