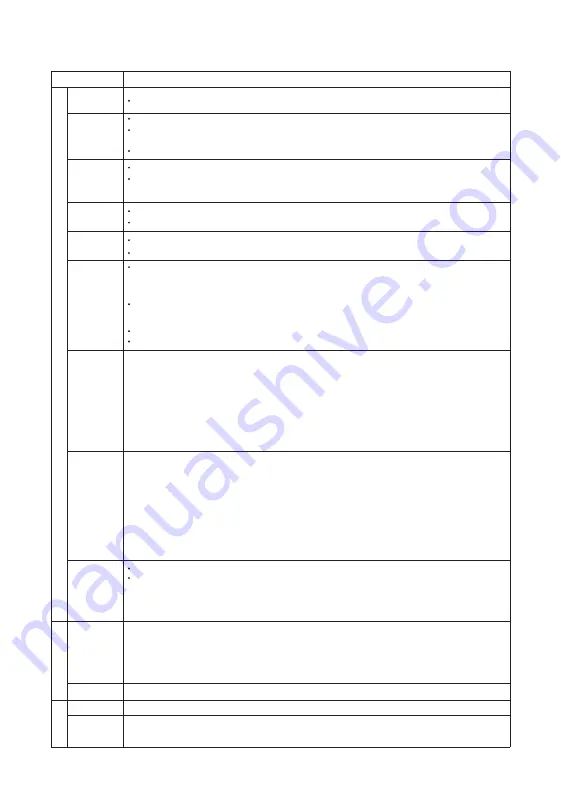
12
Hardware
current limiter
Torque limiter
Control
functions
Digital input
Item
Explanation
0.00 to 6000 s
,
Linear/S-curve/curvilinear, Acceleration/deceleration time settings 1 to 4 switchable.
Running continued at the stop frequency, coast-to-stop, or force to stop
DC braking: Braking starting frequency (up to 60 Hz), time (up to 30.0 s), and operation level (up to
100%).
Zero speed control (under vector control with speed sensor)
Trip immediately, trip after recovery from power failure, trip after deceleration to stop.
Continue to run, restart at the frequency at which the power failure occurred, restart at the starting
frequency, restart after searching for idling motor speed.
Settable Current limiting action value
Over current limiting by hardware (it can be canceled)
Terminals AFM: Output a selected signal with DC voltage (0 to +10 V) or DC current (4 to 20 mA)
Terminals DFM:Output a selected signal with pulse (25 to 6000p/s log voltage (0 to +10 V)
<
Selectable output signals
>
Output frequency (before slip compensation, after slip compensation), output current, output voltage, output
torque, load factor, input power, PID feedback amount, speed (PG feedback value), DC link bus voltage,
universal AO, motor output, calibration, PID command , PID output.
Alarm history: Saves and displays the last 4 alarm code and their detailed description
RS-485 COM port 1 (for keypad connection), RS-485 COM port 2 (on terminal block)
Torque limit value (±300%)
Torque limiter 1/2, torque limiter enabled/disabled, analog torque limit value.
Analog input adjustment (gain/offset/filter time constant), frequency limiter (high and low), bias frequency,
jump frequency,jogging operation, pre-excitation, switch to commercial power, commercial power switch-
ing sequence,cooling fan ON/OFF control, select motor 2 to 4, protect motor from dew condensation,
universal DI, universal DO,universal AO, rotational direction limitation.
Overload prevention control, auto search, slip compensation, over voltage stall prevention, droop control,
PID process control, PID dancer control, Deceleration characteristics (improving braking capability),auto
energy saving function.
Auto-tuning (Operating modes: motor load, do not connect the mechanical transmission parts.)
Light alarm, retry, command loss detection.
Run/stop forward and reverse command, select multi-frequency , select ACC/DEC time,Enable 3-wire
operation, Coast-to-stop command,reset alarm, enable external alarm trip, ready for jogging, select frequency
command 2/1, select motor 1 to 4, enable DC braking, select torque limiter level, switch to commercial power ,
UP/DOWN command, enable data change with keypad, cancel PID control, switch normal/inverse operation,
interlock,cancel torque limiter, enable communications link via RS-485, universal DI, select starting character-
istic, force to stop, pre-excitation, reset PID integral and differential components, hold PID integral
component,select local (keypad) operation, protect the motor from dew condensation, enable internal
sequence to commercial lines , pulse train input, pulse train sign, cancel constant peripheral speed
control,hold constant peripheral speed control frequency in the memory, switch to commercial power
operation (motor 1 to 4), select droop control, servo-lock command (under PG vector control),cancel PG
alarm (under PG vector control),cancel user logic,clear all user logic timers.
Inverter running, frequency arrival signal 1/3, frequency detected (3 points), under voltage detected (inverter
stopped), torque polarity detected, inverter output limiting, auto-restarting after momentary power failure,
motor overload early warning, keypad operation, inverter ready to run, switch motor power between commer-
cial line and inverter output (inverter input/output/commercial power), select the AX terminal function (primary
side MC), inverter output limiting with delay, cooling fan in operation, auto-resetting, universal DO, heat sink
overheat early warning, service lifetime alarm, reference loss detected, inverter operating, overload prevention
control, current detected (3 points), low level current detected, PID alarm, under PID control, PID control
stopped due to slow flowrate, low output torque detected, torque detected (2 points), switched to motor 1 to 4,
run forward signal, run reverse signal, inverter in remote operation, PTC status detection enabled, brake
signal, analog frequency reference loss on the terminal [ACI], inverter keeping speed output, speed arrived,
PG error detected, maintenance timer, light alarm, alarm relay contact output (for any fault), braking resistor
broken, positioning completion signal, user logic output signal.
Speed monitor (reference frequency (Hz), output frequency, motor speed, load shaft speed, line speed,
speed in %).
Output current, output voltage, torque calculation value, input power, PID command value, PID feedback
amount, PID output, load factor, motor output, torque current, flux command, analog signal input monitor,
cumulative inverter run time, cumulative motor run time, input watt-hour, number of startups, I/O checking,
energy-saving monitor.
Upon detection of a momentary power failure lasting more than 15 ms, this function stops the inverter
output. If restart after momentary power failure is selected, this function invokes a restart process if power
is restored within a predetermined period (allowable momentary power failure time).
Acceleration/
deceleration time
Stop control
Auto-restart
after
momentary
power failure
Transistor
output
Analog
output
Running
/stopping
Alarm inform-
ation
Communicat-
ions
Protection against
momentary
power failure
O
th
er
s
In
di
ca
tio
n
C
on
tro
l
Содержание S3800C Series
Страница 17: ...S3800C S3800C S3800C S3800C S3800C S3800C 14 ...
Страница 18: ...FALSE frequency carrier carrier frequency 00 26 15 ...