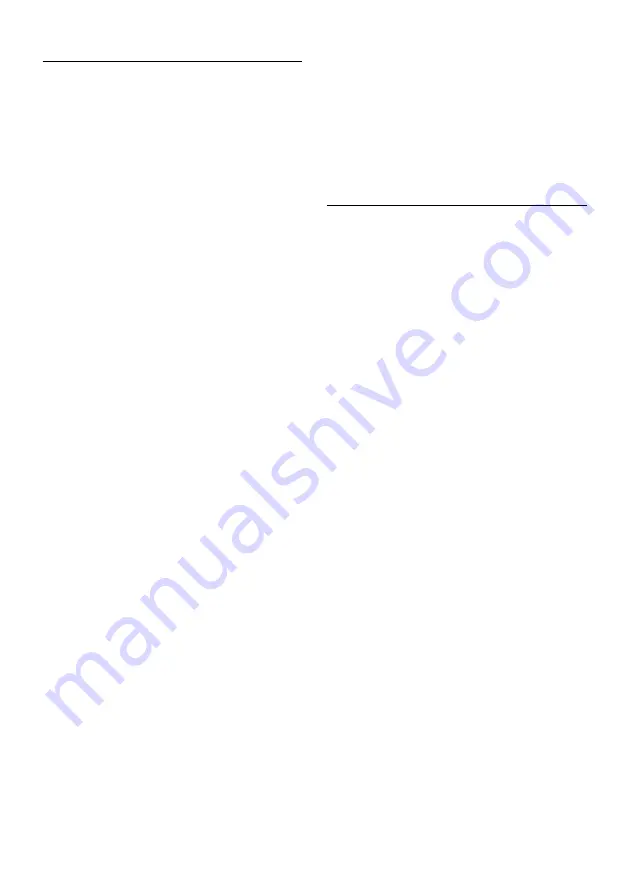
Repair and Maintenance
Cleaning
Caution!
Always disconnect the mains plug for all adjustment and main-
tenance work! Risk of serious injuries or damage due to inad-
vertent starting up of the device, or hazard due to electric shock!
1. After use, thoroughly clean all chips from the machine using a
brush or handbrush. Do not use compressed air for cleaning.
2. Regularly lubricate or oil all moving parts, spindles and
guides!
The outside of the housing can be cleaned with a soft, dry or
damp cloth. It is possible to use mild soap or other suitable
cleaning agent here. Solvents or cleaning agents containing al-
cohol (e.g. petrol, cleaning alcohol etc.) should be avoided, since
these can attack the plastic housing casings as well as wash off
the lubricants.
Please observe:
Changing the power supply cord may only be carried out by our
Proxxon-Service-Department or a qualified specialist!
Adjusting the play of the guides (Fig. 13)
Note:
Even if the guides are regularly lubricated or oiled, it is un-
avoidable that the guides will exhibit play after some time due to
wear.
The procedure described here using the example of the upper
carriage is the same for all guides, therefore it applies analo-
gously to the other guides on your lathe. For that reason they will
not be treated separately here. Adjust the guides according to the
motto: As "tightly" as necessary, as easy running as possible!
Please consider: If guides are set too closely, this causes high-
er operating forces as well as increased wear!
1. Release and slightly unscrew the counter nuts 1 (Fig. 13) of
the adjusting screws 2 for the upper carriage 3 using an open-
end spanner 5.
2. Evenly turn in the adjusting screws 2 with an Allen key 4 un-
til the play is eliminated.
3. Retighten the counter nuts 1. In the process, hold the ad-
justing screws 2 in position with the fixed spanner 5 so that
they do not misadjust again.
4. Then check if the support can still be moved easily and if it
runs completely without play.
