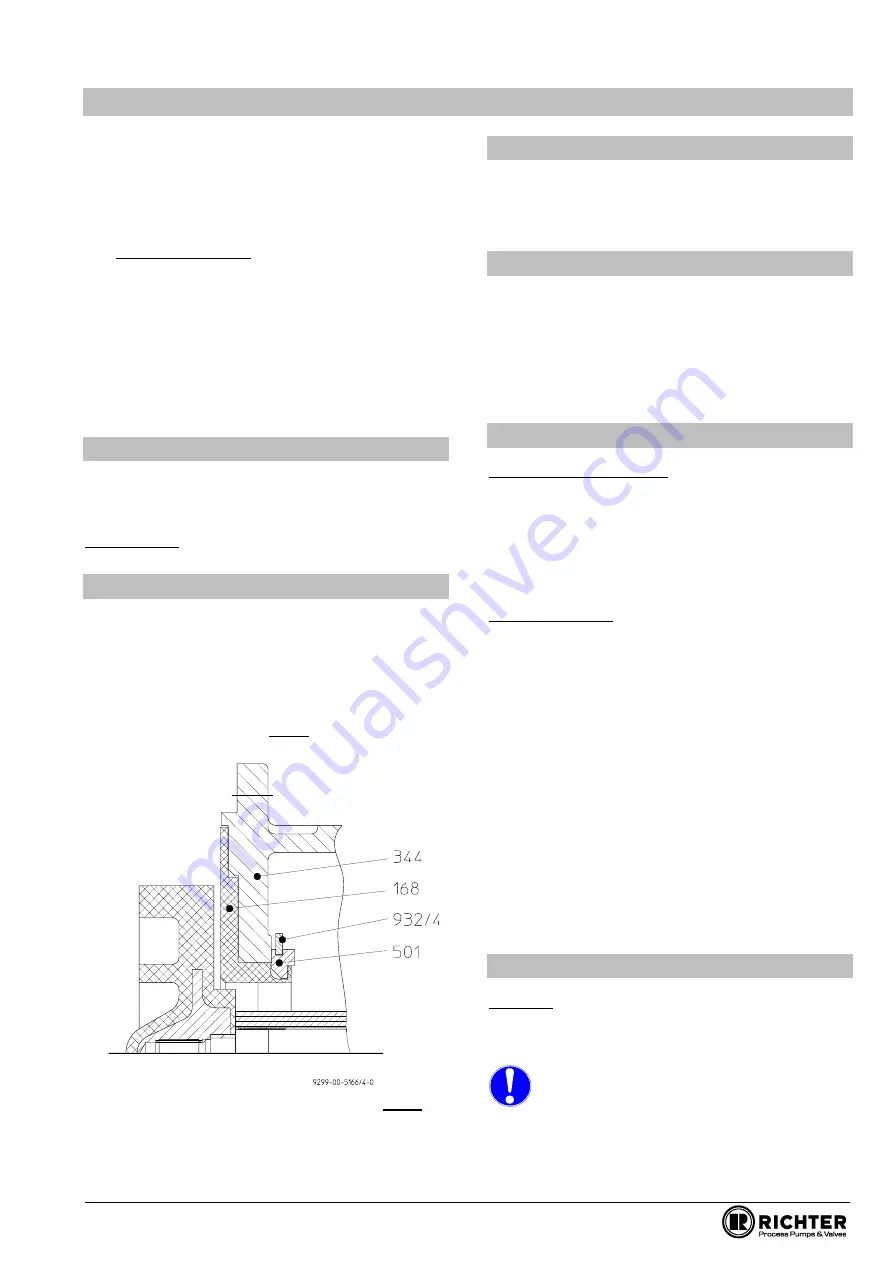
Series SCK, Size 25-25-100
Page 10
9220-003-en
Revision 14
TM 10272
Edition 01/2021
4
Product description
The housing dimensions, nominal ratings and tech-
nical requirements of the pump series SCK corre-
spond to ISO 2858 / DIN EN 22858 / DIN ISO 5199.
The technical requirements of the VDMA 24279 are
satisfied.
The sectional drawing shows the design of the pump.
See
Section 9.2 and 9.3
.
Additional information for the pump is provided in the
brochure.
All components which come into contact with the me-
dium are either plastic-lined or made of other resistant
materials, e.g. silicon carbide.
The pump consists of the assemblies:
Housing, lantern/back plate, impeller, shaft sleeve,
bearing pedestal, shaft gasket and mechanical seal
(separate manual).
4.1 Housing
The metallic shell gives the plastic lining of the hous-
ing
100
the necessary stability.
Optionally, the housing can be fitted with a drain (see
Section 5.4.6
) or heating. This is shown in the data
sheet or in a separate technical document.
4.2 Lantern with back plate
The replaceable back plate
161
consists of the back
plate insert
168
, a two-piece ring
501
and circlip
932/4
. These parts can also be replaced by the cus-
tomer.
The back plate insert
168
is held in the lantern
344
by
a 2-piece ring
501
. A circlip
932/4
holds the 2-
piece ring together. See
Fig. 2
.
Fig. 1
4.3 Impeller
For strength reasons the impeller
230
has a metallic
core inside with which is it screwed onto the shaft
210
.
A locking unit
930/1
is installed between the impeller
and the shaft as an anti-torsion insert.
4.4 Shaft sleeve
To protect the shaft
210
against corrosion, the section
between the impeller and the shaft gasket is protected
with a shaft sleeve
524
made of a hard, corrosion-
resistant material.
A plastic lining is provided at the bearing points in the
shaft sleeve made of non-metallic materials in order to
permit a safe transition to the metallic shaft.
4.5 Bearing pedestal
Long life grease lubrication
The bearing
321/2
on the motor side is designed as a
fixed bearing and that on the pump side as a floating
bearing
321/1
.
A rear bearing cover
361
is installed on the motor side
as additional protection. Grease is provided between
the rear bearing cover and the bearing as corrosion
protection. An additional seal can be installed.
Oil bath lubrication
The bearing pedestal
330
contains radial ball bearings
321/1, 321/2
, which are lubricated by an oil bath. The
fixed bearing is arranged on the motor side, the
floating bearing on the pump side.
A rear bearing cover
361
, which accomodates a rotary
shaft seal
421/1
and an O-ring
412/1
for oil sealing, is
installed on the motor side.
A so-called spring bushing
546
is installed on the
pump side.
It has several functions:
Any medium emerging from the mechanical seal is
kept away from the bearing.
Cup springs
950/1
, which press the shaft sleeve
524
against the impeller
230
are inserted in order to
seal at that location.
It serves as a running surface when an additional seal
ring is installed.
4.6 Mechanical seals
Designs:
Single mechanical seal external
Double mechanical seal to DIN EN 12756
See the relevant installation and operating
manuals of Richter or the mechanical seal
manufacturer.