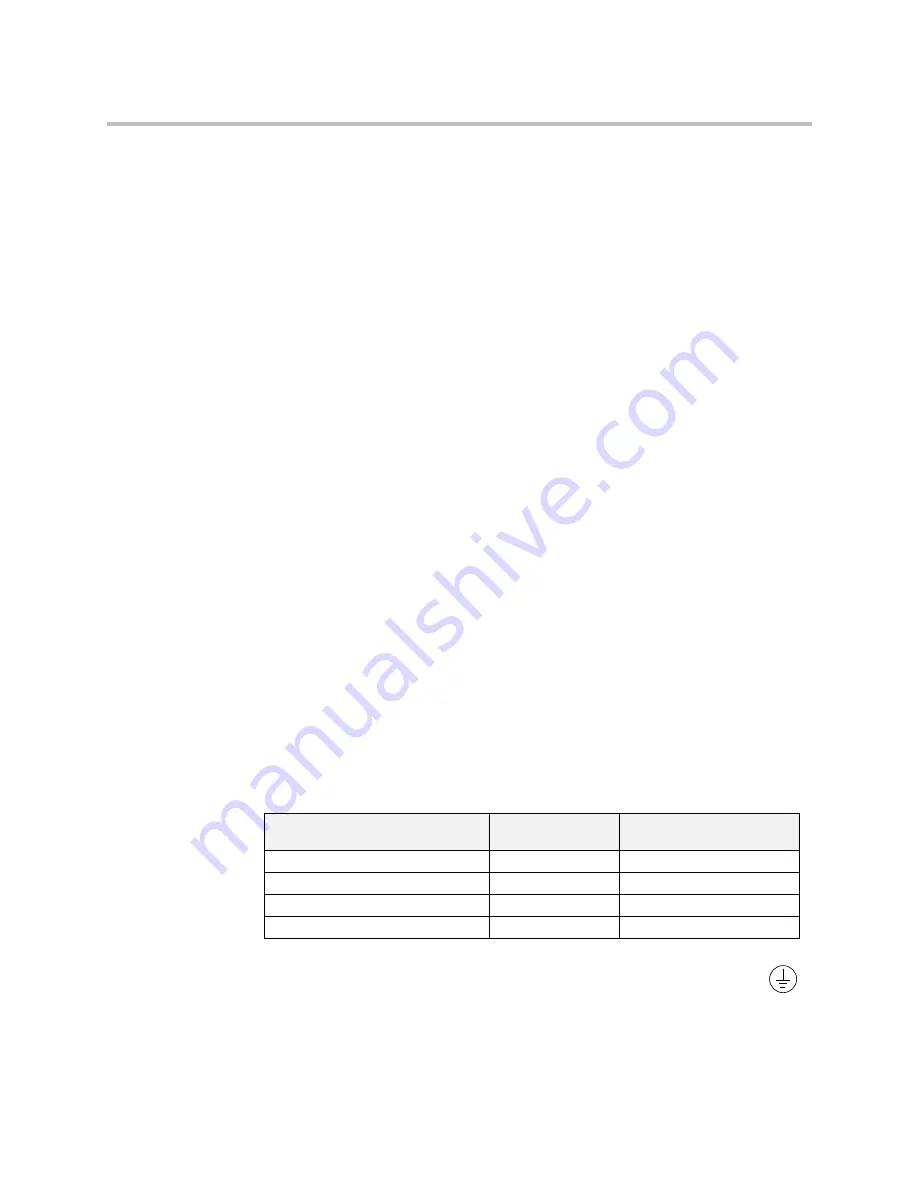
12-6
Certification for the Servo Drive
07-01-08-02-E-V0500 631 Digital Servo Drive
Requirements for UL Compliance
Solid-State Motor Overload Protection
These devices provide Class 10 motor overload protection. The maximum internal overload
protection level (current limit) is 200% for 9 seconds.
An external motor overload protective device must be provided by the installer where the motor
has a full-load ampere rating of less than 50% of the drive output rating. Refer to Chapter 4:
“Operating the Servo Drive” - Motor Overlaod Protection for user current limit adjustment
information..
Internal motor overload is also provided for use with an external thermal device located within
the winding of the motor. This protection cannot be evaluated by Underwriters Laboratories Inc.
and hence it is the responsibility of the Installer and/or local Inspector to determine whether the
overload protection is in compliance with the latest edition of the National Electrical Code,
NEC/NFPA-70.
Short Circuit Rating
All models of this Inverter are suitable for use on a circuit capable of delivering not more than
5,000 RMS Symmetrical Amperes, 240V maximum.
Solid-State Short-Circuit Protection
These devices are provided with Solid-State Short-Circuit (output) Protection. Branch circuit
protection requirements must be in accordance with the latest edition of the National Electrical
Code NEC/NFPA-70.
Recommended Branch Circuit Protection
It is recommended that UL Listed (JDDZ) non-renewable cartridge fuses, Class K5 or H; or UL
Listed (JDRX) renewable cartridge fuses, Class H, are installed upstream of the Inverter. Refer
to Chapter 11: “Technical Specifications” - Power Details for recommended fuse ratings.
Motor Base Frequency
The motor base frequency rating is 500Hz maximum.
Field Wiring Temperature Rating
Use 75°C Copper conductors only.
Field Wiring Terminal Markings
For correct field wiring connections that are to be made to each terminal refer to Chapter 3:
“Installing the Inverter” - Power Wiring Connections, and Control Wiring Connections.
Power Wiring Terminals
Model Recognition
Model Recognition
Model Recognition
Model Recognition
Product Code(Block 2 & 3)
Product Code(Block 2 & 3)
Product Code(Block 2 & 3)
Product Code(Block 2 & 3)
Power Terminals
(maximum wire size)
Brake Terminals DBR1, DBR2
(maximum wire size)
001/230
12 AWG (3.3mm²)
12 AWG (3.3mm²)
002/230
12 AWG (3.3mm²)
12 AWG (3.3mm²)
004/230
12 AWG (3.3mm²)
12 AWG (3.3mm²)
006/230
12 AWG (3.3mm²)
12 AWG (3.3mm²)
Field Grounding Terminals
The field grounding terminals are identified with the International Grounding Symbol
(IEC Publication 417, Symbol 5019).
Operating Ambient Temperature
Heavy duty devices are considered acceptable for use in a maximum ambient temperature of
45°C (40°C for models with a Type 1 Enclosure). Normal duty devices are considered suitable
for use in a maximum ambient temperature of 40°C for both `open type’ and Type 1 Enclosed
models.