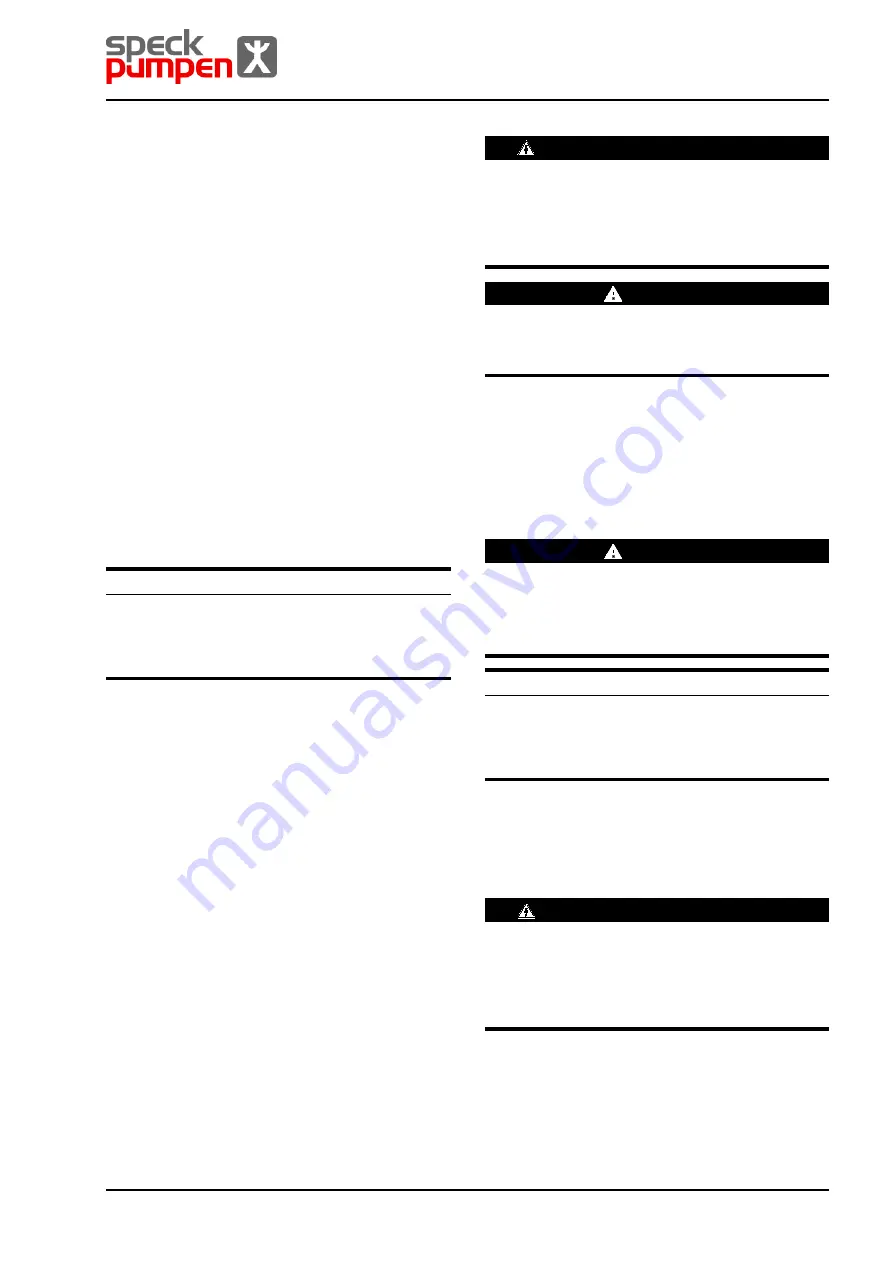
Operating
Instructions
05/2011
1096.0833 | CY, CSY, LNY, LSY, NPY, PY, Y, YS Series
13
5.3.5
Safety and control devices
Please observe the following recommendations for a trou-
ble-free aggregate operation.
