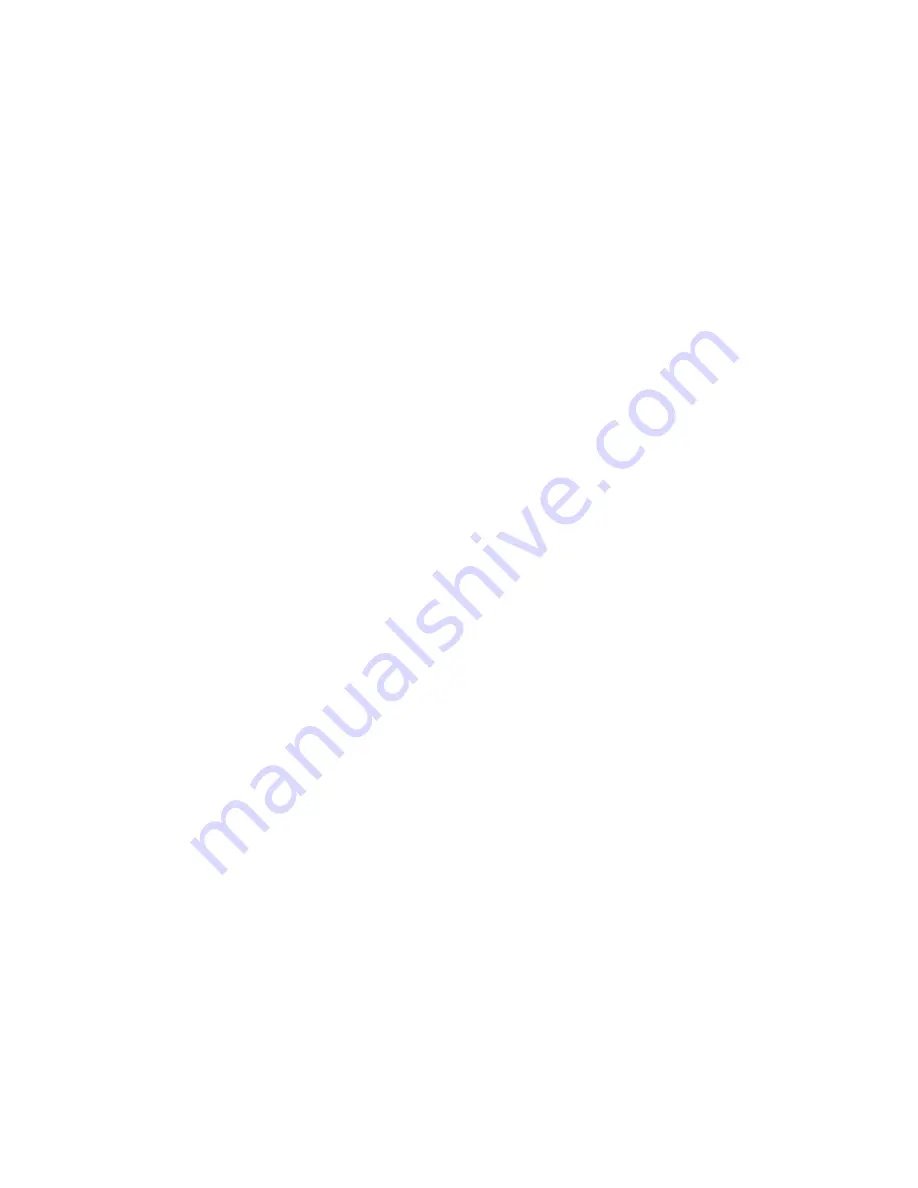
iWorx® VPU2
30
505-010-2, Effective: April 29, 2014
© 2014 Taco Electronic Solutions, Inc.
The P+I control loop is based on the mixed air temperature setpoint and economizer setpoint. As the temperature
increases above the economizer setpoint, the economizer is modulated open. The economizer is modulated closed as
the temperature decreases below the economizer setpoint.
To prevent the integral component from becoming too large, there is anti-wind up reset protection. This protection
clamps the integral value when all of the components add up to more than 100% or less than 0%. The following equa-
tions are used for P+I control:
K
p
=
Proportional Gain
K
i
=
Integral Gain
EconPosition
= (K
p
x
Error
) + I
When the economizer is disabled, it modulates to the minimum position. A configuration parameter is available to
optionally disable the economizer during unoccupied periods.
Dehumidification
The VPU2 can be configured to keep humidity below a given setpoint. If the Setpoint is set to zero, dehumidification is
disabled. When the humidity is above the Setpoint dehumidification begins and stops when the humidity drops below
Setpoint minus 3%.
Dehumidification stops when the reference zones (VAVI) space temperature drops below the heating setpoint minus
the control band offset. Dehumidification is also disabled when the unit is in heating.
During dehumidification, the operating mode will be displayed as “Dehumid,’ the cooling outputs will stage on and the
stage timer is enforced, or modulating output or floating point valve will be set to 100%.
Fan Operation
During Morning Warm-up, Occupied, Extended Occupancy, and Emergency Heating states, the fan runs continuously.
During the shutdown state, the fan is off.
The fan can be overridden from the LCI or another host controller. When the fan is overridden, the static pressure P+I
loop control is disabled and the integral sum is cleared to prevent anti-windup reset. The fan's modulated output can be
overridden between 0 and 100%. If the desired speed is greater than the current speed, the speed is ramped up to the
desired speed based on the
Soft Start Ramp
setting.
Static Pressure Control
Static pressure control is achieved by modulating a variable speed drive based on the measured static pressure in the
supply duct. The static pressure sensor input has maximum range of 5.000"
W.C.
with
a
minimum
resolution
of
0.005"
W.C.
The fan speed output is modulated by a P+I control loop based on the static pressure loop setpoint and the supply
static pressure measurement. The P+I control loop modulates the output to maintain a constant static pressure within
the supply air duct. As the supply static pressure decreases 0.025"
W.C.
below
the
static
pressure
loop
setpoint,
the
output is modulated towards its maximum value. The output is modulated towards its minimum value as the supply
static pressure increases to 0.025"
W.C. above the static pressure loop setpoint. When the static pressure is within
±0.025”
W.C. of the static pressure setpoint, the damper output remains at its current level.
Error
EconSp MixedAirTemp
–
=
I
I
K
i
Error
+
=