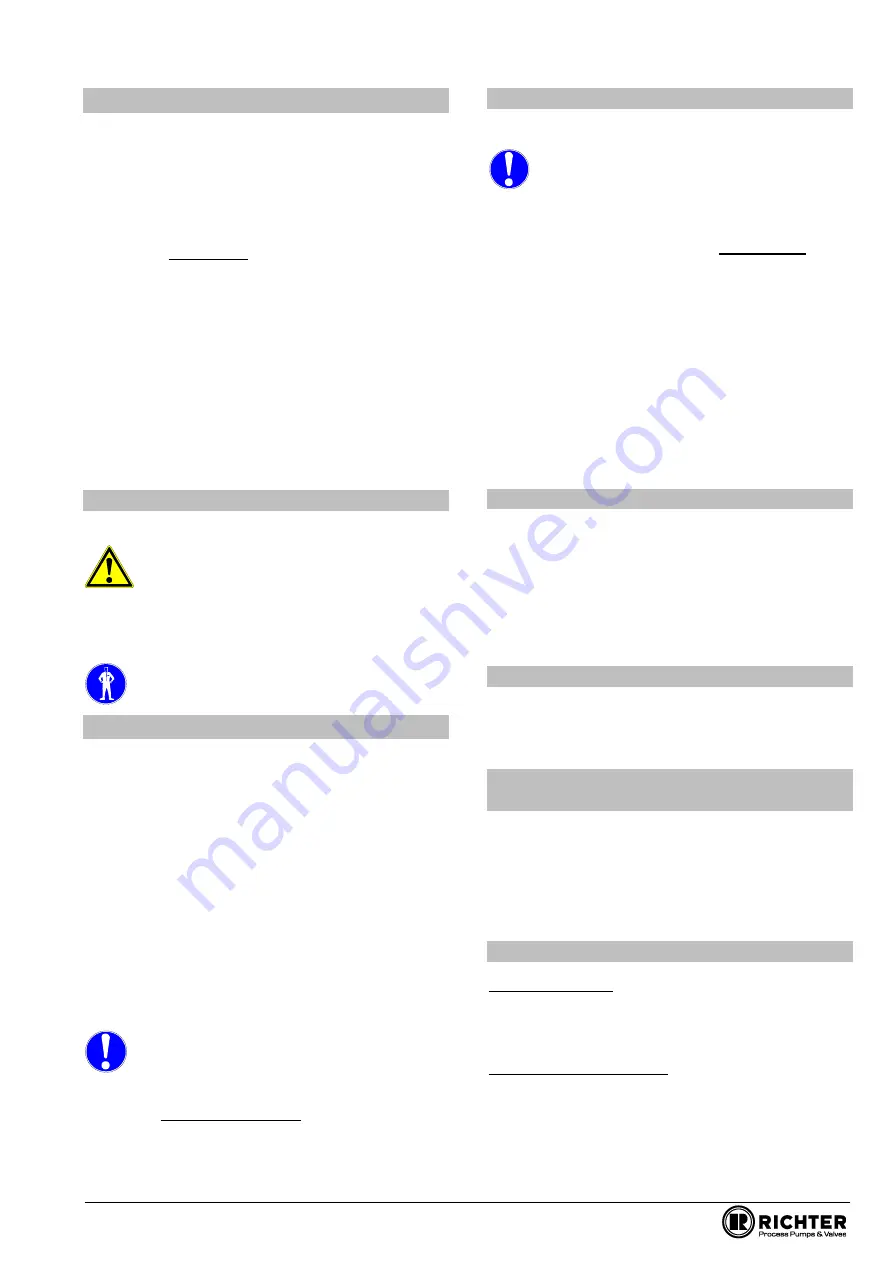
Series SCK, Size 25-25-100
Page 17
9220-003-en
Revision 14
TM 10272
Edition 01/2021
7.6 Notes on dismantling
All repair and maintenance work is to be performed by
skilled staff using appropriate tools and original
spare parts.
Is the necessary documentation available?
Has the pump been shut down, drained and flushed in
accordance with the regulations?
See also
Section 6.3
.
If no new assembly is performed immediately after
dismantling, the plastic and ceramic components in
particular must be stored carefully.
The ceramic parts are relatively easy fragile; with the
plastic components the soft sealing surfaces in
particular are to be protected.
If the diameter of a plastic impeller is to be reduced, it
must be remembered that there is a metallic core
in the impeller which is not resistant to the medi-
um. The table of the machined diameters of plastic
impellers is to be observed. In case of doubt only
machine the area of the vanes.
7.6.1 Protective clothing
Even if the pump has been properly
evacuated and flushed, residue of the
medium may still remain in the pump, e.g.
between sealing surfaces or in the bearing
seats or in the can or the can insert.
Plastic components may absorb medium which
gradually emerges from the material after flushing.
Proper protective clothing is to be worn.
7.7 Dismantling
There are two possibilities for dismantling:
1. Dismantling the complete pump from the plant.
2. Dismantling the complete slide-in unit as the pump
housing can remain in the plant connected to the
piping.
If the coupling installed is a spacer-type coupling, the
motor can also remain in the plant.
Remove seal guard
685
(only with single mechanical
seal)
Undo support bracket
183
from the base plate.
Undo housing screws
901/3
,
554/11
Remove entire slide-in unit.
If the housing
100
remains in the plant, leave
the housing gasket
401
in the centering to
protect the housing sealing surface.
Dismantling can be checked using the sectional
drawing in
Section 9.2 and 9.3
and the components
available.
7.7.1 Dismantling slide-in unit
Clamp the slide-in unit in the vice.
It is imperative to use clamping jaws with an
aluminium surface.
Loosen impeller 230 with a strap wrench or assembly
wrench.
Right-hand thread!
For assembly aid for impeller, see
Section 10.1
.
The impeller is dismantled before or during disman-
tling of the mechanical seal, depending on the type of
mechanical seal.
After removing the impeller
230
, the locking unit
930/1
becomes visible.
The one half of the locking unit is generally seated
firmly on the impeller and the other half firmly on the
shaft.
If these parts are still in good condition, they are best
left assembled. If one or both locking unit halves
has/have to be removed, it/they may have to be
destroyed with a chisel.
7.7.2 Dismantling the mechanical seal
See the installation and operating manual for the re-
spective mechanical seal version:
External single mechanical seal or
Double mechanical seal to DIN EN 12756
9220-066-en
and/or operating manual of the mechanical seal man-
ufacturer.
7.7.3 Dismantling the shaft sleeve
The dismantling of the shaft seal is described in the
installation and operating manual of the respective
mechanical seal type.
7.7.4 Dismantling the lantern with back
plate
The dismantling of the lantern with back plate is de-
scribed in the installation and operating manual of the
respective mechanical seal type.
A replaceable back plate
161
can be dismantled after
removal of the circlip
932/4
and the 2-piece ring
501
.
7.7.5 Dismantling the bearing pedestal
Oil bath lubrication
Drain oil from hex. screw
901/4
.
Screw hex. socket screw
914/1
out of the bearing
cover
360
.
Long life grease lubrication
Unscrew rear bearing cover
361
from the bearing
pedestal
330
.