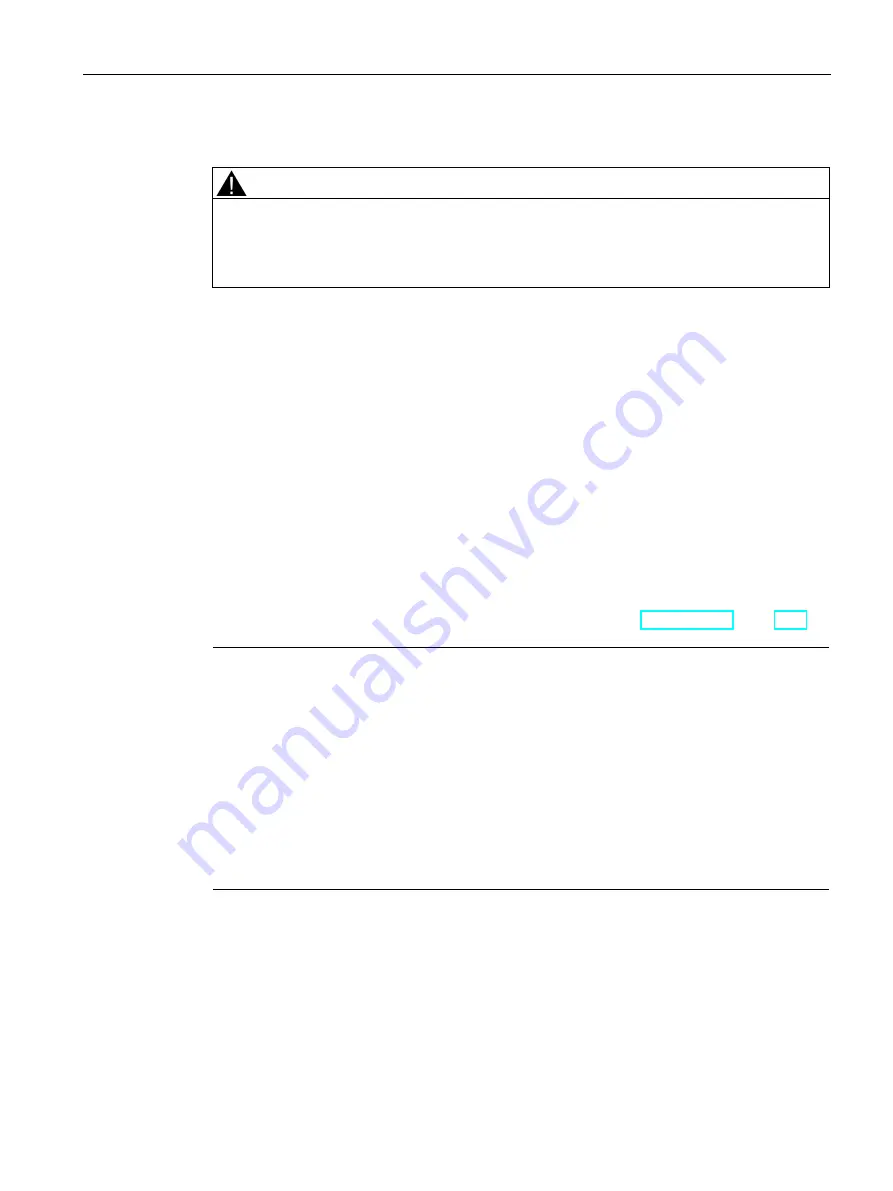
Functions
3.5 Motor control
M200D PROFIBUS/PROFINET
Manual, 08/2014, A5E01577426A/RS-AA/004
39
Brake output
WARNING
Dangerous voltage
Risk of death or serious injury
The brake is only switched in a single phase. This means that voltage can be applied at pin
6 even when the system is switched off.
Externally supplied motor brakes are usually powered via a jumper on the motor terminal
board.
Since switching the motor and brake simultaneously can increase wear and tear to the
brake, all M200D motor starters can be fitted with an optional electronic brake controller.
(Order variant)
Depending on the order variant, the following externally supplied brake coils can be
controlled:
●
400 V AC/230 V AC
The brake rectifier must be installed in the motor. The rectifier input is controlled via the
motor starter.
●
180 V DC
A rectifier is not required for the brake in the motor because the motor starter provides
the 180 V DC. This allows brake coils for 180 V DC to be switched direct.
The brake voltage is fed to the motor together with the motor infeed via a joint cable. For
more information about connecting the brake output, see section Brake output (Page 108).
Note
With both brake output versions, the electronic switching element is located on the AC side.
Please refer to the technical data of the brake (e.g. Catalog D87.1 "SIEMENS MOTOX
Geared Motors") for the resulting engaging time of the brake.
If faster brake engaging times are required (DC side tripping), a 400 V / 230 V AC brake
output in conjunction with a function rectifier integrated into the motor is preferable.
Devices with a 180 V DC brake output as of product version E10 are suitable for achieving
fast brake engaging times. This means that the time until the motor comes to a standstill is
shorter compared with previous product versions.
The integrated free-wheeling diode is deactivated when the brake output switches off and
the energy of the brake coil is dissipated using a varistor.
Содержание SIRIUS M200D
Страница 2: ......
Страница 16: ...Product description 1 3 PROFIenergy M200D PROFIBUS PROFINET 16 Manual 08 2014 A5E01577426A RS AA 004 ...
Страница 24: ...Product family 2 3 Design concept M200D PROFIBUS PROFINET 24 Manual 08 2014 A5E01577426A RS AA 004 ...
Страница 90: ...Functions 3 22 Logbook M200D PROFIBUS PROFINET 90 Manual 08 2014 A5E01577426A RS AA 004 ...
Страница 118: ...Mounting connection 4 2 Connection M200D PROFIBUS PROFINET 118 Manual 08 2014 A5E01577426A RS AA 004 ...
Страница 222: ...Appendix A 2 Order numbers M200D PROFIBUS PROFINET 222 Manual 08 2014 A5E01577426A RS AA 004 ...
Страница 224: ...Correction sheet M200D PROFIBUS PROFINET 224 Manual 08 2014 A5E01577426A RS AA 004 ...
Страница 232: ...Index M200D PROFIBUS PROFINET 232 Manual 08 2014 A5E01577426A RS AA 004 ...
Страница 233: ......