Adjusting the play of the handwheels (Fig. 14):
Just as for the guides, handwheel wear during operation cannot
be avoided which ensures that the backlash increases slowly
but consistently. To minimise this again, please proceed as fol-
lows:
1. Hold on to the handwheel 1 and release the cap nut 2.
2. Turn the handwheel slightly to the right.
3. Retighten the cap nut while still holding the handwheel.
Please consider here as well:
The complete elimination of the backlash and a too "tight" ad-
justment for the handwheels is unreasonable: If the handwheels
are set too closely, this causes higher operating forces as well
as increased wear here as well!
Accessories for the FD 150/E
Cutting tool set (Article 24524)
The contents of the cutting tool set were already introduced in
the chapter "Select cutting tool"
Ring gear drill chuck (Article 24152)
Drills with sizes 0.5 to 6.5 mm can be clamped in the drill chuck
to manufacture holes on the plane side.
Inserting the drill chuck (Fig. 15)
1. Remove the travelling lathe centre from the quill as explained
at "Working with the tailstock".
2. Appropriately clean off the grease and dirt from the cone of
the chuck 1 and quill 2.
3. Insert the collar into the quill and firmly push on the drill
chuck.
4. Clamp the drill.
5. The complete tailstock 3 can now be moved up to the work-
piece to be machined after the clamping lever 4 has been re-
leased. Then tighten clamping screw 4.
6. Turn the handwheel 5 to move the drill up to the workpiece.
7. Switch on the machine and turn the handwheel 5 to lower the
drill to the required depth in the workpiece.
A tip: If the drill is set down very lightly, the scale ring 6 can be
"zeroised". This enables the manufacture of drill holes with a de-
fined depth by observing the scale markings and counting the
handwheel revolutions during infeed: One revolution will tra-
verse the drill by 1 mm.
Multiple range ER 11 collets (Article 24154)
The collets are particularly suitable for machining round parts
with great precision. The true running accuracy is considerably
higher here than when working with a jaw chuck.
Caution!
It is possible to use workpieces with diameters of up to 0.5 mm
below the nominal diameter of the collet.
- 22 -
Содержание FD 150/E
Страница 1: ...DE GB FR IT ES NL DK SE CZ TR PL RU MANUAL Drehmaschine FD 150 E...
Страница 3: ...3 NOTIZEN...
Страница 5: ...5 Fig 7 Fig 7a Fig 7b 1 1 4 2 Fig 9 3 4 5 2 1 6 a b c d Fig 10 Fig 11 Fig 8 a b c d e f...
Страница 109: ...PROXXON PROXXON 85 16 1 1 2 3 4 5 6 7 8 9 10 11 12 13 14 15 16 17 18 19 109...
Страница 111: ...2 2b FD 150 E PROXXON 2 2 1 2 3 4 3 1 2 2 3 1 2 3 3 111...
Страница 112: ...1 3 4 2 10 2 3 1 5 3 5 4 6 4 4 2 4 1 2 3 0 1 4 4 2 3 2 5 1 60 1 0 1 2 3 2 6 3 5 1 1 5 1 4 2 4 7 3 4 5 1 6 1 8 5 8 112...
Страница 113: ...2 3 7 7a 7a 7b 1 3 2 1 2 3 3 3 4 3 2 5 2 1 6 7 1 2 3 8 24524 b d f 9 6 6 113...
Страница 114: ...114 1 1 9 2 2 1 3 4 4 800 5000 10 1 1 2 2 3 3 4 4 3 5 5 1 1 6 10 11...
Страница 115: ...115 1 2 3 4 5 6 1 7 8 9 10 b 1 2 3 2 45 d 1 2 12 1 2 3 5 4 2 6 2 5 3...
Страница 116: ...6 5 3 1 7 1 6 2 8 3 9 4 1 2 PROXXON 13 1 1 13 2 3 5 2 2 4 3 1 2 5 4 Fig 14 1 2 2 3 FD 150 E 24524 24152 0 5 6 5 15 1 116...
Страница 123: ...4 1 2 5 3 6 123 4 3 2 1 5 Fig 12 6 4 Fig 13 Fig 14 Fig 16 Fig 16a Fig 15 2 1 5 4 3 1 2 1 3 2 4 5 6 7...