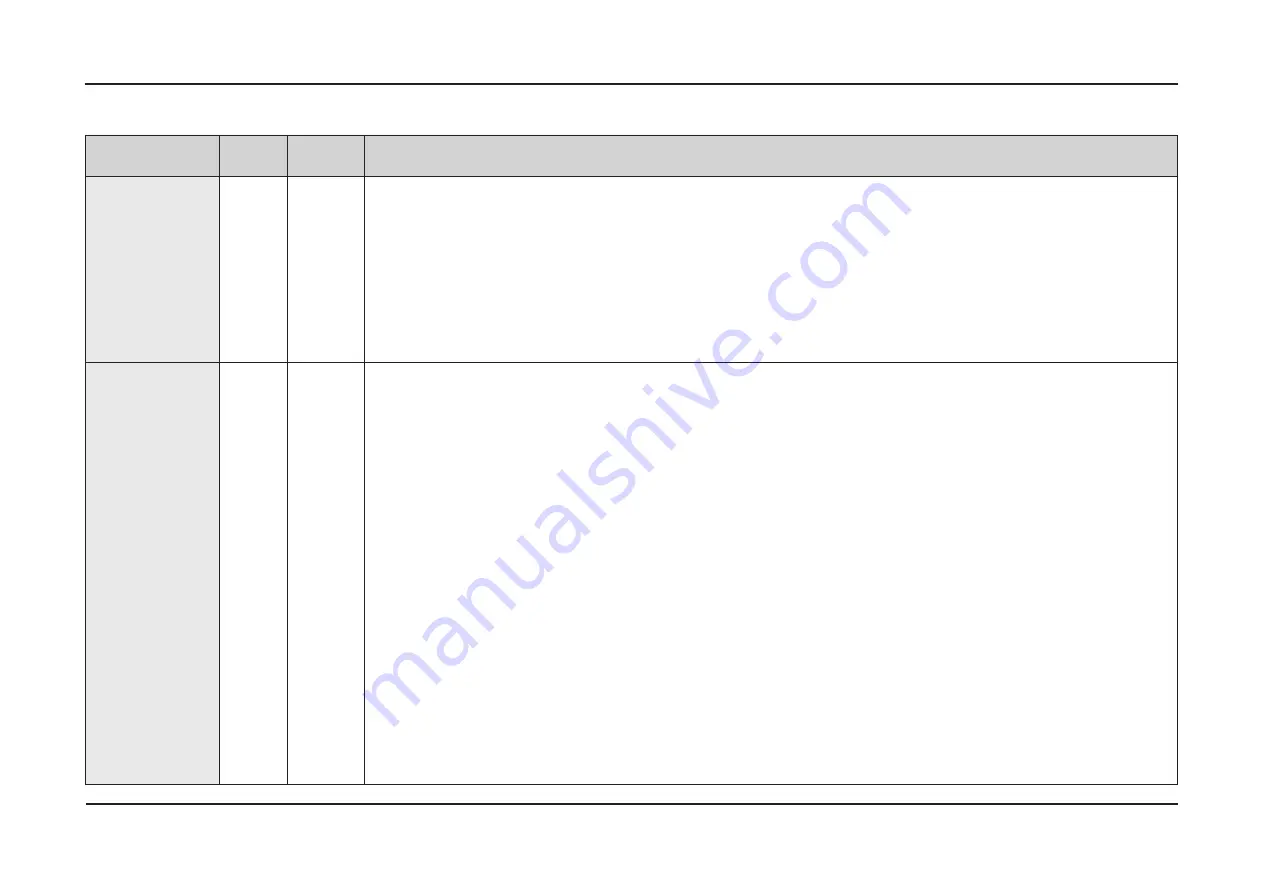
Troubleshooting_41
Item
Related
Parts
Symptoms
Description
Auto Mode
Configuration
9. [Auto Mode STEP 5: check drying]
1) Operate Auto Door Open Actuator.
- If the Door does not open within 3 minutes after the Auto Door Open Actuator is run, it will Retry once (10 seconds Off, 3 minutes On).
- If the Door does not open after the retry, a DC3 check code will occur.
2) If the door open is detected after Auto Door Open, operate for additional 30 seconds from the time the door opens and complete the
Auto Door Open step.
3) Operate the Fan Motor and Dry Actuator for 30 seconds. (Only for models with the relevant part)
4) Once the above 1), 2) and 3) are complete, proceed to [STEP 6].
10. [Auto Mode STEP 6: complete the Auto Mode operation]
1) "OK" displays.
2) At the time Auto Mode operation completes, Smart Install Auto Mode Completion is saved to EEPROM.
Manual Mode
Configuration
- Each time Auto Key is pressed, the Manual Mode step changes indicating Step No.
- After Max Step No. is selected, it is automatically changed to Auto Mode "AS”.
- Start Key must be pressed to start the Manual Mode steps.
- The Step of the manual mode will operate only when the Door is closed within 3.7 seconds after entering the Start Key.
- If the Door opens during operation, it will stop and the Door Open check code “dC(dC1)” will be displayed.
- If the Door is left open for 3.7 seconds after the Start Key is entered, the Door Open check code “dC(dC1)” will be displayed.
※
dC1 will occur if Door Open information is detected only in Inverter Micom.
- During manual mode operations, if the relevant Step number blinks and the relevant Step operation has been completed, the Display
will indicate the relevant Step number.
- Once this Manual Mode step is complete, the Step No. stays turned on in the display.
- If the Door opens during operation, it will stop and the Door Open check code “dC(dC1)” will be displayed.
(However, Auto Door Open Mode is an exception. The operation is resumed as it detects the door is open.)
- When the Door open check code "dC(dC1)" is displayed, pressing the Start Key will turn the check code display off and it will restart.
- When restarting, the mode starts from the beginning.
- For models with a vane, the vane must be always positioned at parking when the bottom nozzle starts spraying (to prevent leakage).
1. [Manual Mode STEP 1: drain / supply of water]
1) Perform Auto Mode STEP 4 (drainage) and STEP 2 (water supply).
2. [Manual Mode STEP 2: check the nozzle]
- Each time Normal Course Key is pressed, the setting changes by 100rpm (it can be set to 1201~3500RPM).
- Delicate Key: 2400 (default RPM) → 2300 → 2200 → 2100 → (Change to RPM decreasing direction)
AC circulation pump model: change to Low (default) → Hi →Low -> Hi → ...
(When the key is pressed, the RPM displays for 2 seconds.)
- Each time Heavy Course Key is pressed, the alternation nozzle position can be set and it starts from its default position.
Unused alternation cannot be set.
No. 1 (default: the default position varies by model → No. 2 → No. 3 → No. 4 → No. 5 → No. 6 (max. alternation target position:
varies by model) → No. 1 → Please refer to [Dish Washer-Washing Performance Specifications-Distributor Control] for the specifications of
alternation position by model. (When the key is pressed, the current target alternation position displays for 2 seconds.)