5.3.5.1
Avoiding contamination
1.
Install a filter in the suction pipe
(screen cross-section = 3 x DN
S
, mesh size 0.1 mm).
2.
Install a differential pressure gauge with contact manome-
ter to monitor the contamination process.
5.3.5.2
Avoiding backflow
►
Put a check valve between the outlet nozzle and the gate
valve to prevent the medium to be pumped from flowing
back after the aggregate has been switched off.
5.3.5.3
Provisions for isolating and shutting off pipes
For maintenance and repair works
►
Provide for shut-off devices in the suction and pressure
pipe.
5.3.5.4
Provisions for measuring operating conditions
1.
For pressure measuring: provide for manometers in the
suction and pressure pipe.
2.
Provide for a power sensor at the motor side.
3.
Provide for temperature measurement at the pump side.
5.4 Connecting pipes
5.4.1
Providing for clean piping
CAUTION
Risk of material damage caused by aggregate contamina-
tion!
►
Make sure the inside of the aggregate is kept free of con-
tamination.
1.
Clean all piping parts and fittings prior to assembly.
2.
Make sure no flange seals project inwards (NPY-2051 self-
priming/Y-5081/CY-5091/Y-6091).
3.
Make sure no sealing material (sealing tape, adhesive)
projects inwards.
4.
Remove any blank flanges, plugs, protective foils and/or
protective paint from the flanges.
5.4.2
Installing suction pipe
1.
Remove transport and sealing covers from the aggregate.
2.
Lay out the feed pipe with a continuous slope down to the
aggregate and the suction pipe with a continuous slope up
to the aggregate.
3.
Make sure no seals (flange designs only) project inwards.
4.
Suction lift mode:
It is recommendable to install a foot valve in the suction
pipe. It prevents the aggregate at standstill.
5.
Gravity feed mode:
Make sure the liquid level does not drop below the center
line of the shaft.
5.4.3
Installing pressure pipe
1.
Remove transport and sealing covers from the aggregate.
2.
Install the pressure pipe.
3.
Make sure no seals (flange designs only) project inwards.
5.4.4
Stress-free pipe connection
For the layout of piping, observe VDMA standard sheet
24277 on stress-free pipe connections.
5.5 Electrical connection
RISK OF ELECTRIC SHOCK
Risk of death from electric shock!
►
Any electrical works must be carried out by qualified electri-
cians only.
►
Observe the IEC 30364 (DIN VDE 0100) and for potentially
explosive areas the IEC 60079 (DIN VDE 0165) standard.
DANGER
Risk of death from rotating parts!
►
Make sure to only operate the aggregate with all covers
(fan hood, coupling guard) installed.
5.5.1
Motor connection
Observe the specifications of the motor manufacturer.
1.
Connect the motor in accordance with the circuit diagram.
2.
Exclude any risk associated with electric power.
The electric motor must be protected by an upstream motor
protection switch, which is set to I
N
(I
N
= nominal current).
5.5.2
Checking direction of rotation
DANGER
Risk of death from rotating parts!
►
Use protective equipment when carrying out any works on
the aggregate.
►
Keep an adequate distance to rotating parts.
CAUTION
Risk of material damage caused by dry running or incorrect
direction of rotation!
►
Fill the aggregate and pipes with the medium to be pumped
(
Filling and venting, page 14).
1.
Switch the aggregate on and immediately off again.
2.
Check whether the direction of rotation of the motor is in
accordance with the arrow indicating the direction of rota-
tion on the aggregate.
Wrong direction of rotation may result in damage and es-
cape of operating liquid at the mechanical seal.
RISK OF ELECTRIC SHOCK
Risk of death from electric shock!
►
Any electrical works must be carried out by qualified electri-
cians only.
►
Observe the IEC 30364 (DIN VDE 0100) and for potentially
explosive areas the IEC 60079 (DIN VDE 0165) standard.
3.
In case of deviating direction of rotation: Swap the two
phases (three-phase drive).