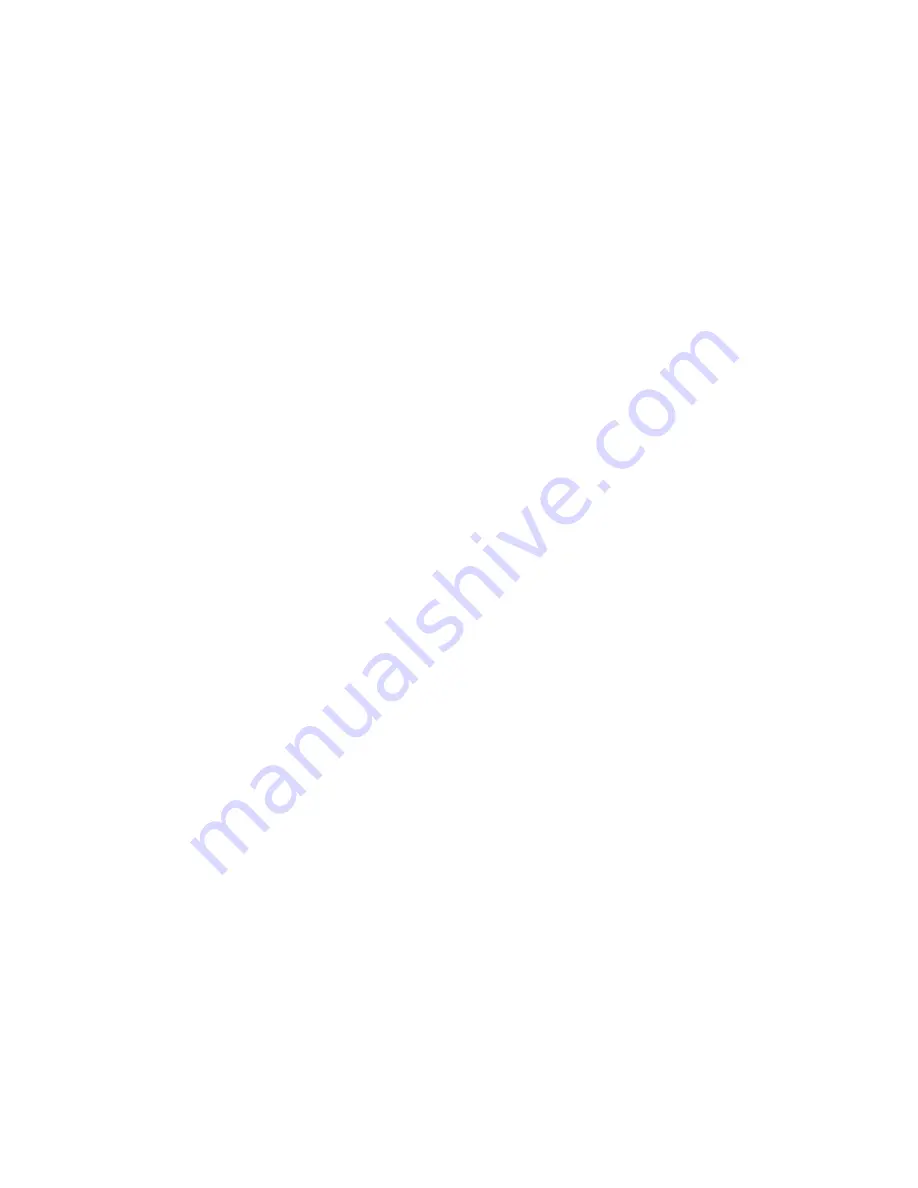
2200
23
rotor (3) to 140° - 160° F max. Check the temperature with a heat stick or
freeze the drive shaft (5) using liquid nitrogen. Insert the driveshaft.
Install the six socket head cap screws (83). Do not tighten the screws
until the driveshaft and the rotor have reached the same temperature, then
torque to 100 ft. lbs.
4.1.2
Place the endplate (15) on the shaft (5) as shown in assembly drawing
(
Figure 2-7
). Install wave spring (66) and the hardened shim (111).
4.1.3
Heat the rotor bearing (11) to 150°-170° F. Check the temperature with a
heat stick. Place the bearing on the shaft against the shoulder as shown
in assembly drawing (
Figure 2-7
) letters up.
4.1.4
Heat the oil slinger (19) to 120°-150° F and install after bearing as shown
in assembly drawing. Install self lock nut (47). Torque to 250 ft. lbs.
4.1.5
Heat the thrust bearing oil slinger (20) to 120°-150° F and install onto the
shaft (5) as shown in the assembly drawing (
Figure 2-7
).
4.1.6
Heat the thrust bearing (12) to 150°-175° F. Check the temperature with
the heat stick. Place bearing on shaft with the wide shoulder of the inner
race against the shoulder of the oil slinger (20).
4.1.7
Place the thrust bearing matched spacer set (23) around the shaft (5) and
against the thrust bearing (12).
4.1.8
For Model 2200A:
Heat the radial bearing (13A) to 150°-175° F, and
place it on the shaft against the thrust bearing spacer set with the wide
face of the inner race facing away from the bearing spacers.
For Model 2200B:
Heat the inner race of the roller bearing (13B) to 150°-
175° F and place it on the shaft against the bearing spacer. Place the
outer race and roller in position over the inner race after it has completely
cooled.
4.1.9
Install spacer (28) on shaft.
4.1.10 Place self-locking nut (46) on the shaft (5) and torque to 175 ft. lbs.
4.1.11 For drive bearing conversion, see Appendix A.
4.2.
PEDESTAL SLEEVE INSTALLATION
Press or freeze pedestal bushing (100) using liquid nitrogen and install all
the way into the bore of the pedestal (17) with the step towards the back.
The face of the sleeve must be parallel to the face of the pedestal end
plate machined surface to within .001 inches.
Содержание 2200
Страница 8: ...2200 5 2 2 DIMENSIONAL DRAWINGS Figure 2 2 2200 2x2 Dimensional Drawing ...
Страница 9: ...2200 6 Figure 2 3 2200 3x2 Dimensional Drawing Threaded ...
Страница 10: ...2200 7 Figure 2 4 2200 3x2 Dimensional Drawing Flanged ...
Страница 15: ...2200 12 Figure 2 7 2200 Rotor Assembly Section Drawing ...
Страница 36: ...2200 33 9 MAINTENANCE RECORD DATE SERIAL NO MAINTENANCE RECORD BY ...
Страница 40: ...2200 37 Figure B 2 Alignment Tool Location 3x2 Pump ...