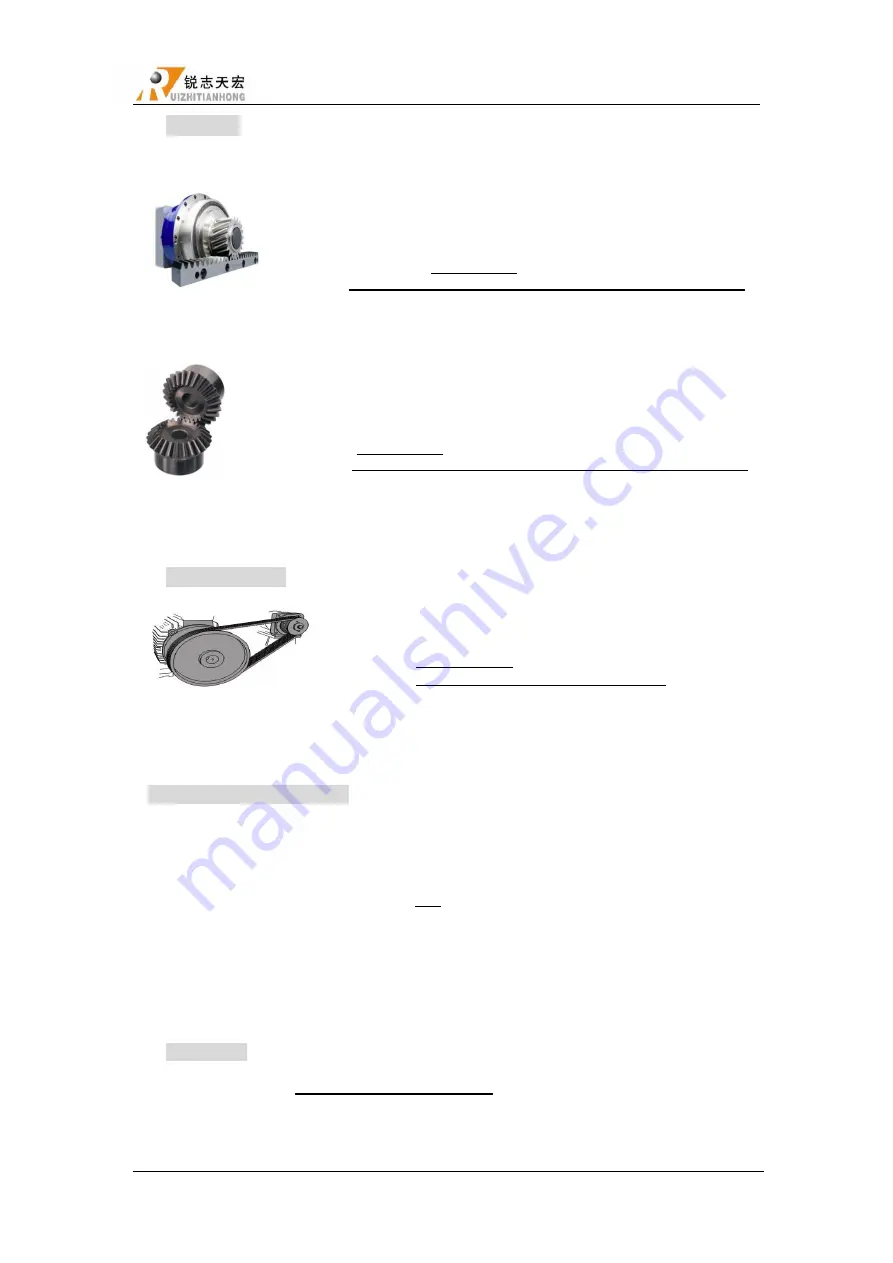
Beijing RichAuto S&T Co., Ltd.
Forging ahead and determined to win 71
Rack drive
:
►
Straight rack
:
pulse =
360
°
Stepper angle
×Driver subdivision
rack module ×gear teeth number ×
π
×transmission ratio
►
Helical rack
:
pulse =
360
°
Stepper angle
×Driver subdivision ×cos
rack module ×gear teeth number ×
π
×transmission ratio
Pulley&belt drive
:
pulse =
360
°
Stepper angle
×Driver subdivision
π
d×transmission ratio
d
:
pulley diameter
2.
Pulse equivalent of linear axis
e.g.
:
pulse/rev=1600
,
results retain up to three decimal places
Screw drive
screw pitch=5mm
,
pulse equivalent=
1600
5
=320
Rack drive
rack module
:
1.25,gear teeth number
:
23,π
:
3.141592654,transmission ratio
:
1/5(0.2)
19°31′42″
(
≈19.52833333°
)
►
Straight rack
pulse equivalent =
1600
1.25×23×3.141592654 ×0.2
= 88.573