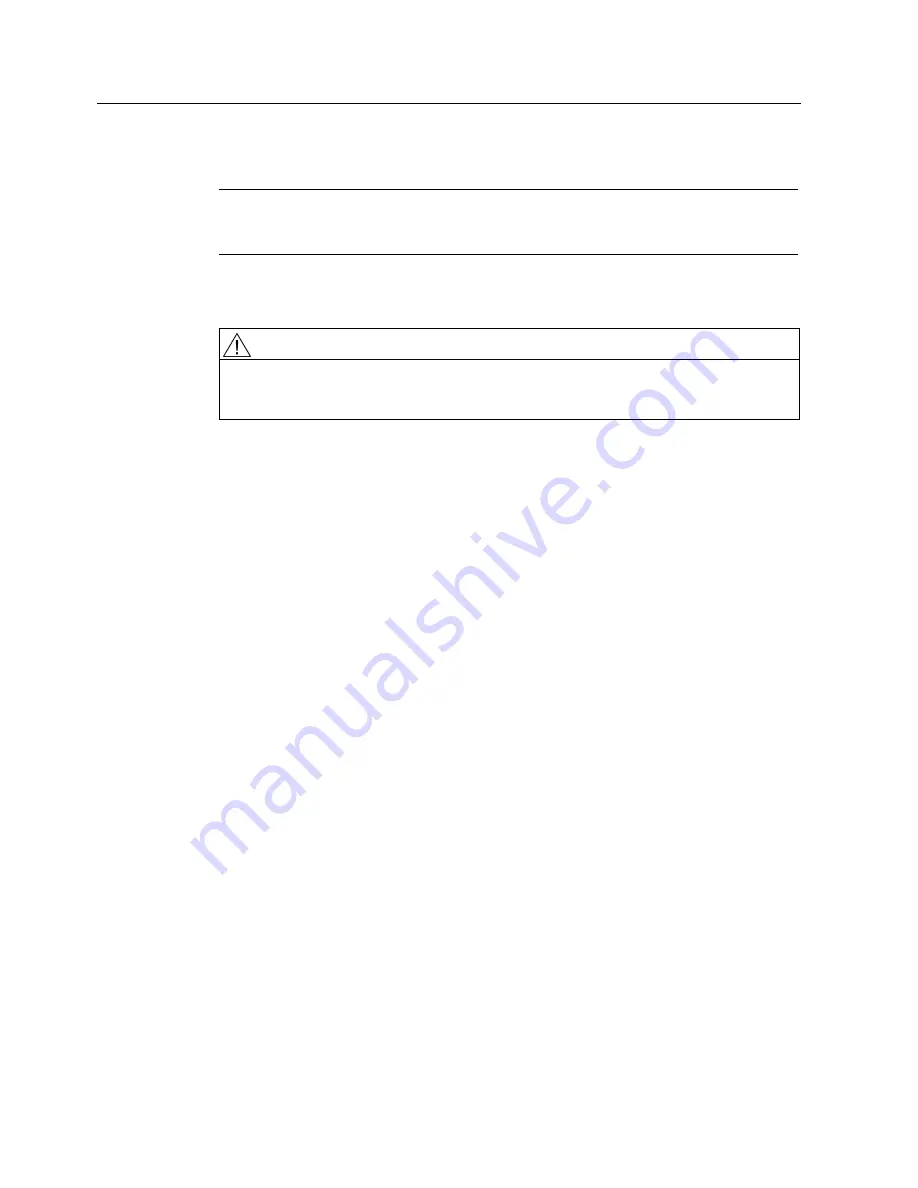
Installing/Mounting
4.2 Connecting a CU240S via Terminals
Control Units CU240S
32
Operating Instructions, 07/2008 - FW 3.2, A5E00766042B AD
Terminal wiring examples for the Control Unit CU240S
Note
To control the CU240S DP, CU240S DP-F or CU240S PN via terminals is also possible, but
in this case the parameter settings for command and setpoint source have to be changed.
In this section examples of controlling a SINAMICS G120 inverter with a CU240S via
terminals are shown.
CAUTION
Use of unscreened cables is possible, however we recommend the use of screened cables
in order to fulfill the EMC requirements for the CE marking and fail-safe products (CU240S
DP-F).
● Control with the default settings
● Frequency setpoint and an additional setpoint via terminals
(AI0 and AI1 used as voltage inputs)
● Frequency setpoint and an additional setpoint via terminals
(AI0 and AI1 used as current inputs)
Control with the default settings
When shipped from the factory the G120 inverter (Control Unit and Power Module) must not
be operated before the values depending on the specific PM are read into the CU.
This can be done via:
● Downloading a valid parameter set (by MMC, STARTER, or BOP)
● Quick commissioning
● A factory reset
To operate the inverter with the basic settings (e.g. after factory reset, without additional
parameterization or DIP switch setting), the following conditions have to be fulfilled:
● The rated current of the inverter is at least as great as the rated current of the motor.
● The power range of the inverter matches the power range of the motor.
● The controlled motor is a 4-pole motor (best Siemens 1LA7).
● The rated motor frequency is 50 Hz, power dimension unit is kW.
Control settings
Digital and analog inputs for commands and setpoints are parameterized for a cabling as
shown in the block diagram of the CU240S in the operating instructions. Furthermore the
state of the inverter is monitored via digital and analog outputs.