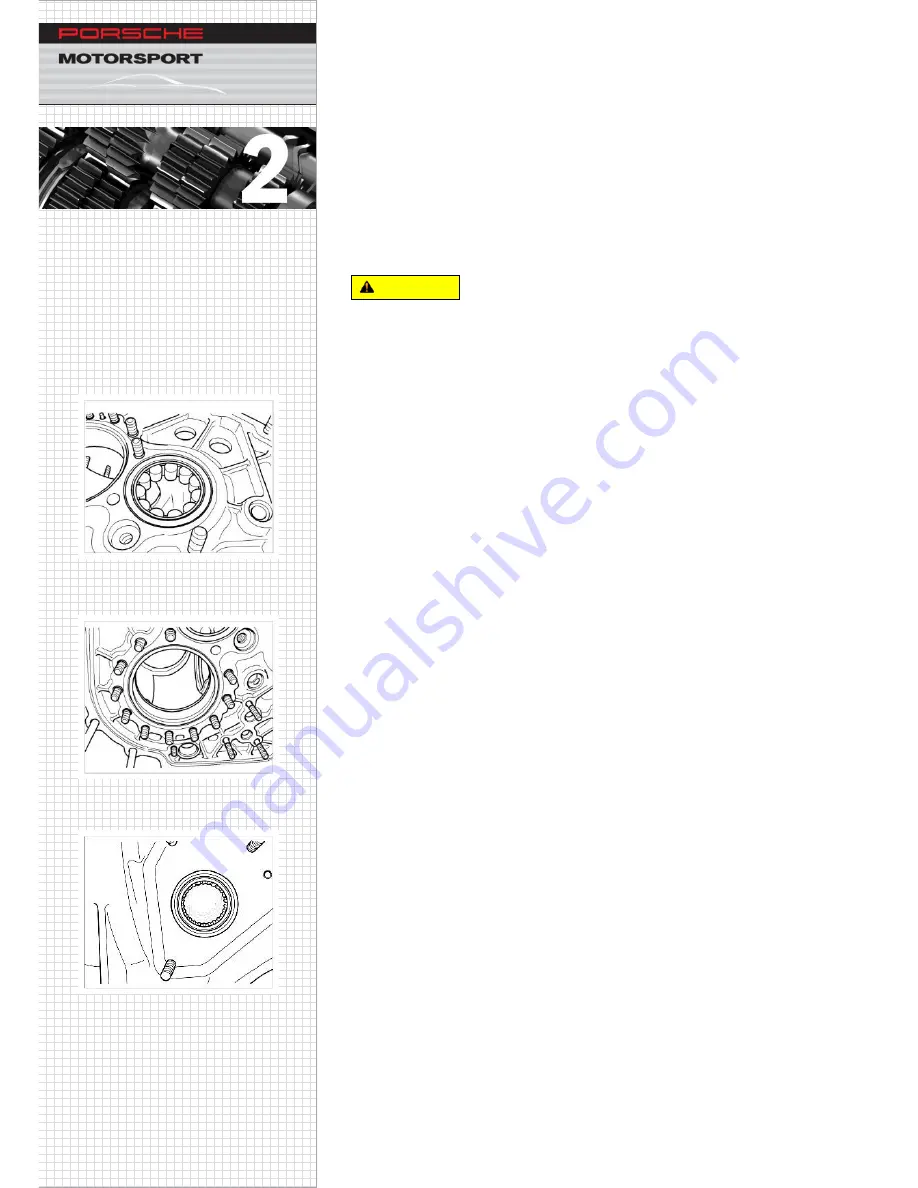
Version: 4/20/2018
2
102
Powertrain
911 GT3 Cup (991 II)
MY 2018
Bearing assembly
Inserting the bearings requires the heating of the gearbox housing analogous to the
setting of the adhesive connection (see above). All bearings must be inserted quickly
before the housing has cooled off. To ensure the proper seat of the bearings, all
bearings must be tapped with an appropriate tool after the housing has cooled off.
Hot components
Danger of burns
Wear personal protective equipment.
Drive shaft bearing
Dimensions:
34x62x17
Type:
Cylinder roll bearing
Tool:
No. 1
Pinion shaft cylinder roll bearing (outer ring)
Dimensions:
40x90x23
Type:
Cylinder roll bearing
Tool:
No. 3
Input shaft/connecting shaft bearing
Dimensions:
30x37x16
Type:
Needle bearing
Tool:
No. 14
2.9.1.12
2.9.1.10
2.9.1.11
Caution
Содержание 911 GT3 Cup 2018
Страница 1: ...Technical manual 911 GT3 Cup 991 II MY 2018 ...
Страница 17: ...Version 4 20 2018 911 GT3 Cup 991 II MY 2018 16 Preface ...
Страница 224: ...Version 4 20 2018 223 Bodywork 911 GT3 Cup 991 II MY 2018 Side view 4 2 2 ...
Страница 351: ...Version 4 20 2018 350 Electrical system 911 GT3 Cup 991 II MY 2018 ...
Страница 369: ...Version 4 20 2018 368 Maintenance 911 GT3 Cup 991 II MY 2018 7 1 1 1 60 sec ...