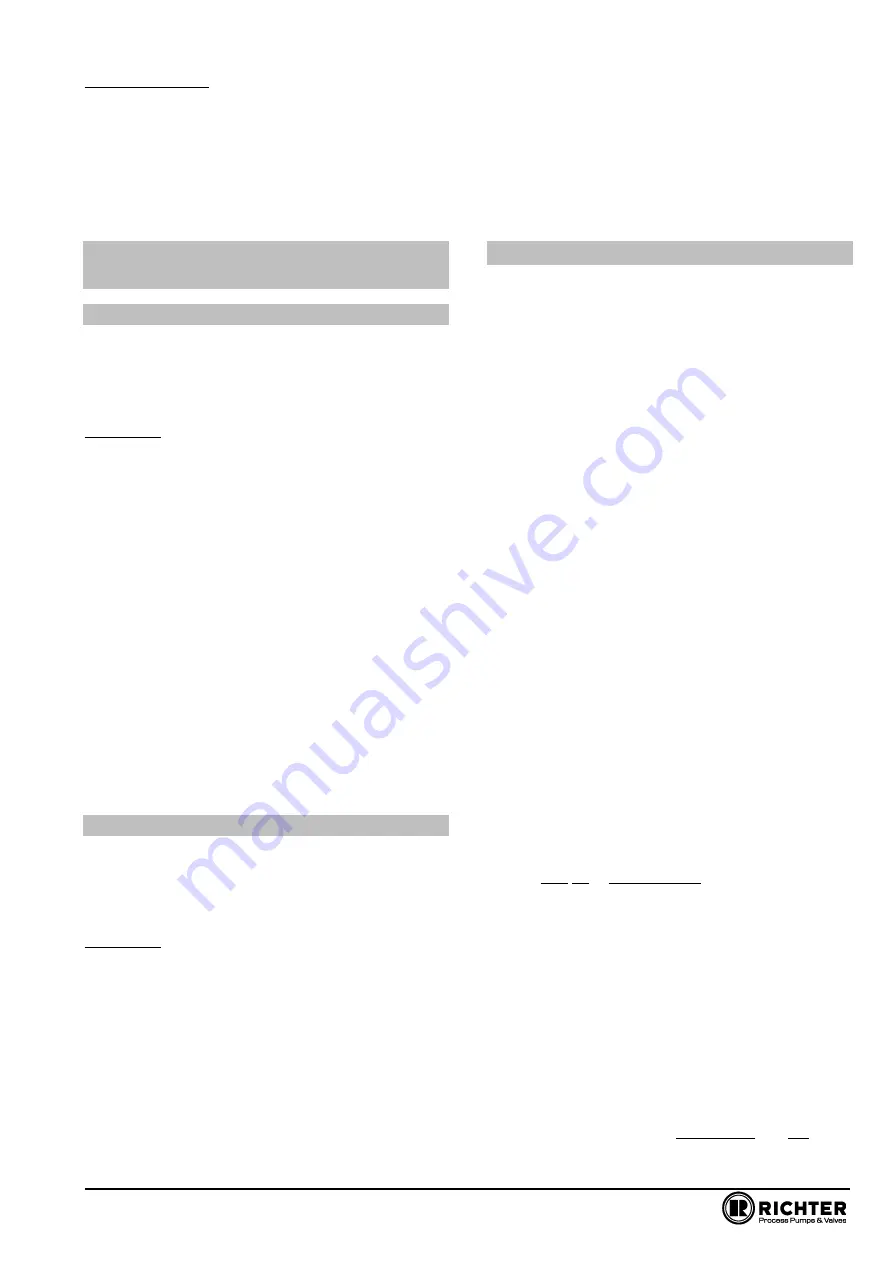
Series SCK, Size 25-25-100
Page 18
9220-003-en
Revision 14
TM 10272
Edition 01/2021
Oil bath lubrication
Unscrew rear bearing cover
361
with rotary shaft
seal
421/1
from the bearing pedestal
330
.
Remove circlip
932/2
.
The shaft
210
with the radial ball bearing
321/1
is
pressed on a press towards the pump side out of
the bearing pedestal.
7.8 Changing the radial ball bear-
ings
7.8.1 Long life grease lubrication
Pull radial ball bearing
321/2
out of the bearing pedes-
tal
330
.
Remove circlip
932/1
.
Press radial ball bearing
321/1
off the shaft.
Installation:
Press new radial ball bearing
321/2
onto the shaft
210
.
Insert circlip
932/1
.
Force shaft
210
with radial ball bearing into the bear-
ing pedestal
330
.
Insert circlip
932/2
on the motor side.
Provide grease seal.
Mount and screw rear bearing cover
361
.
Mount new radial ball bearing
321/1
.
Provide grease seal.
Mount bearing cover
360
and screw to bearing pedes-
tal.
Insert shoulder ring
505
.
Insert cup springs
950/1
.
Cup springs are to be mounted in alternating direc-
tions.
Insert spring bushing
546
.
7.8.2 Oil bath lubrication
Pull radial ball bearing
321/2
out of the bearing pedes-
tal
330
.
Remove circlip
932/1
.
Press radial ball bearing
321/1
off the shaft.
Installation:
Press new radial ball bearing
321/2
onto the shaft
210
.
Insert circlip
932/1
.
Force shaft
210
with radial ball bearing into the bear-
ing pedestal
330
.
Insert circlip
932/2
on the motor side.
Provide grease seal.
Mount and screw rear end cover
361
.
Mount new radial ball bearing
321/1
.
Provide grease seal.
Insert bearing cover
360
and screw to bearing pedes-
tal.
Insert shoulder ring
505
.
Insert cup springs
950/1
.
Cup springs are to be mounted in alternating direc-
tions.
Insert spring bushing
546
.
7.9 Notes on assembly
Use original spare parts. See also
Section 2.4
.
Do not use any defective parts.
The recommendations of the mechanical seal manu-
facturer are to be observed.
Close-tolerance areas, screws and cup springs are to
be treated with a grease to protect against corro-
sion.
Grease chambers which serve to protect the bearings
must be filled with grease long life grease lubrica-
tion).
The locking unit
930
must not be greased during as-
sembly.
The circlips
932/1
and
932/2
for the shaft are a rein-
forced version.
Replace all static sealing elements on re-assembly.
When using a bellows-type mechanical seal whose
clamping surface is made of PTFE, it must be en-
sured that only original shaft sleeves with the
greater surface roughness required for this me-
chanical seal are used.
Shaft sleeves
524
made of ceramic materials should
be able to turn easily on the shaft
210
. If the fitting
is too tight, the plastic bearing points in the shaft
sleeve are to be reamed.
If the shaft sleeve only has one leading chamfered
edge, it must lie on the side of the cup springs. The
surface of the shaft sleeve must be absolutely
clean; that also applies to the leading chamfered
edge.
Cup springs are to be mounted in alternating direc-
tions. .
See
Fig.
11
in
Section 7.7.1
.
The impeller
230
is to be mounted until the locking
unit
930/1
sits perfectly.
The dimension X specified in the works certificate
between impeller
230
and back plate
161
is to be
observed. If the actual dimension deviates from the
target dimension, an assembly error has been
made.
The dimension
Y
between the impeller and the hous-
ing can be influenced by the thickness of the hous-
ing gasket
401
. If the pump is used at higher tem-
peratures than originally expected, the dimension
Y is to be increased according to the works infor-
mation. Refer also to the Richter works certificate
and sectional drawing in
Section 9.2
and
9.3
.
Finally, the pump housing is to be subjected to the
operating pressure.