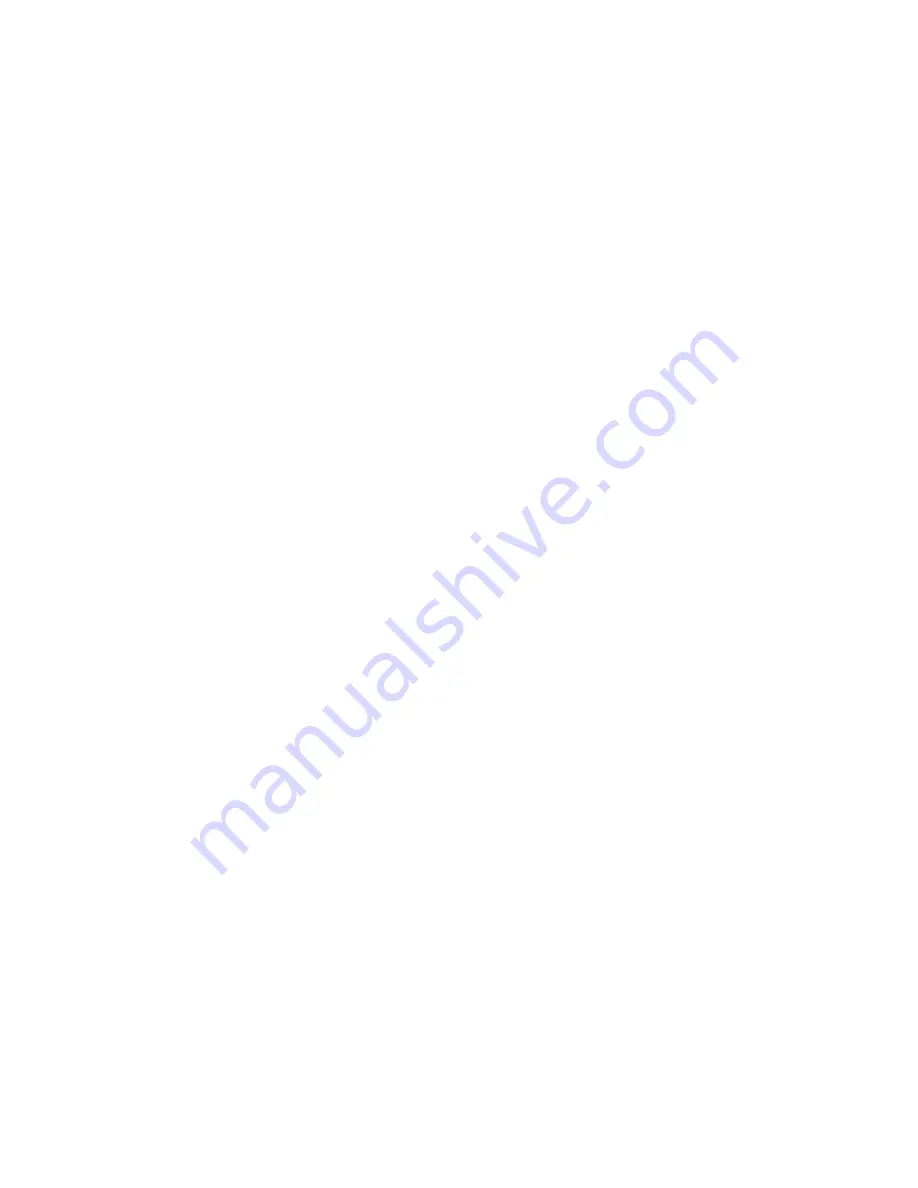
19-12
maintenance the oil suction tube screen must be cleaned and all lower internal hardware
inspected for security and safetying. Oil sumps that are warped or cracked must be
discarded.
19-5
LUBRICATION SYSTEM MAINTENANCE (continued)
Oil Suction Tube
- The oil sump and accessory case must be removed to gain access to
the oil suction tube. If oil suction tube access is required, see the applicable portions of oil
sump/accessory case in accordance with the applicable disassembly/reassembly in the
L/TSIO-360 Series Overhaul Manual, Form X30596A
Oil Cooler
- The oil cooler or its components may be removed for replacement and repair
in accordance with the applicable portions of oil cooler disassembly/reassembly
instructions in the L/TSIO-360 Series Overhaul Manual, Form OH-08..
Oil Pressure Relief Valve
- Cut safety wire, remove the oil pressure relief valve and
inspect the plunger for scoring, nicks, and the conical face for roughening. Inspect oil
pressure relief valve limits in accordance with Section 19-5. Oil pressure relief valves with
scoring, nicks, roughening of the conical face or that exceed the specified limits must be
discarded and replaced with new.
Inspect the oil pressure relief valve seat for scoring, nicks or roughening. Seats with these
indications must be refaced. Using an Oil Pressure Relief Spot Facer as shown in
Chapter 2," Tools," reface the pressure relief valve seat in the oil pump housing.
CAUTION. . . Reface pressure relief valve seat using light finger pressure when turning
refacing tool.
After the refacing procedure, the depth from the top of the oil pump housing to the seat
face must not exceed the specified limit item (2) in Figure 19-8," Lubrication System
Service Limits." Accessory cases with oil pressure relief valve housings that exceed
specified limits must be discarded.
