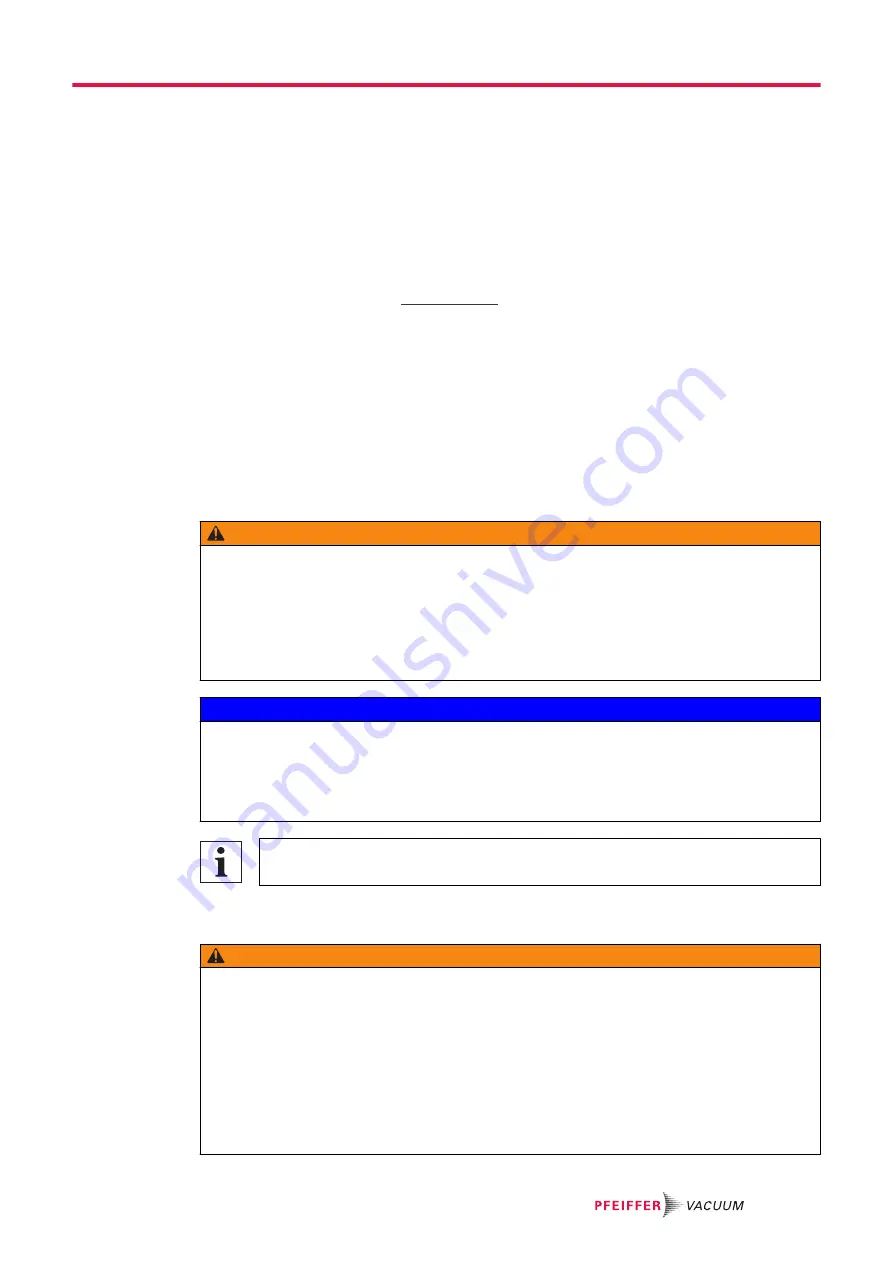
General instructions for installing the pump in the pumping line in accordance with industry
best practice
The inlet and exhaust connections must not put undue strain on the pumping line that could cause leak-
age.
1. Wear gloves to connect and remove the pump from the equipment.
2. Always complete the mechanical installation before the electrical connection.
3.
Avoid connecting a reducing flange to the pump inlet
. Contact us if necessary.
4.
Check that the splinter shield is installed in the inlet flange.
5. Only use accessories on the pumping line, for the inlet and exhaust lines, with materials and seal-
ing properties that are compatible with the gases being pumped. Refer to the connection accesso-
ries catalog available at the
website.
6. When assembling the pumping line, include accessories for isolating the pump from the pumping
line and making maintenance easier to carry out (pump inlet and exhaust isolation valves, purge
valves, etc.).
7. The O-rings located under the blanking plates are not compatible with all applications.
Product
users or integrators are responsible for installing O-rings compatible with the application
.
8. Remove the blanking plates used to seal the inlet and exhaust ports.
9. Keep the blanking plates, screws and washers for reuse when transporting the pump.
10. Ensure that no screws, washers or other objects are dropped into the pump inlet.
11. Perform a leak test on the entire pumping line after installation.
5.3.1 Pump inlet connection
WARNING
Risk of cutting injuries due to contact with sharp edges via the high vacuum flange
Sharp components can be accessed via the inlet flange. Rotor and stator blades on turbomolecular
pumps have very sharp edges.
► Before starting any work on the product, wait for the pump to come to a complete standstill.
► Always keep the splinter shield in the inlet housing, as it limits the risk of injury.
► Always wear protective gloves in accordance with standard EN 420.
►
Never disconnect the high vacuum flange before the rotor is completely immobilized
.
NOTICE
Failure to meet cleanliness requirements poses a risk of process contamination
When parts in contact with high vacuum are dirty, pumping time increases and the process is conta-
minated.
► Use only dry parts and clean, grease-free, dust-free pipelines.
► Wear gloves when making connections, especially on the high vacuum side.
Make sure that the parts or chambers connected to the inlet of our products can withstand
a negative pressure of 1·10
-3
hPa relative to atmospheric pressure.
5.3.2 Pump exhaust connection
WARNING
Risk of poisoning when process gases are present in the atmosphere
The manufacturer has no control over the types of gases used with the pump. Process gases are of-
ten toxic, flammable, corrosive, explosive and/or otherwise reactive. There is a risk of serious or fatal
injury if these gases are allowed to escape freely into the atmosphere.
► Apply the relevant safety instructions in accordance with local regulation. This information is
available from the operator’s safety department.
►
Always connect the turbomolecular pump’s exhaust to a backing pump compatible with
process gases
: the backing pump’s exhaust is connected to the installation’s dangerous gas ex-
traction system
► Regularly check that there are no leaks where the pump connects to the exhaust pipework.
Installation
27/78