CAUTION. . . Thoroughly clean oil pressure relief valve cavity after refacing procedure. All
debris from the refacing procedure must be removed.
Reassemble serviceable or new relief valve housing and adjusting screw. Turn adjusting
screw into housing about halfway. Install new copper washer and nut. Assemble plunger,
spring, washer and slide into housing. Coat housing threads with TCM anti-seize
lubricant. insure relief valve components are aligned and install in oil pump housing.
Torque housing to 240-260 inch pounds. Safety wire oil pressure relief valve housing in
accordance with Section 9-2," Lockwire Procedure." The engine oil pressure must be
adjusted prior to release for return to service in accordance with Section 23-2, "Oil
Pressure Adjustment."
Oil Temperature Control Valve
- Remove the oil temperature control valve and inspect
the valve seat for scoring, nicks, roughness or deterioration. Inspect oil temperature
control valve limits in accordance with Section 19-5. Oil temperature control valves
exhibiting any of the above indications or that exceed specified limits must be discarded
and replaced with new. Reinstall serviceable or new oil temperature control valve using
new gasket and torque to 440-460 inch pounds. Safety wire oil temperature control valve
housing in accordance with Section 9-2," Lockwire Procedure."
CAUTION. . . When performing dimensional inspection the following "Service Limits" may
be used. However, they are only intended as a guide for re-use when performing
maintenance of the engine prior to major overhaul. Parts with dimensions or fits that
exceed service limits must not be re-used. Parts with values up to and including service
limits may be re-used, however, judgment should be exercised considering the
PROXIMITY of the engine to its recommended overhaul time. Service limits must NOT be
Содержание TSIO-360-RB
Страница 11: ...1 5 FIGURE 1 1 Engine Description L TSIO 360 RB ...
Страница 12: ...1 6 FIGURE 1 2 ENGINE DESCRIPTION L TSIO 360 RB Cont d ...
Страница 13: ...1 7 FIGURE 1 2 ENGINE DESCRIPTION L TSIO 360 RB Cont d ...
Страница 14: ...1 8 FIGURE 1 2 ENGINE DESCRIPTION L TSIO 360 RB Cont d ...
Страница 15: ...1 9 FIGURE 1 2 ENGINE DESCRIPTION L TSIO 360 RB Cont d ...
Страница 25: ...3 1 CHAPTER 3 SEALANTS AND LUBRICANTS Sealants Lubricants 3 2 ...
Страница 32: ...4 2 INTENTIONALLY LEFT BLANK ...
Страница 54: ...6 2 INTENTIONALLY LEFT BLANK ...
Страница 58: ...6 6 FIGURE 6 1 INSTALLATION DRAWING ...
Страница 59: ...6 7 FIGURE 6 1 INSTALLATION DRAWING cont d ...
Страница 60: ...6 8 FIGURE 6 1 INSTALLATION DRAWING cont d ...
Страница 61: ...6 9 FIGURE 6 1 INSTALLATION DRAWING cont d ...
Страница 64: ...6 12 INTENTIONALLY LEFT BLANK ...
Страница 70: ...7 6 INTENTIONALLY LEFT BLANK ...
Страница 82: ...10 2 INTENTIONALLY LEFT BLANK ...
Страница 85: ...11 3 FIGURE 11 1 INDUCTION AND EXHAUST SYSTEM ...
Страница 94: ...11 12 INTENTIONALLY LEFT BLANK ...
Страница 110: ...12 16 INTENTIONALLY LEFT BLANK ...
Страница 124: ...14 4 INTENTIONALLY LEFT BLANK ...
Страница 128: ...15 4 INTENTIONALLY LEFT BLANK ...
Страница 132: ...16 4 INTENTIONALLY LEFT BLANK ...
Страница 139: ...17 7 FIGURE 17 4 STARTER ADAPTER FITS LIMITS ...
Страница 140: ...17 8 INTENTIONALLY LEFT BLANK ...
Страница 143: ...18 3 FIGURE 18 1 ACCESSORY CASE DESCRIPTION ...
Страница 147: ...19 3 FIGURE 19 1 LUBRICATION SYSTEM SCHEMATIC ...
Страница 149: ...19 5 ACCESSORY CASE INTERNAL VIEW TSIO 360 FIGURE 19 2 OIL PUMP DESCRIPTION TSIO 360 ...
Страница 150: ...19 6 ACCESSORY CASE INTERNAL VIEW LTSIO 360 FIGURE 19 3 OIL PUMP DESCRIPTION LTSIO 360 ...
Страница 158: ...19 14 INTENTIONALLY LEFT BLANK ...
Страница 176: ...20 18 FIGURE 20 12 CYLINDER ASSEMBLY SERVICE LIMITS For Maintenance Cylinder Dimensions see next page ...
Страница 181: ...21 3 FIGURE 21 1 CRANKCASE DESCRIPTION ...
Страница 186: ...21 8 INTENTIONALLY LEFT BLANK ...
Страница 194: ...22 8 INTENTIONALLY LEFT BLANK ...
Страница 203: ...23 9 FIGURE 23 6 CONSTANT SPEED SEA LEVEL PERFORMANCE CURVE ...
Страница 204: ...23 10 FIGURE 23 7 FUEL FLOW VS METERED FUEL PRESSURE ...
Страница 205: ...23 11 FIGURE 23 8 FUEL FLOW VS BRAKE HORSEPOWER ...